Pyrolysis reactors are essential equipment for converting biomass or other organic materials into valuable products like bio-oils, syngas, and biochar. The choice of reactor depends on factors such as the type of feedstock, desired products, processing capacity, and operational efficiency. Common reactors include fluidized bed, fixed bed, rotary kiln, vacuum, and ablative reactors, each with unique characteristics and advantages. These reactors are designed to handle high temperatures and pressures, ensuring efficient heat transfer and optimal product yields. Understanding the different types of reactors and their applications is crucial for selecting the right system for specific pyrolysis processes.
Key Points Explained:
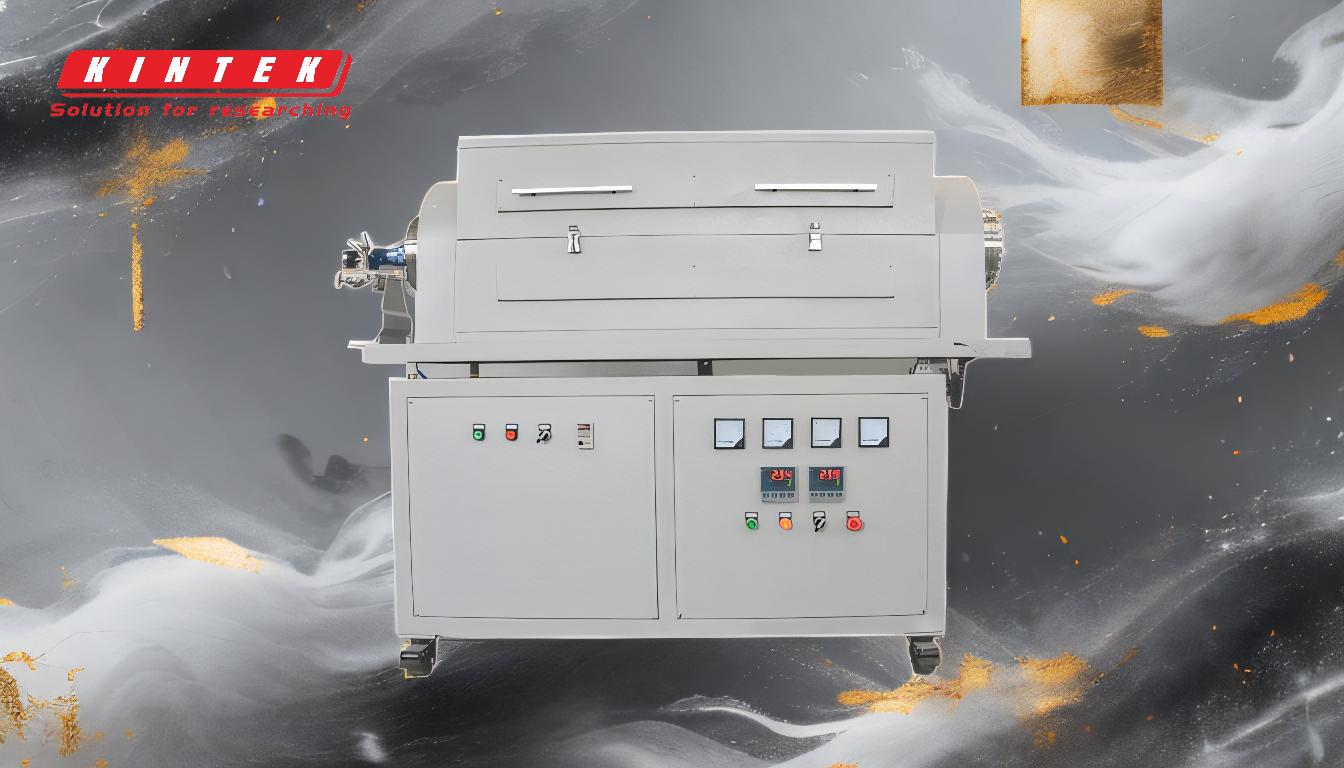
-
Fluidized Bed Reactors
- Types: Includes bubbling fluidized bed and circulating fluidized bed reactors.
- Mechanism: Biomass particles are suspended in a gas or liquid medium, allowing for even heating and rapid heat transfer.
- Advantages: High heat transfer rates, uniform temperature distribution, and scalability for large-scale operations.
- Applications: Widely used for fast pyrolysis to produce bio-oils and syngas.
-
Fixed Bed Reactors
- Design: Biomass is placed in a stationary bed, and heat is applied either directly or indirectly.
