Catalytic pyrolysis is a process that uses catalysts to enhance the breakdown of biomass or plastics into valuable products such as biofuels, chemicals, and hydrocarbons. The choice of catalyst depends on the feedstock, desired end products, and process conditions. Commonly used catalysts include biochar-based catalysts, zeolites, clay minerals like kaolin, and metal-based catalysts such as titanium compounds and metal nitrides. These catalysts improve reaction efficiency, selectivity, and yield by promoting specific chemical reactions, such as cracking heavy hydrocarbons or deoxygenation. The catalytic activity is influenced by factors like the catalyst's basicity, porosity, and composition, which determine its ability to optimize the pyrolysis process.
Key Points Explained:
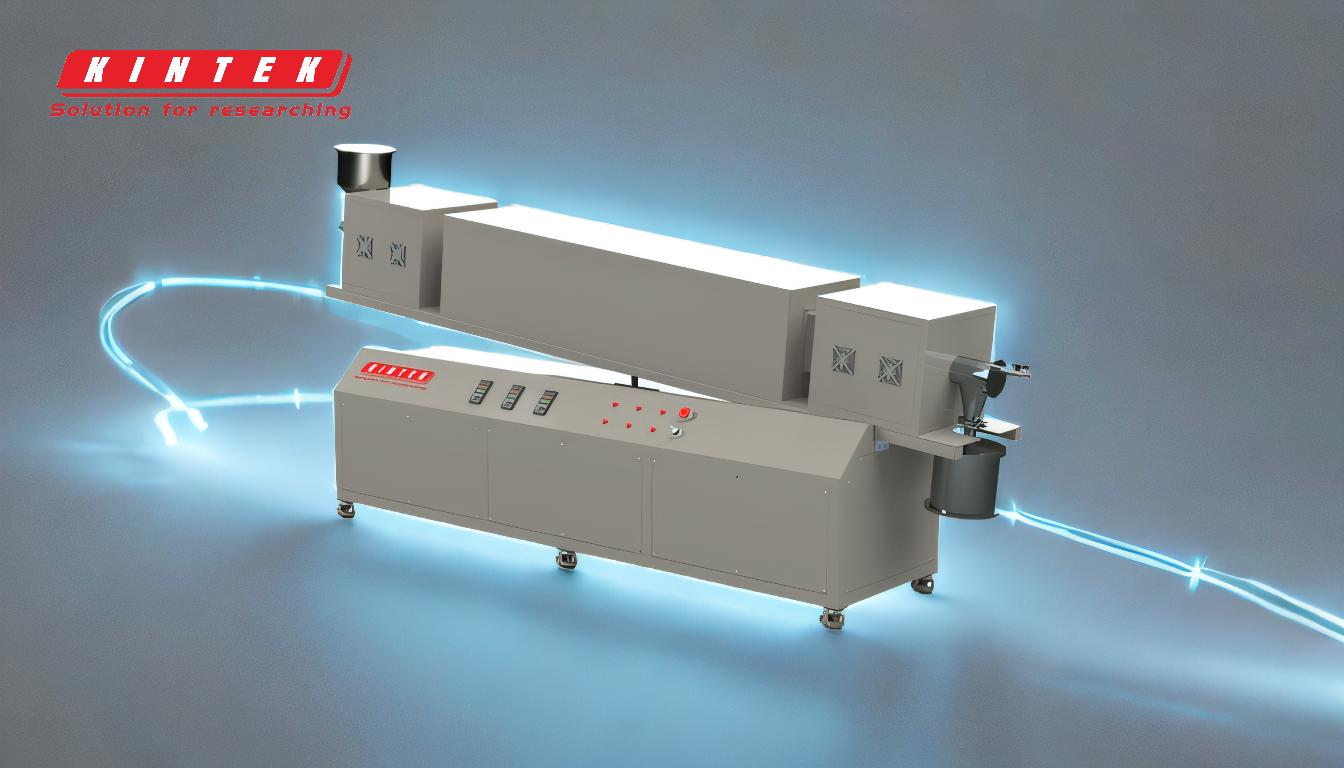
-
Role of Catalysts in Pyrolysis
- Catalysts are used to promote specific chemical reactions during pyrolysis, enhancing the conversion of biomass or plastics into valuable products like biofuels and chemicals.
