Sieving is a widely used method for particle size analysis due to its simplicity, cost-effectiveness, and reliability. It offers several advantages, such as ease of use, low investment costs, quick and reproducible results, and the ability to separate particles into distinct size fractions. However, it also has limitations, including potential inaccuracies with irregularly shaped particles, limited resolution for very fine particles, and challenges with materials that are prone to clumping or static. Below is a detailed exploration of the pros and cons of sieving.
Key Points Explained:
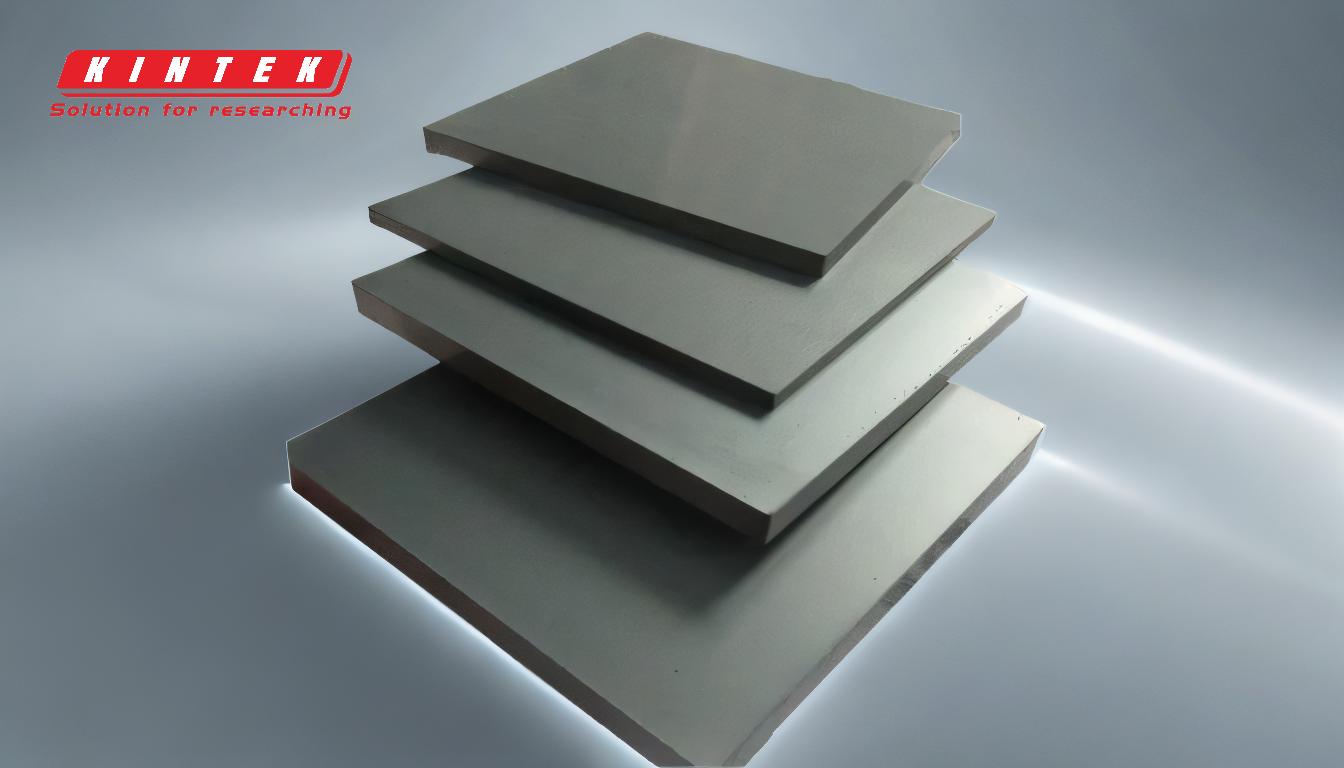
-
Advantages of Sieving:
-
Ease of Use:
- Sieving is a straightforward and intuitive process that does not require extensive training or expertise. The equipment is simple to operate, making it accessible for a wide range of users.
-
Minimal Investment Costs:
- Compared to other particle size analysis techniques, such as laser diffraction or dynamic light scattering, sieving equipment is relatively inexpensive. This makes it a cost-effective option for laboratories and industries with budget constraints.