- Advantages: Simple design, low operating costs, and suitability for small-scale operations.
- Limitations: Slower heat transfer and less uniform temperature distribution compared to fluidized beds.
- Applications: Commonly used for slow pyrolysis to produce biochar.
-
Rotary Kiln Reactors
- Mechanism: Biomass is fed into a rotating drum, where it is heated indirectly to avoid contamination.
- Advantages: Continuous operation, reduced risk of contamination, and flexibility in handling various feedstocks.
- Applications: Suitable for both fast and slow pyrolysis processes, often used in industrial settings.
-
Vacuum Reactors
- Mechanism: Operates under reduced pressure to lower the boiling points of volatile compounds, facilitating their removal.
- Advantages: Minimizes secondary reactions, leading to higher-quality bio-oil.
- Applications: Ideal for producing high-quality bio-oils from biomass.
-
Ablative Reactors
- Mechanism: Biomass is pressed against a heated surface, causing rapid pyrolysis at the contact point.
- Advantages: High heat transfer rates and no need for fine particle size.
- Applications: Effective for fast pyrolysis, especially with high-moisture feedstocks.
-
Screw and Auger Reactors
- Mechanism: Biomass is conveyed through a heated screw or auger, allowing for continuous processing.
- Advantages: Compact design, continuous operation, and ease of automation.
- Applications: Suitable for small to medium-scale pyrolysis operations.
-
Cyclonic and Vortex Reactors
- Mechanism: Biomass particles are subjected to high-velocity gas streams, causing rapid heating and pyrolysis.
- Advantages: Extremely fast processing times and high throughput.
- Applications: Used in rapid pyrolysis for bio-oil production.
-
Batch and Semi-Batch Reactors
- Design: Operates in discrete cycles, with biomass loaded, processed, and unloaded in batches.
- Advantages: Flexibility in feedstock and process conditions, suitable for research and small-scale production.
- Limitations: Lower throughput compared to continuous systems.
- Applications: Commonly used in laboratory and pilot-scale studies.
-
Other Reactor Types
- Drum Reactors: Similar to rotary kilns but with a simpler design, often used for slow pyrolysis.
- Tubular Reactors: Long, heated tubes where biomass is pyrolyzed as it moves through.
- Wire Mesh Reactors: Used for fundamental studies of pyrolysis kinetics due to their precise control over temperature and residence time.
-
Selection Criteria
- Feedstock Type: Different reactors are better suited for specific feedstocks (e.g., fluidized beds for fine particles, rotary kilns for bulky materials).
- Product Requirements: The desired end products (bio-oil, syngas, biochar) influence reactor choice.
- Scale of Operation: Batch reactors are ideal for small-scale or experimental setups, while continuous systems like fluidized beds are better for large-scale production.
- Heat Transfer Efficiency: Reactors with high heat transfer rates (e.g., fluidized beds, ablative reactors) are preferred for fast pyrolysis.
By understanding the strengths and limitations of each reactor type, stakeholders can make informed decisions to optimize their pyrolysis processes for specific applications.
Summary Table:
Reactor Type | Mechanism | Advantages | Applications |
---|---|---|---|
Fluidized Bed | Biomass suspended in gas/liquid for even heating | High heat transfer, uniform temperature, scalable | Fast pyrolysis (bio-oils, syngas) |
Fixed Bed | Biomass in stationary bed, heated directly/indirectly | Simple design, low cost, small-scale suitability | Slow pyrolysis (biochar) |
Rotary Kiln | Biomass fed into rotating drum, heated indirectly | Continuous operation, flexible feedstock handling | Fast/slow pyrolysis (industrial) |
Vacuum | Operates under reduced pressure to lower boiling points | High-quality bio-oil, minimizes secondary reactions | High-quality bio-oil production |
Ablative | Biomass pressed against heated surface for rapid pyrolysis | High heat transfer, no fine particle size needed | Fast pyrolysis (high-moisture feed) |
Screw/Auger | Biomass conveyed through heated screw/auger | Compact, continuous, easy automation | Small-medium scale pyrolysis |
Cyclonic/Vortex | Biomass subjected to high-velocity gas streams | Extremely fast processing, high throughput | Rapid pyrolysis (bio-oil) |
Batch/Semi-Batch | Operates in discrete cycles | Flexible feedstock, suitable for research/small-scale | Lab/pilot-scale studies |
Drum/Tubular/Wire Mesh | Various designs for specific needs | Versatile, precise control | Slow pyrolysis, kinetic studies |
Need help selecting the right pyrolysis reactor? Contact our experts today for tailored solutions!