- They improve reaction selectivity, efficiency, and yield by targeting desirable reactions, such as cracking heavy hydrocarbons or deoxygenation.
-
Types of Catalysts Used in Catalytic Pyrolysis
- Biochar-Based Catalysts: Derived from biomass, these catalysts are effective in promoting reactions that yield biofuels and chemicals. They are sustainable and cost-effective.
- Zeolites: Porous materials composed of aluminum and silicon oxides, zeolites are widely used for their ability to selectively crack heavy hydrocarbons and condense light hydrocarbons. They are particularly effective for producing C1, C2, and C3 hydrocarbons from biomass.
- Clay Minerals (e.g., Kaolin): These natural minerals are used for their catalytic properties in cracking and reforming reactions. They are cost-effective and widely available.
-
Metal-Based Catalysts:
- Titanium Compounds (e.g., TiN): Used in fast pyrolysis for furfural production, these catalysts enhance the yield of furfural compounds.
- Metal Nitrides (e.g., GaN): Known for their high activity and selectivity in producing furfural and other valuable chemicals.
-
Influence of Catalyst Properties
- Basicity: Catalysts with higher basicity exhibit greater efficiency due to their strong deoxygenation capacity, which is crucial for improving the quality of pyrolysis products.
- Porosity and Surface Area: Zeolites and other porous catalysts provide a large surface area for reactions, enhancing their effectiveness in cracking and reforming processes.
- Composition: The chemical composition of the catalyst determines its reactivity and selectivity. For example, the presence of alkali and alkali-earth metals in biomass can exhibit inherent catalytic activity.
-
Application-Specific Catalysts
- Plastic Pyrolysis: Catalysts are used to convert plastic waste into oil by promoting specific chemical reactions. The choice of catalyst depends on the type of plastic and desired end products.
- Biomass Pyrolysis: Catalysts like zeolites and clay minerals are used to optimize the production of hydrocarbons and biofuels from biomass. Metal-based catalysts are employed for specialized applications, such as furfural production.
-
Catalyst Selection Criteria
- The choice of catalyst depends on factors such as:
- Feedstock Type: Different feedstocks (e.g., biomass, plastics) require specific catalysts to achieve optimal results.
- Desired End Products: Catalysts are selected based on the target products, such as biofuels, chemicals, or hydrocarbons.
- Process Conditions: Temperature, pressure, and reaction time influence the choice of catalyst.
- The choice of catalyst depends on factors such as:
-
Challenges and Considerations
- Catalyst Deactivation: Over time, catalysts may lose activity due to fouling, poisoning, or sintering, requiring regeneration or replacement.
- Cost and Availability: The economic feasibility of catalysts depends on their cost, availability, and reusability.
- Environmental Impact: Sustainable catalysts, such as biochar-based catalysts, are preferred for their lower environmental footprint.
By carefully selecting and optimizing catalysts, catalytic pyrolysis can be tailored to produce high-value products efficiently and sustainably.
Summary Table:
Catalyst Type | Key Features | Applications |
---|---|---|
Biochar-Based | Sustainable, cost-effective, promotes biofuels and chemicals | Biomass pyrolysis, biofuel production |
Zeolites | Porous, selective cracking, condenses light hydrocarbons | C1, C2, C3 hydrocarbon production from biomass |
Clay Minerals (e.g., Kaolin) | Cost-effective, widely available, effective in cracking and reforming | Biomass and plastic pyrolysis |
Metal-Based (e.g., TiN, GaN) | High activity, selective furfural production, enhances chemical yields | Fast pyrolysis, furfural and chemical production |
Ready to optimize your pyrolysis process? Contact our experts today for tailored catalyst solutions!