-
Accurate and Reproducible Results:
- Sieving provides consistent and reliable results when performed correctly. The method is well-standardized, and the use of certified sieves ensures accuracy in particle size distribution measurements.
-
Short Analysis Time:
- Sieving can be completed quickly, especially for dry materials. This makes it suitable for high-throughput environments where rapid results are needed.
-
Separation of Particle Size Fractions:
- Sieving allows for the physical separation of particles into distinct size fractions. This is particularly useful for applications requiring specific particle size ranges, such as in construction materials or pharmaceutical formulations.
-
Ease of Use:
-
Disadvantages of Sieving:
-
Challenges with Irregularly Shaped Particles:
- Sieving assumes particles are spherical or near-spherical. Irregularly shaped particles may not pass through sieve openings as expected, leading to inaccuracies in size distribution measurements.
-
Limited Resolution for Fine Particles:
- Sieving is less effective for analyzing very fine particles (typically below 50 microns). Fine particles can clog sieve openings or adhere to each other due to static electricity, reducing the accuracy of results.
-
Material-Specific Limitations:
- Some materials, such as those that are sticky, hygroscopic, or prone to clumping, are difficult to sieve effectively. These materials may require additional preparation, such as drying or dispersing agents, which can complicate the process.
-
Wear and Tear of Sieves:
- Over time, sieves can become worn or damaged, leading to changes in the size of sieve openings. Regular calibration and maintenance are necessary to ensure consistent results.
-
Manual Labor and Operator Dependency:
- While sieving is simple, it can be labor-intensive, especially for large sample volumes. The results may also be influenced by the operator’s technique, such as the duration and intensity of shaking.
-
Challenges with Irregularly Shaped Particles:
-
Applications and Suitability:
-
Ideal Applications:
- Sieving is well-suited for coarse to medium-sized particles, particularly in industries like construction, mining, agriculture, and food processing. It is also useful for quality control in manufacturing processes.
-
Less Suitable Applications:
- For fine powders or nanoparticles, alternative methods like laser diffraction or sedimentation analysis may provide more accurate and detailed results.
-
Ideal Applications:
-
Comparison with Other Particle Size Analysis Methods:
-
Advantages Over Other Methods:
- Sieving is more cost-effective and simpler than techniques like laser diffraction or dynamic light scattering. It also provides a physical separation of particles, which can be beneficial for downstream processing.
-
Limitations Compared to Other Methods:
- Other methods offer higher resolution and can handle a broader range of particle sizes, including sub-micron particles. They are also less affected by particle shape and material properties.
-
Advantages Over Other Methods:
-
Best Practices for Sieving:
-
Proper Sieve Selection:
- Choose sieves with appropriate mesh sizes for the particle size range of interest. Ensure sieves are certified and regularly calibrated.
-
Sample Preparation:
- Dry or disperse the sample if necessary to prevent clumping or static interference. Use a representative sample size to ensure accurate results.
-
Consistent Technique:
- Follow standardized procedures for sieving, including consistent shaking duration and intensity. Automated sieve shakers can help reduce operator variability.
-
Proper Sieve Selection:
In summary, sieving is a practical and cost-effective method for particle size analysis, particularly for coarse to medium-sized particles. Its ease of use, low cost, and ability to separate size fractions make it a valuable tool in many industries. However, it has limitations with fine particles, irregularly shaped particles, and certain material properties. Understanding these pros and cons helps in selecting the appropriate method for specific applications and ensuring accurate and reliable results.
Summary Table:
Aspect | Advantages | Disadvantages |
---|---|---|
Ease of Use | Simple and intuitive; minimal training required | Labor-intensive for large samples; operator-dependent results |
Cost | Low investment costs compared to other methods | Wear and tear of sieves requires regular maintenance |
Accuracy | Reliable and reproducible results with certified sieves | Inaccuracies with irregularly shaped particles |
Resolution | Effective for coarse to medium-sized particles | Limited resolution for fine particles (below 50 microns) |
Material Suitability | Works well for dry, non-sticky materials | Challenges with sticky, hygroscopic, or clumping materials |
Analysis Time | Quick results, especially for dry materials | May require additional preparation for certain materials |
Applications | Ideal for construction, mining, agriculture, and food processing industries | Less suitable for fine powders or nanoparticles |
Need help choosing the right particle size analysis method? Contact our experts today for personalized advice!