Silicon carbide (SiC) is a versatile material with exceptional mechanical, thermal, chemical, and physical properties. It is widely used in traditional industries and high-tech fields, including semiconductors, nuclear energy, national defense, and space technology. Its applications range from industrial components like pumps and desulfurization nozzles to advanced uses in electronics and wearables. Silicon carbide ceramic materials are known for their corrosion resistance, wear resistance, and high-temperature stability, making them ideal for harsh environments. Additionally, they are used in mechanical processing, automotive, aerospace, and even biocompatible applications. The material's flexibility and durability ensure its relevance across diverse industries.
Key Points Explained:
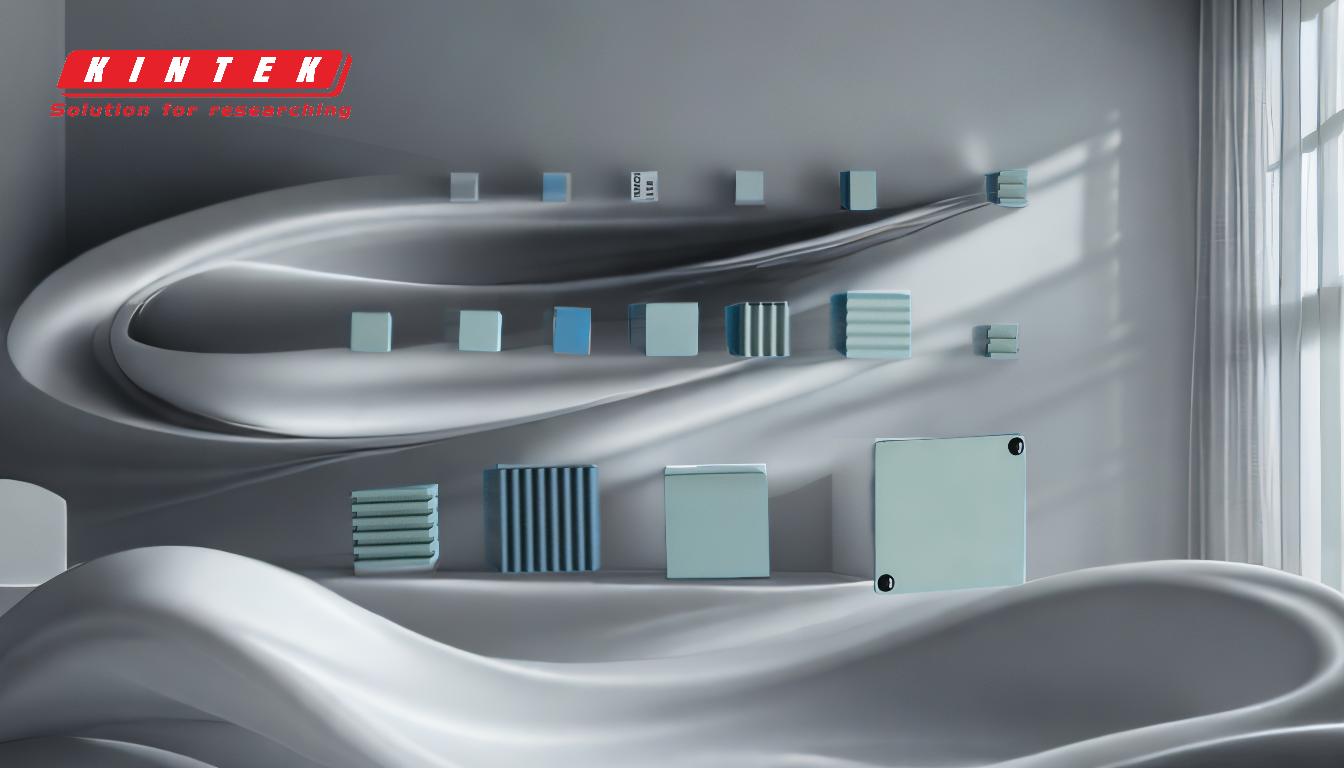
-
Mechanical and Industrial Applications:
- Silicon carbide is extensively used in mechanical and industrial applications due to its hardness and wear resistance. It is commonly employed in:
- Cutting Tools and Sandpapers: Historically, silicon carbide has been used for abrasive purposes, such as sandpapers and cutting tools, owing to its extreme hardness.
