Silicon Carbide (SiC) is a versatile material with a wide range of industrial applications, and its synthesis methods are critical to achieving the desired properties for specific uses. The primary industrial methods for synthesizing SiC include sintering, reaction bonding, crystal growth, and chemical vapor deposition (CVD). Additionally, the preparation of SiC powder, which is often a precursor for these methods, involves techniques such as the Acheson method, the silicon dioxide low-temperature carbothermal reduction method, and the silicon-carbon direct reaction method. Each method has unique characteristics that influence the final properties of the SiC, such as purity, grain size, and mechanical strength. Below, we explore these methods in detail, focusing on their processes, advantages, and applications.
Key Points Explained:
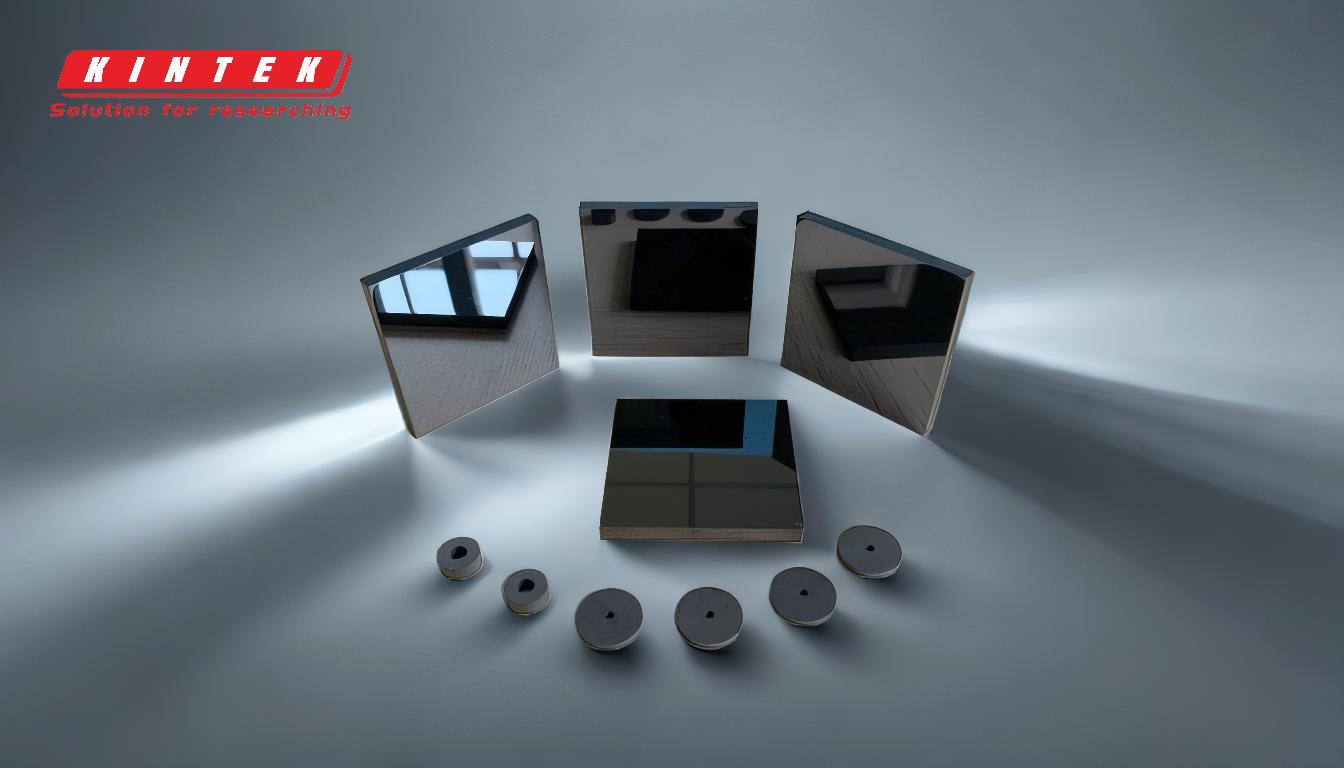
-
Acheson Method
- Process: The Acheson method is one of the earliest and most traditional methods for producing SiC. It involves a high-temperature electro-chemical reaction between sand (silicon dioxide, SiO₂) and carbon (C) in an electric resistance furnace at temperatures around 2200°C to 2500°C. The reaction can be summarized as: [ \text{SiO}_2 + 3\text{C} \rightarrow \text{SiC} + 2\text{CO} ]
- Advantages: This method is cost-effective and capable of producing large quantities of SiC. It is widely used for industrial-grade SiC production.
- Applications: The SiC produced by this method is often used in abrasive materials, refractory materials, and as a raw material for further processing into other forms of SiC.
-
Silicon Dioxide Low-Temperature Carbothermal Reduction Method
- Process: This method involves the reduction of silicon dioxide (SiO₂) with carbon at relatively lower temperatures (typically below 1600°C) compared to the Acheson method. The reaction is similar but occurs at a lower temperature, which can be controlled to produce finer SiC powders.
