Injection moulding machines are versatile tools used to manufacture a wide range of plastic products. These machines melt plastic pellets and inject the molten material into a mould, where it cools and solidifies into the desired shape. The process is highly efficient, repeatable, and cost-effective for mass production. Common items produced using injection moulding include plastic bottles, bottle caps, toys like Legos, consumer electronics, kitchenware, plastic furniture, flower pots, and even toilet seats. The process is ideal for creating complex shapes with high precision, making it a cornerstone of modern manufacturing.
Key Points Explained:
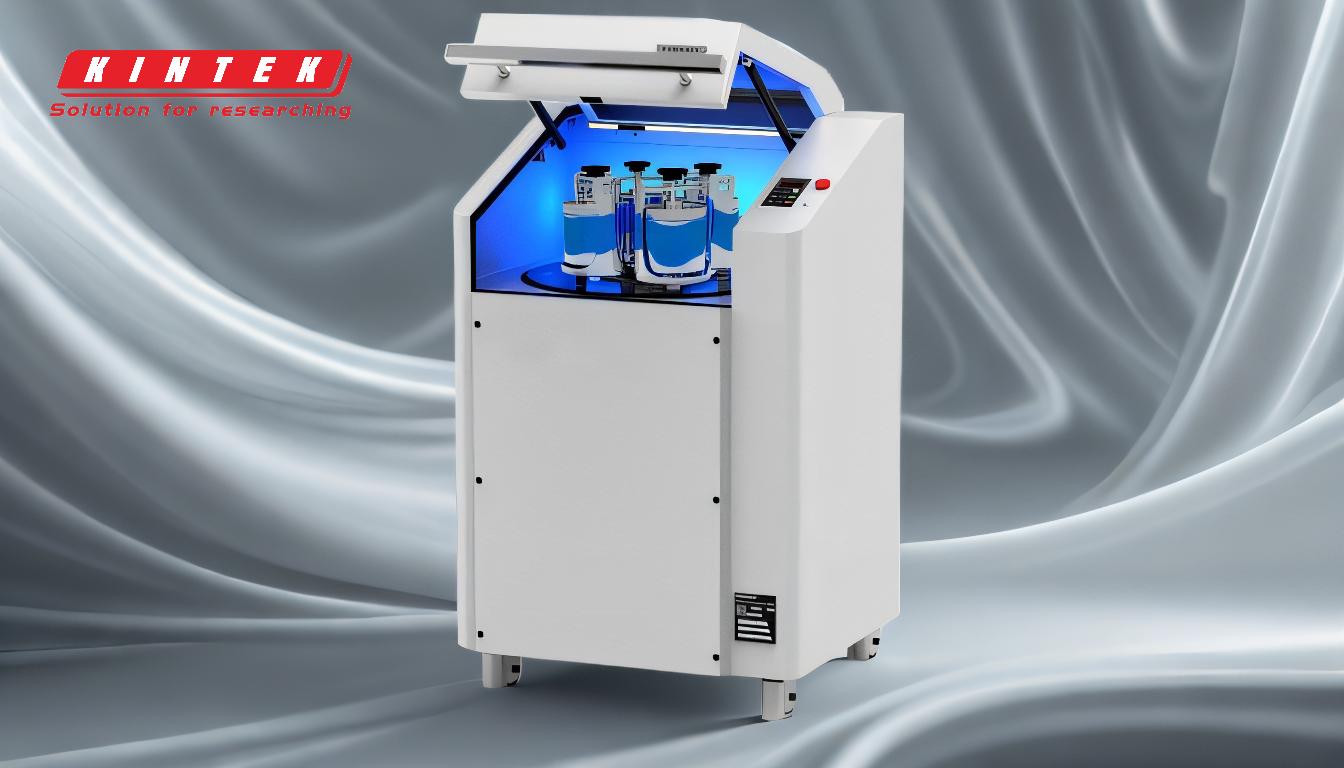
-
Plastic Bottles
- Injection moulding is widely used to produce plastic bottles for beverages, cleaning products, and personal care items.
- The process allows for consistent wall thickness, durability, and the ability to incorporate intricate designs or logos.
- Materials like PET (polyethylene terephthalate) are commonly used for their clarity and recyclability.
-
Bottle Caps
- Bottle caps are a prime example of small, precision parts made using injection moulding.
- The process ensures tight tolerances and compatibility with the bottles they seal.
- Materials like polypropylene are often used for their flexibility and resistance to chemicals.
-
Legos and Toys
- Injection moulding is ideal for producing toys like Legos due to its ability to create highly detailed and consistent parts.
- The process ensures that each piece fits perfectly with others, which is critical for toys that require assembly.
- Durable plastics like ABS (acrylonitrile butadiene styrene) are commonly used for their strength and safety.
-
Computers and Other Consumer Electronics
- Many components of computers, smartphones, and other electronics are made using injection moulding.
- This includes casings, buttons, and internal parts that require precision and durability.
- Materials like polycarbonate are often used for their strength, heat resistance, and electrical insulation properties.
-
Kitchenware
- Injection moulding is used to produce a variety of kitchen items, such as utensils, storage containers, and cutting boards.
- The process allows for the creation of ergonomic designs and the use of food-safe plastics.
- Materials like polypropylene and polyethylene are commonly used for their durability and resistance to heat and chemicals.
-
Plastic Furniture
- Injection moulding is used to create lightweight, durable, and aesthetically pleasing plastic furniture.
- Items like chairs, tables, and storage units can be produced with intricate designs and textures.
- Materials like HDPE (high-density polyethylene) are often used for their strength and resistance to weathering.
-
Flower Pots
- Injection moulding is ideal for producing flower pots of various sizes and designs.
- The process allows for the creation of drainage holes and textured surfaces to enhance functionality and aesthetics.
- Materials like polypropylene are commonly used for their durability and resistance to UV light.
-
Toilet Seats
- Injection moulding is used to produce toilet seats that are durable, easy to clean, and resistant to wear.
- The process allows for the incorporation of features like soft-close hinges and antimicrobial coatings.
- Materials like thermoplastics are commonly used for their strength and resistance to moisture.
In summary, injection moulding machines are essential for producing a vast array of plastic products that are integral to everyday life. The process offers unparalleled precision, efficiency, and versatility, making it a cornerstone of modern manufacturing. Whether it's a simple bottle cap or a complex electronic component, injection moulding ensures high-quality, consistent, and cost-effective production.
Summary Table:
Product | Key Features | Common Materials |
---|---|---|
Plastic Bottles | Consistent wall thickness, durability, intricate designs | PET |
Bottle Caps | Tight tolerances, compatibility, chemical resistance | Polypropylene |
Legos and Toys | Highly detailed, consistent parts, perfect fit for assembly | ABS |
Consumer Electronics | Precision, durability, heat resistance, electrical insulation | Polycarbonate |
Kitchenware | Ergonomic designs, food-safe, heat and chemical resistance | Polypropylene, Polyethylene |
Plastic Furniture | Lightweight, durable, intricate designs, weather resistance | HDPE |
Flower Pots | Drainage holes, textured surfaces, UV resistance | Polypropylene |
Toilet Seats | Durability, easy to clean, moisture resistance, soft-close hinges | Thermoplastics |
Ready to enhance your manufacturing process? tablet press molds can help streamline your production. Contact us today to learn how injection moulding can benefit your business!