Sintering zirconia refers to the process of heating zirconia materials to high temperatures (typically between 1,100°C to 1,200°C) to fuse particles together, reducing porosity and increasing density. This transformation results in a stronger, more durable material with enhanced mechanical properties. During sintering, zirconia undergoes significant shrinkage and a structural change from a monoclinic to a polytetragonal crystalline state, which improves its hardness, strength, and translucency. Specialized high-temperature sintering furnaces are required for this process, as standard porcelain furnaces are insufficient. Sintering is a critical step in producing high-quality zirconia ceramic restorations used in dental and industrial applications.
Key Points Explained:
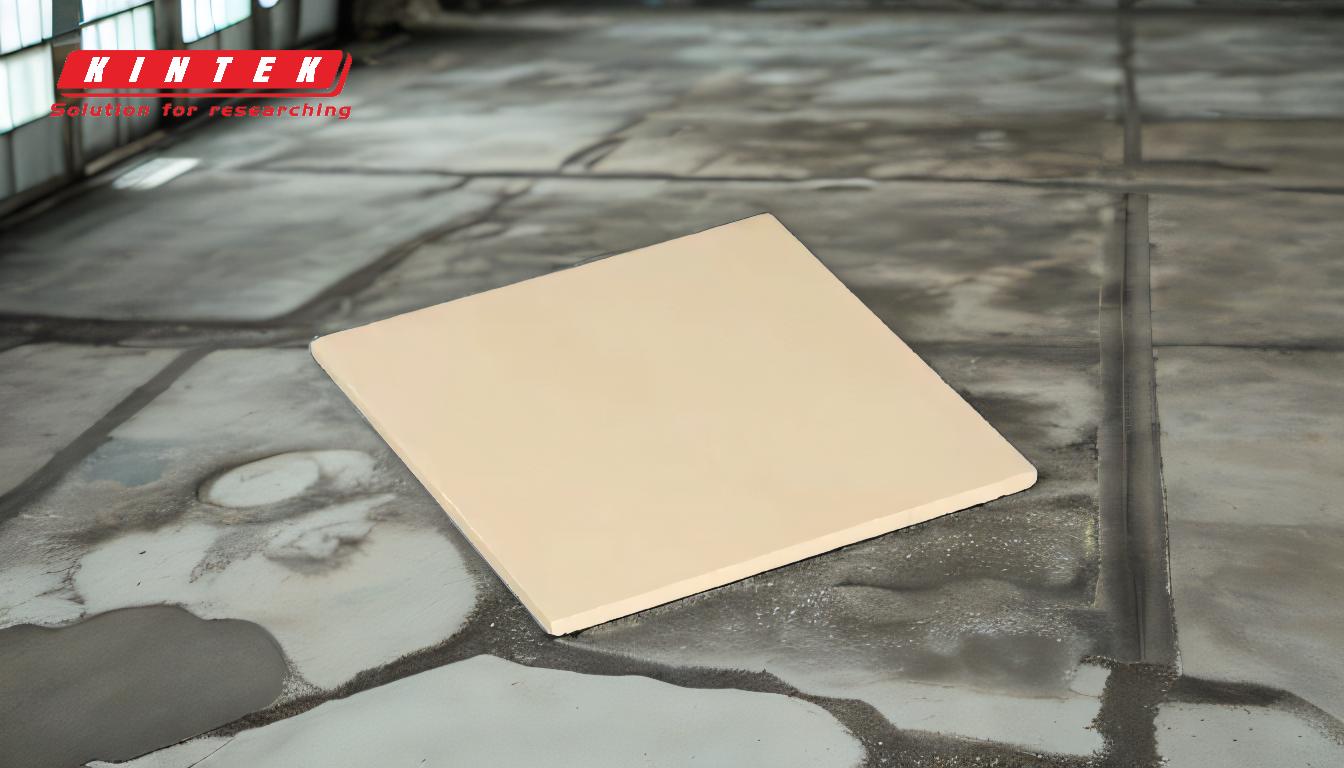
-
Definition of Sintering in Zirconia:
- Sintering is a thermal process used to fuse zirconia particles into a solid mass without melting them into a liquid state. This process is essential for enhancing the material's mechanical properties, such as strength and durability.
- Unlike other processes that involve melting, sintering relies on heat and sometimes pressure to bond particles at a molecular level.
-
Temperature and Structural Transformation:
- Zirconia sintering occurs at high temperatures, typically between 1,100°C to 1,200°C.
- At these temperatures, zirconia undergoes a crystalline phase transformation from a monoclinic structure to a polytetragonal structure. This transformation is critical for achieving the material's high strength and hardness.
-
Shrinkage and Density Improvement:
- During sintering, zirconia experiences significant shrinkage, which reduces porosity and increases the material's density.
- The reduction in porosity enhances the material's mechanical properties, making it more suitable for applications requiring high strength and durability, such as dental restorations.
-
Enhanced Mechanical Properties:
- Sintering improves zirconia's mechanical properties, including strength, hardness, and translucency.
- These enhancements make sintered zirconia ideal for use in dental crowns, bridges, and other ceramic restorations, as well as in industrial applications where durability is critical.
-
Specialized Equipment Requirements:
- Sintering zirconia requires specialized high-temperature sintering furnaces, which are different from standard porcelain furnaces.
- These furnaces are designed to reach and maintain the precise temperatures needed for the sintering process, ensuring consistent and high-quality results.
-
Applications of Sintered Zirconia:
- Sintered zirconia is widely used in dental applications due to its biocompatibility, strength, and aesthetic properties.
- It is also used in industrial applications, such as cutting tools and wear-resistant components, where its hardness and durability are advantageous.
By understanding the sintering process and its effects on zirconia, purchasers and users can better appreciate the material's capabilities and ensure they select the appropriate equipment and consumables for their specific needs.
Summary Table:
Key Aspect | Details |
---|---|
Temperature Range | 1,100°C to 1,200°C |
Structural Transformation | Monoclinic to polytetragonal crystalline state |
Shrinkage & Density | Reduces porosity, increases density, and improves mechanical properties |
Enhanced Properties | Strength, hardness, and translucency |
Equipment Needed | Specialized high-temperature sintering furnaces |
Applications | Dental restorations, cutting tools, wear-resistant components |
Ready to enhance your zirconia sintering process? Contact us today for expert advice and solutions!