Slow pyrolysis is a thermal decomposition process that occurs at relatively low heating rates and longer residence times, typically used to maximize char production. The choice of reactor is critical for achieving the desired outcomes in slow pyrolysis. Common reactors for slow pyrolysis include fixed bed reactors, rotary kiln reactors, and certain types of fluidized bed reactors. Each reactor type has unique characteristics that make it suitable for specific applications, such as heat transfer efficiency, residence time control, and feedstock handling capabilities. Below, we explore the key aspects of reactors used in slow pyrolysis.
Key Points Explained:
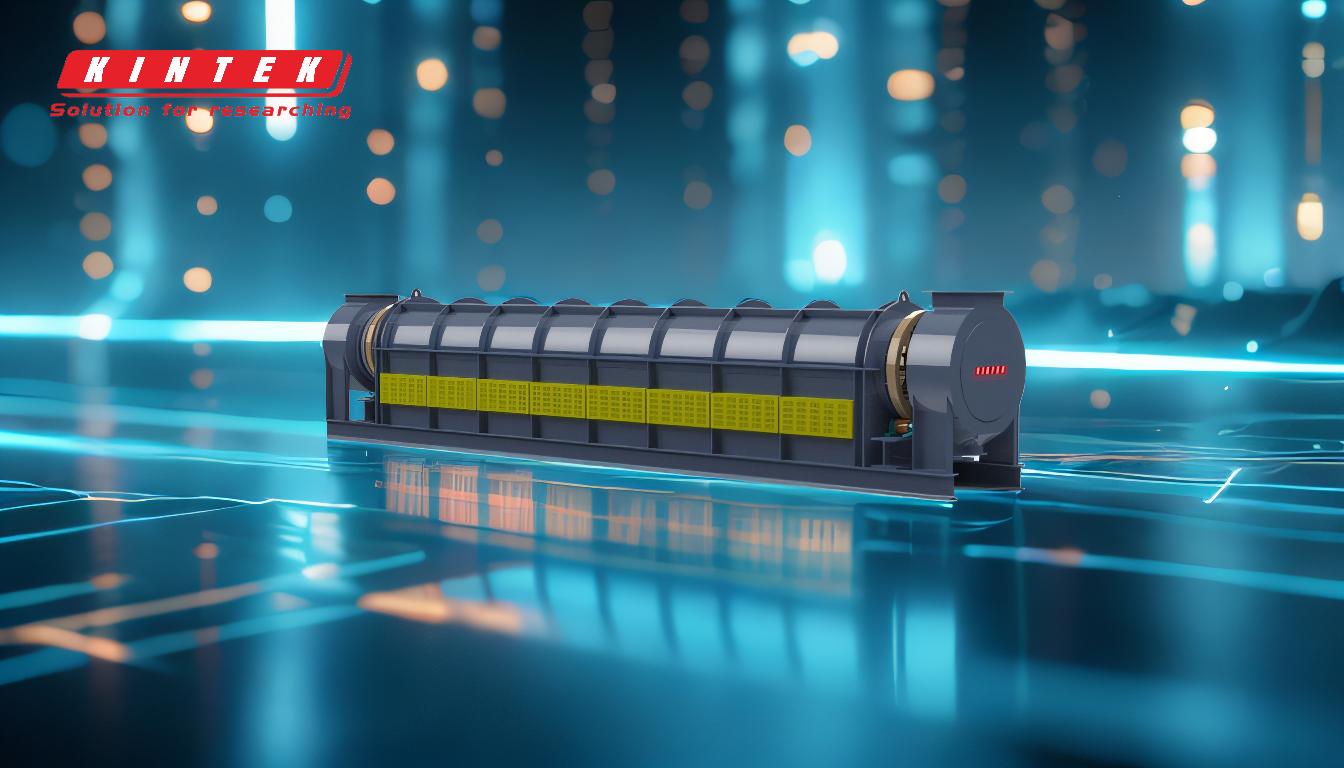
-
Fixed Bed Reactors
- Fixed bed reactors are one of the most commonly used reactors for slow pyrolysis.
- They operate by placing the feedstock in a stationary bed, where it is heated indirectly or directly.
- These reactors are ideal for slow pyrolysis due to their ability to maintain longer residence times, which is essential for maximizing char production.
- They are simple in design and cost-effective, making them suitable for small-scale operations.
- However, they may have limitations in terms of heat transfer efficiency and scalability for larger operations.
-
Rotary Kiln Reactors
- Rotary kiln reactors are another popular choice for slow pyrolysis.
- They use indirect heating to break down materials, which reduces the risk of contamination and ensures uniform heating.
- The rotating motion of the kiln helps mix the feedstock, improving heat transfer and reaction efficiency.
- These reactors are versatile and can handle a wide range of feedstocks, including biomass and waste materials.
- They are particularly useful for slow pyrolysis because they allow for precise control over temperature and residence time.
-
Fluidized Bed Reactors
- While fluidized bed reactors are more commonly associated with fast pyrolysis, certain types can be adapted for slow pyrolysis.
- Bubbling fluidized bed reactors, for example, can be used for slow pyrolysis by adjusting the operating conditions to achieve longer residence times.
- These reactors suspend the feedstock in a gas or liquid, allowing for even heating and efficient heat transfer.
- They are highly efficient and scalable, making them suitable for both small and large-scale operations.
- However, they may require more complex design and higher operational costs compared to fixed bed or rotary kiln reactors.
-
Key Considerations for Reactor Selection
- Heat Transfer Efficiency: The reactor must ensure efficient heat transfer to the feedstock to achieve uniform pyrolysis.
- Residence Time Control: Slow pyrolysis requires longer residence times, so the reactor must be capable of maintaining these conditions.
- Feedstock Handling: The reactor should be able to handle the specific type of feedstock being used, whether it is biomass, waste, or other materials.
- Scalability: The reactor design should allow for scalability depending on the intended application, whether small-scale or industrial.
By understanding the unique characteristics of each reactor type, purchasers can make informed decisions based on their specific needs and goals for slow pyrolysis.
Summary Table:
Reactor Type | Key Features | Best For |
---|---|---|
Fixed Bed Reactors | Simple design, cost-effective, longer residence times | Small-scale operations, char production |
Rotary Kiln Reactors | Indirect heating, uniform heating, precise temperature control | Versatile feedstock handling |
Fluidized Bed Reactors | Efficient heat transfer, scalable, adjustable residence times | Large-scale operations, diverse feedstocks |
Looking for the right reactor for your slow pyrolysis process? Contact our experts today for tailored solutions!