Calendering is a critical finishing process in textile manufacturing that enhances the fabric's appearance, texture, and functionality. By passing fabric through heated rollers under high pressure, calendering smooths the surface, adds a polished or glossy finish, and can even create unique patterns like the watered effect on moire fabrics. This process is also used to thin materials or combine fabrics with other materials, such as rubber, for specialized applications. Calendering improves the fabric's hand feel, durability, and aesthetic appeal, making it suitable for a wide range of textile products.
Key Points Explained:
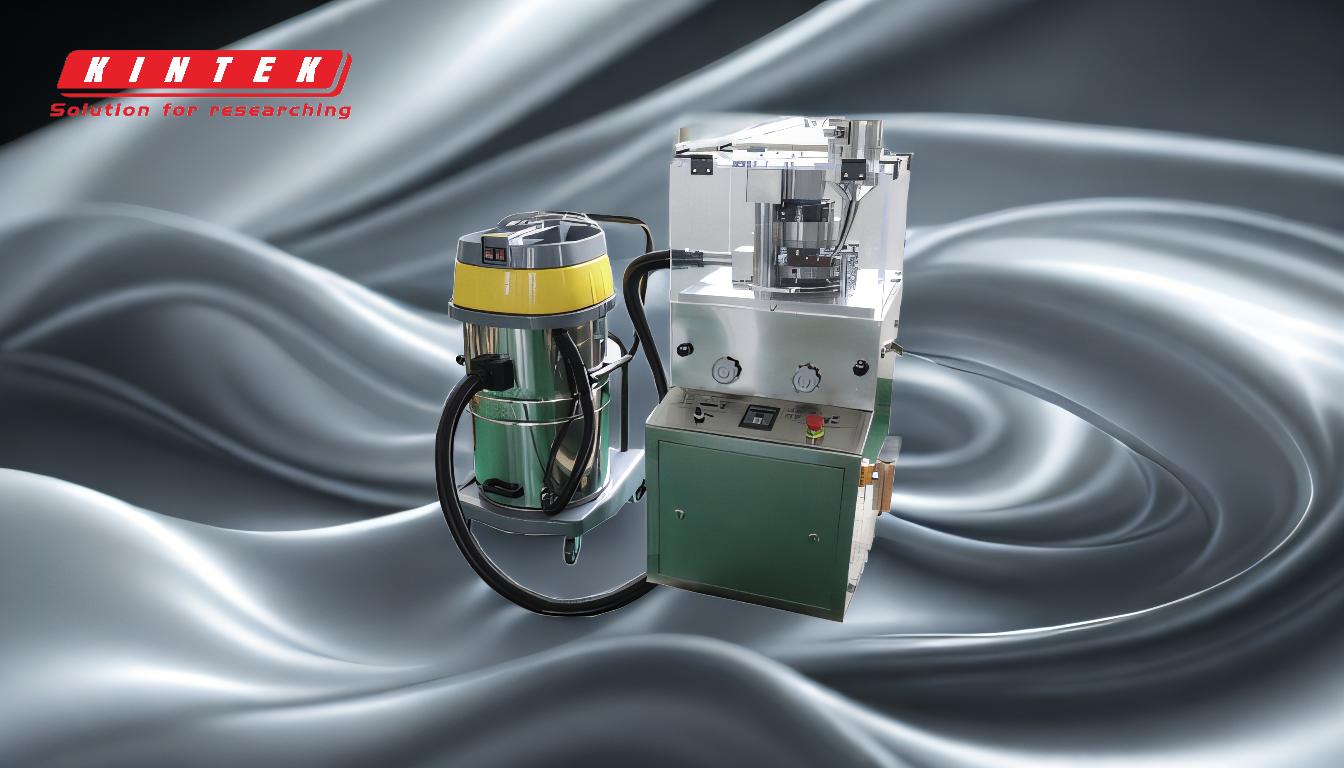
-
Definition and Purpose of Calendering:
- Calendering is a mechanical finishing process that involves passing fabric through a series of heated rollers under high pressure.
- The primary purpose is to alter the fabric's surface characteristics, such as smoothness, sheen, and texture, while also improving its functional properties.
-
How Calendering Works:
- The fabric is fed through calender rollers, which are typically heated to specific temperatures.
- The pressure applied by the rollers compresses the fabric, flattening its surface and creating a uniform finish.
- The combination of heat and pressure can also bond fabrics with other materials, such as rubber, in processes like frictioning or combining.
-
Types of Effects Achieved Through Calendering:
- Smoothing: Calendering removes surface irregularities, giving the fabric a sleek and polished appearance.
- Glossing: The process can impart a shiny or lustrous finish, enhancing the fabric's visual appeal.
- Thinning: By compressing the fabric, calendering can reduce its thickness, making it lighter and more pliable.
- Pattern Creation: Specialized rollers can create unique patterns, such as the watered effect seen in moire fabrics.
-
Applications of Calendering in Textiles:
- Moire Fabrics: Calendering produces the distinctive watered effect by pressing the fabric with engraved rollers.
- Cambric and Sateens: These fabrics are calendered to achieve a smooth, polished surface and improved drape.
- Rubber-Coated Fabrics: Calendering is used to combine rubber sheeting with textiles, enhancing durability and functionality for applications like waterproofing or industrial uses.
-
Benefits of Calendering:
- Enhanced Aesthetics: The process improves the fabric's visual appeal by creating a smooth, glossy, or patterned surface.
- Improved Hand Feel: Calendering makes fabrics softer and more pleasant to touch.
- Increased Durability: The compression and bonding processes can strengthen the fabric, making it more resistant to wear and tear.
- Versatility: Calendering can be tailored to achieve a wide range of finishes and effects, making it suitable for diverse textile applications.
-
Considerations for Fabric Purchasers:
- Desired Finish: Purchasers should consider whether they need a smooth, glossy, or patterned finish for their specific application.
- Material Compatibility: Not all fabrics respond equally to calendering, so it's essential to choose materials that will benefit from the process.
- Functional Requirements: For applications requiring durability or specialized properties (e.g., waterproofing), calendered fabrics with rubber coatings may be ideal.
- Cost and Efficiency: Calendering adds value to fabrics but may increase production costs, so purchasers should weigh the benefits against their budget.
By understanding the calendering process and its effects, fabric purchasers can make informed decisions to select materials that meet their aesthetic, functional, and budgetary needs.
Summary Table:
Aspect | Details |
---|---|
Definition | A mechanical finishing process using heated rollers under high pressure. |
Purpose | Alters surface characteristics (smoothness, sheen, texture) and functionality. |
Key Effects | Smoothing, glossing, thinning, and pattern creation (e.g., moire fabrics). |
Applications | Moire fabrics, cambric, sateens, rubber-coated textiles. |
Benefits | Enhanced aesthetics, improved hand feel, increased durability, versatility. |
Considerations | Desired finish, material compatibility, functional requirements, cost. |
Ready to elevate your fabric quality? Contact us today to learn more about calendering solutions!