- Advantages: Lower energy consumption and the ability to produce finer and more uniform SiC particles compared to the Acheson method. This method is suitable for producing high-purity SiC powders.
- Applications: The fine SiC powder produced is often used in advanced ceramics, electronic components, and as a precursor for further processing in CVD or sintering.
-
Silicon-Carbon Direct Reaction Method
- Process: In this method, silicon (Si) and carbon (C) are directly reacted at high temperatures (typically above 1400°C) to form SiC. The reaction is straightforward: [ \text{Si} + \text{C} \rightarrow \text{SiC} ]
- Advantages: This method allows for precise control over the stoichiometry and purity of the SiC produced. It is particularly useful for producing high-purity SiC for electronic applications.
- Applications: The SiC produced by this method is often used in semiconductor devices, high-temperature electronics, and as a raw material for further processing.
-
Sintering
- Process: Sintered SiC is produced by compacting pure SiC powder with non-oxide sintering aids (such as boron or aluminum) and then sintering the material in an inert atmosphere at temperatures up to 2000°C or higher. The sintering aids help in densifying the material by promoting grain boundary diffusion.
- Advantages: Sintered SiC has high mechanical strength, excellent thermal conductivity, and good chemical resistance. It is also highly pure and dense, making it suitable for demanding applications.
- Applications: Sintered SiC is used in high-temperature applications, such as furnace components, heat exchangers, and wear-resistant parts.
-
Reaction Bonding
- Process: Reaction bonding involves infiltrating a porous carbon preform with molten silicon. The silicon reacts with the carbon to form SiC, which bonds the structure together. The process typically occurs at temperatures around 1400°C to 1600°C.
- Advantages: This method allows for the production of complex shapes with good mechanical properties. The resulting material has a high SiC content but may also contain residual silicon.
- Applications: Reaction-bonded SiC is used in applications requiring complex shapes and good mechanical properties, such as in aerospace components and industrial machinery.
-
Crystal Growth
- Process: SiC crystals can be grown using techniques such as the Lely method or the seeded sublimation method (also known as the modified Lely method). In the seeded sublimation method, a SiC seed crystal is placed in a high-temperature furnace, and SiC vapor is deposited onto the seed, allowing the crystal to grow.
- Advantages: This method produces high-quality single crystals of SiC, which are essential for electronic applications. The crystals have high purity and excellent electrical properties.
- Applications: SiC crystals are used in high-power and high-frequency electronic devices, such as Schottky diodes, MOSFETs, and RF devices.
-
Chemical Vapor Deposition (CVD)
- Process: CVD involves the deposition of SiC from a gas phase onto a substrate. Typically, a mixture of silicon-containing gases (such as silane, SiH₄) and carbon-containing gases (such as methane, CH₄) is used. The gases react at high temperatures (typically above 1000°C) to form SiC, which is deposited as a thin film or coating.
- Advantages: CVD produces high-purity SiC with excellent uniformity and control over thickness. The material produced by CVD is often superior in terms of mechanical and thermal properties compared to other methods.
- Applications: CVD SiC is used in high-performance applications, such as in optical components, semiconductor wafers, and protective coatings for extreme environments.
In summary, the synthesis of SiC involves a variety of methods, each tailored to produce SiC with specific properties for different applications. The choice of method depends on the desired purity, grain size, mechanical strength, and other properties required for the end-use application. Whether it is the traditional Acheson method for industrial-grade SiC or the advanced CVD method for high-purity SiC, each technique plays a crucial role in the production of this versatile material.
Summary Table:
Method | Process | Advantages | Applications |
---|---|---|---|
Acheson Method | High-temperature reaction of SiO₂ and carbon (2200°C–2500°C) | Cost-effective, large-scale production | Abrasives, refractory materials, raw material for further processing |
Low-Temperature Carbothermal | Reduction of SiO₂ with carbon (<1600°C) | Lower energy, finer particles, high purity | Advanced ceramics, electronic components, CVD/sintering precursor |
Silicon-Carbon Direct Reaction | Direct reaction of Si and C (>1400°C) | Precise stoichiometry, high purity | Semiconductors, high-temperature electronics, raw material |
Sintering | Compacting SiC powder with sintering aids (up to 2000°C) | High strength, thermal conductivity, chemical resistance | Furnace components, heat exchangers, wear-resistant parts |
Reaction Bonding | Infiltrating carbon preform with molten Si (1400°C–1600°C) | Complex shapes, good mechanical properties | Aerospace components, industrial machinery |
Crystal Growth | Growth via Lely or seeded sublimation methods | High-quality single crystals, high purity | High-power/high-frequency electronic devices (e.g., Schottky diodes, MOSFETs) |
CVD | Deposition from gas phase (SiH₄ + CH₄, >1000°C) | High purity, uniformity, superior mechanical/thermal properties | Optical components, semiconductor wafers, protective coatings |
Need help selecting the right SiC synthesis method for your application? Contact our experts today for tailored solutions!