The sieving method is a systematic process used to separate particles based on their size. It involves several critical steps, including sampling, sample division, selection of appropriate sieves and parameters, actual sieving, recovery of material, data evaluation, and cleaning of sieves. These steps ensure accurate and reliable results. Wet sieving, a variation of the method, uses a liquid medium to enhance separation efficiency. The process relies on the principle of relative motion between the sieve and particles, allowing smaller particles to pass through the mesh while retaining larger ones. Proper execution of each step is essential for achieving precise particle size analysis.
Key Points Explained:
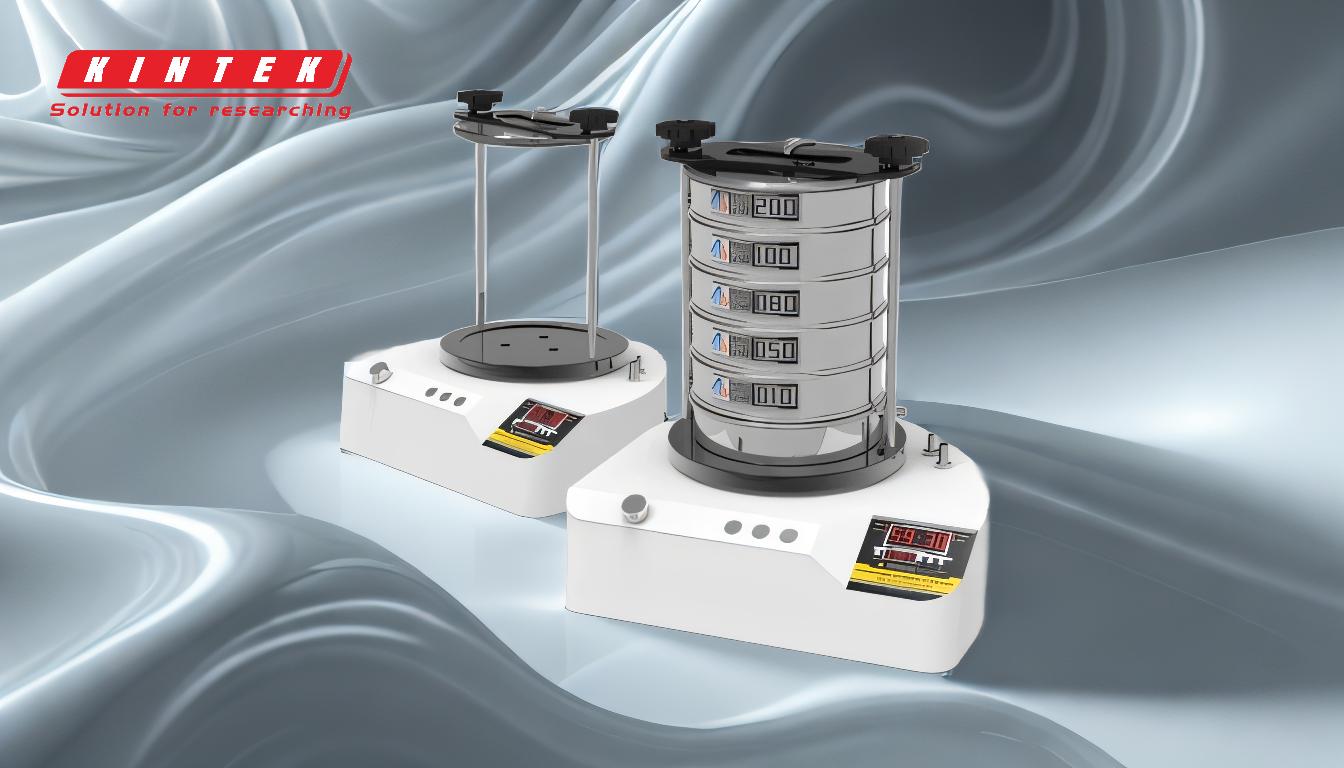
-
Sampling:
- The first step involves collecting a representative sample of the material to be analyzed. This ensures that the results reflect the true characteristics of the entire batch.
- Proper sampling techniques are crucial to avoid bias and ensure consistency.
-
Sample Division (if required):
- If the sample is too large, it may need to be divided into smaller, more manageable portions. This step ensures uniformity and reduces the risk of errors during sieving.
- Techniques like quartering or using a sample splitter can be employed for this purpose.
-
Selection of Suitable Test Sieves:
- Choosing the right sieves is critical for accurate separation. Sieves with different mesh sizes are selected based on the expected particle size distribution of the sample.
- The mesh size should be appropriate for the material being analyzed to ensure that particles are effectively separated.
-
Selection of Sieving Parameters:
- Parameters such as sieving time, amplitude, and method (e.g., dry or wet sieving) are selected based on the material properties and desired outcomes.
- Proper parameter selection ensures efficient and accurate sieving.
-
Actual Sieve Analysis:
- The sample is placed on the top sieve of a stack, and the sieving process begins. The material is subjected to motion (vertical or horizontal), allowing particles to pass through the mesh according to their size.
- In wet sieving, a liquid medium is used to aid the separation process, particularly for fine particles or materials prone to agglomeration.
-
Recovery of Sample Material:
- After sieving, the material retained on each sieve is collected and weighed. This step provides data on the particle size distribution.
- In wet sieving, the residue is typically oven-dried before weighing to remove any moisture.
-
Data Evaluation:
- The weights of the material retained on each sieve are recorded and analyzed to determine the particle size distribution.
- This data is often presented in the form of a graph or table, providing insights into the material's characteristics.
-
Cleaning and Drying the Test Sieves:
- After the analysis, the sieves must be thoroughly cleaned and dried to remove any residual material. This step is essential to prevent cross-contamination in subsequent analyses.
- Proper maintenance of sieves ensures their longevity and accuracy.
By following these steps meticulously, the sieving method provides reliable and precise results, making it an essential tool in various industries for particle size analysis.
Summary Table:
Step | Description |
---|---|
1. Sampling | Collect a representative sample to ensure accurate results. |
2. Sample Division | Divide large samples for uniformity and reduced errors. |
3. Sieve Selection | Choose sieves with appropriate mesh sizes for effective separation. |
4. Parameter Selection | Set sieving time, amplitude, and method (dry/wet) based on material properties. |
5. Sieve Analysis | Perform sieving with motion to separate particles by size. |
6. Material Recovery | Collect and weigh retained material for particle size distribution data. |
7. Data Evaluation | Analyze weights to determine particle size distribution. |
8. Sieve Cleaning | Clean and dry sieves to prevent cross-contamination and ensure accuracy. |
Optimize your particle size analysis with expert guidance—contact us today!