Chemical vapor deposition (CVD) is a widely used thin-film deposition technique with numerous advantages, such as high purity, uniformity, scalability, and versatility, making it suitable for applications like electrical circuits and complex surface coatings. However, it also has limitations, including high equipment and precursor gas costs, high operating temperatures, and challenges in coating large or complex materials. Below, we explore the pros and cons of CVD in detail.
Key Points Explained:
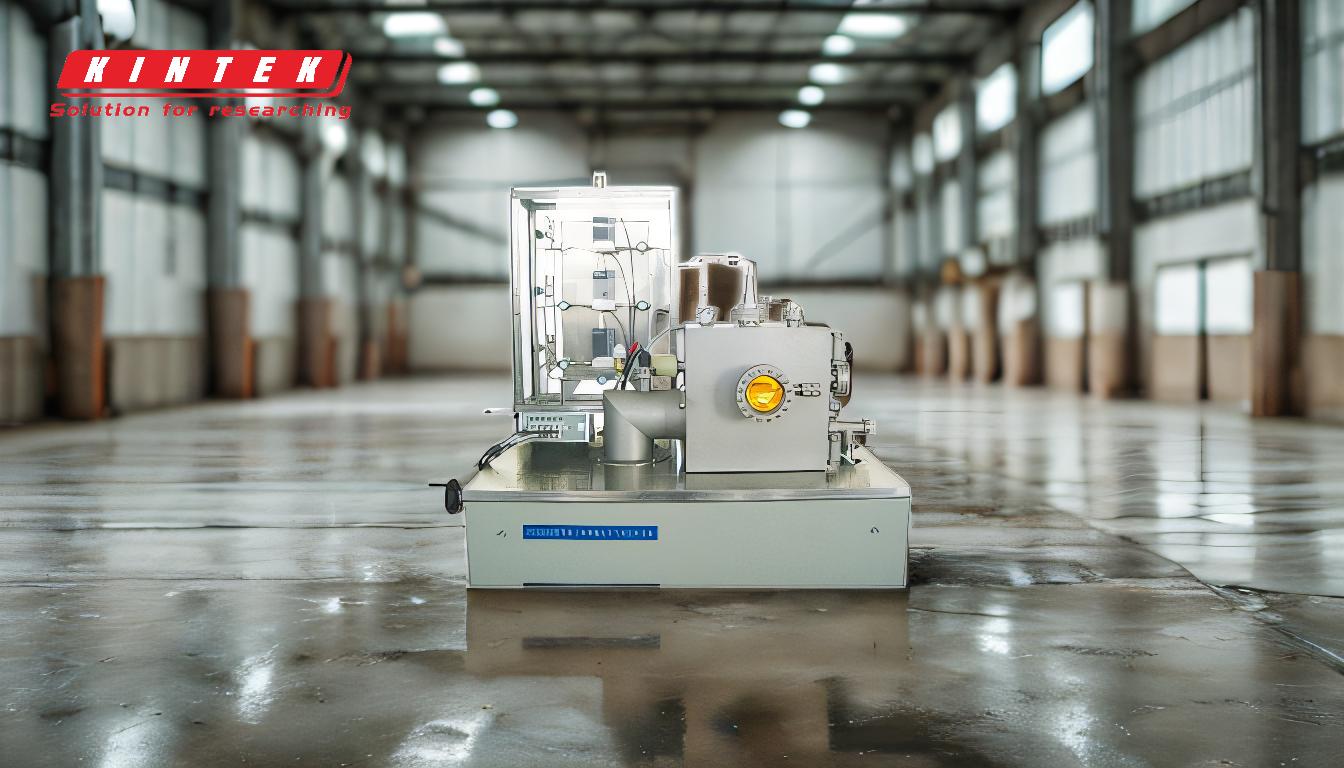
Advantages of Chemical Vapor Deposition (CVD):
-
High Purity and Density of Films:
- CVD produces thin films with extremely high purity and density, which are critical for applications requiring precise material properties, such as semiconductors and optical coatings.