- Pumps: Silicon carbide ceramic materials are used in pumps for their corrosion resistance, wear resistance, and non-toxicity. These properties make them suitable for environments with corrosive media, ensuring maintenance-free operation for 5 to 8 years.
- Desulfurization Nozzles: In corrosive environments, such as thermal power plants and large boilers, silicon carbide is used to make desulfurization nozzles. Its chemical and physical stability makes it ideal for handling highly corrosive gases and liquids.
- Silicon carbide is extensively used in mechanical and industrial applications due to its hardness and wear resistance. It is commonly employed in:
-
High-Tech and Advanced Applications:
- Silicon carbide's unique properties make it indispensable in high-tech industries:
- Semiconductors: SiC is a key material in the semiconductor industry due to its high thermal conductivity and ability to operate at high temperatures and voltages.
- Nuclear Energy: Its radiation resistance and thermal stability make silicon carbide suitable for nuclear energy applications.
- National Defense and Space Technology: Silicon carbide is used in defense and space applications for its lightweight, high-strength, and thermal shock resistance properties.
- Silicon carbide's unique properties make it indispensable in high-tech industries:
-
Thermal and Chemical Stability:
- Silicon carbide ceramic tubing is highly valued for its thermal and chemical stability. It features:
- High density and hardness.
- Resistance to wear, abrasion, and corrosion.
- Excellent flexural strength at various temperatures.
- Shock resistance and flexibility in high-temperature environments.
- These properties make it suitable for industries such as power generation, chemical processing, oil drilling, automotive, and semiconductor manufacturing.
- Silicon carbide ceramic tubing is highly valued for its thermal and chemical stability. It features:
-
Types of Silicon Carbide Ceramics:
- The main types of silicon carbide ceramic materials used in industrial production include:
- Reaction Sintering: Known for its high density and strength.
- Atmospheric Pressure Sintering: Offers excellent mechanical properties and is cost-effective.
- Recrystallization Sintering: Provides superior thermal shock resistance.
- Each type has unique advantages, and the choice depends on the specific application requirements.
- The main types of silicon carbide ceramic materials used in industrial production include:
-
Ceramic Industry Applications:
- In the ceramic industry, silicon carbide is used for:
- Receiving Capsules and Muffles: These components are utilized in the sintering of technical ceramics and porcelain, benefiting from silicon carbide's high-temperature stability and durability.
- In the ceramic industry, silicon carbide is used for:
-
Biocompatibility and Wearables:
- Silicon carbide ceramics are also used in biocompatible applications and wearables due to their chemical stability and non-toxicity. This makes them suitable for medical devices and wearable technology.
In summary, silicon carbide ceramic materials are highly versatile and indispensable across a wide range of industries. Their exceptional properties, including hardness, thermal stability, and corrosion resistance, ensure their continued relevance in both traditional and cutting-edge applications. For more detailed information on silicon carbide ceramics, visit silicon carbide ceramic.
Summary Table:
Application | Key Properties | Industries |
---|---|---|
Cutting Tools & Sandpapers | Extreme hardness, wear resistance | Industrial, Manufacturing |
Pumps | Corrosion resistance, wear resistance, non-toxicity | Chemical Processing, Oil & Gas |
Desulfurization Nozzles | Chemical stability, thermal resistance | Power Generation, Environmental Protection |
Semiconductors | High thermal conductivity, high-temperature operation | Electronics, Renewable Energy |
Nuclear Energy | Radiation resistance, thermal stability | Energy, Defense |
Aerospace & Defense | Lightweight, high strength, thermal shock resistance | Space Technology, National Defense |
Biocompatible Applications | Chemical stability, non-toxicity | Medical Devices, Wearable Technology |
Ceramic Industry | High-temperature stability, durability | Technical Ceramics, Porcelain Manufacturing |
Interested in learning how silicon carbide can benefit your industry? Contact us today for expert advice!