- The process relies on chemical reactions, ensuring minimal contamination and high-quality results.
-
Uniformity and Control:
- CVD allows precise control over the thickness, composition, and microstructure of the deposited films, enabling tailored properties for specific applications.
- The films are uniform both within the layer and across the substrate surface, making it ideal for large-area coatings.
-
Versatility in Materials and Substrates:
- CVD can deposit a wide range of materials, including metals, semiconductors, ceramics, and polymers.
- It is compatible with various substrate materials, such as metals, glass, and plastics, making it highly adaptable to different industries.
-
Scalability and High Deposition Rates:
- CVD is scalable, suitable for both small-scale research and large-scale industrial production.
- It offers high deposition rates, making it efficient for producing large-area thin films quickly.
-
Wrap-Around Properties for Complex Surfaces:
- CVD can uniformly coat irregular or complex-shaped surfaces due to its non-line-of-sight nature, making it ideal for precision components and intricate designs.
-
Durable and High-Performance Coatings:
- The coatings produced by CVD are durable and can withstand high-stress environments, extreme temperatures, and temperature variations.
- Gases used in CVD can be optimized for specific properties, such as corrosion resistance or abrasion resistance.
-
Simple and Easy-to-Operate Equipment:
- CVD equipment is relatively simple to operate and maintain, reducing operational complexity and downtime.
Disadvantages of Chemical Vapor Deposition (CVD):
-
High Equipment and Precursor Gas Costs:
- The initial investment in CVD equipment is high, and the precursor gases used in the process can be expensive, increasing overall costs.
-
High Operating Temperatures:
- CVD typically requires high temperatures, which can limit its use with temperature-sensitive materials and substrates.
- High temperatures can also lead to residual stress in the coating and substrate, requiring careful control of deposition parameters.
-
Limited On-Site Application:
- CVD is usually performed in specialized coating centers rather than on-site, which can be inconvenient for certain applications.
- All parts must be disassembled into individual components for coating, adding complexity to the process.
-
Size Constraints Due to Vacuum Chambers:
- The size of the vacuum chamber limits the ability to coat larger surfaces, restricting its use for large-scale applications.
-
All-or-Nothing Coating Process:
- CVD is an all-or-nothing process, meaning it is difficult to partially coat materials or achieve selective coverage.
-
Potential Hazards from Precursor Gases:
- Some precursor gases used in CVD can be hazardous, requiring strict safety measures and handling protocols.
-
Challenges in Achieving Complete Coverage:
- While CVD can coat complex surfaces, achieving complete and uniform coverage can be challenging, especially for intricate geometries.
Conclusion:
CVD is a highly versatile and effective method for thin-film deposition, offering advantages such as high purity, uniformity, and scalability. Its ability to coat complex surfaces and produce durable, high-performance films makes it indispensable in industries like electronics, optics, and aerospace. However, its high costs, high operating temperatures, and limitations in coating large or temperature-sensitive materials are notable drawbacks. Understanding these pros and cons is essential for selecting CVD as the appropriate deposition technique for specific applications.
Summary Table:
Aspect | Advantages | Disadvantages |
---|---|---|
Purity and Density | High purity and density of films, ideal for semiconductors and optical coatings. | High equipment and precursor gas costs. |
Uniformity and Control | Precise control over thickness, composition, and microstructure. | High operating temperatures, limiting use with temperature-sensitive materials. |
Versatility | Deposits a wide range of materials and compatible with various substrates. | Limited on-site application; requires specialized coating centers. |
Scalability | Scalable for both small-scale research and large-scale production. | Size constraints due to vacuum chambers, limiting large-scale applications. |
Complex Surfaces | Uniformly coats irregular or complex-shaped surfaces. | All-or-nothing coating process; difficult to achieve selective coverage. |
Durability | Produces durable, high-performance coatings for extreme environments. | Potential hazards from precursor gases, requiring strict safety measures. |
Ease of Use | Simple and easy-to-operate equipment. | Challenges in achieving complete coverage for intricate geometries. |
Ready to explore how CVD can enhance your applications? Contact us today for expert guidance!