In Physical Vapor Deposition (PVD), a variety of gases are used depending on the specific process and desired coating properties. These gases can be broadly categorized into inert gases and reactive gases. Inert gases like argon are primarily used in sputtering processes to facilitate the ejection of target material atoms. Reactive gases such as oxygen, nitrogen, methane, and acetylene are used to chemically react with the ejected material, forming compounds like oxides, nitrides, and carbides. The choice of gas depends on factors like the atomic weight of the target material and the desired chemical composition of the coating.
Key Points Explained:
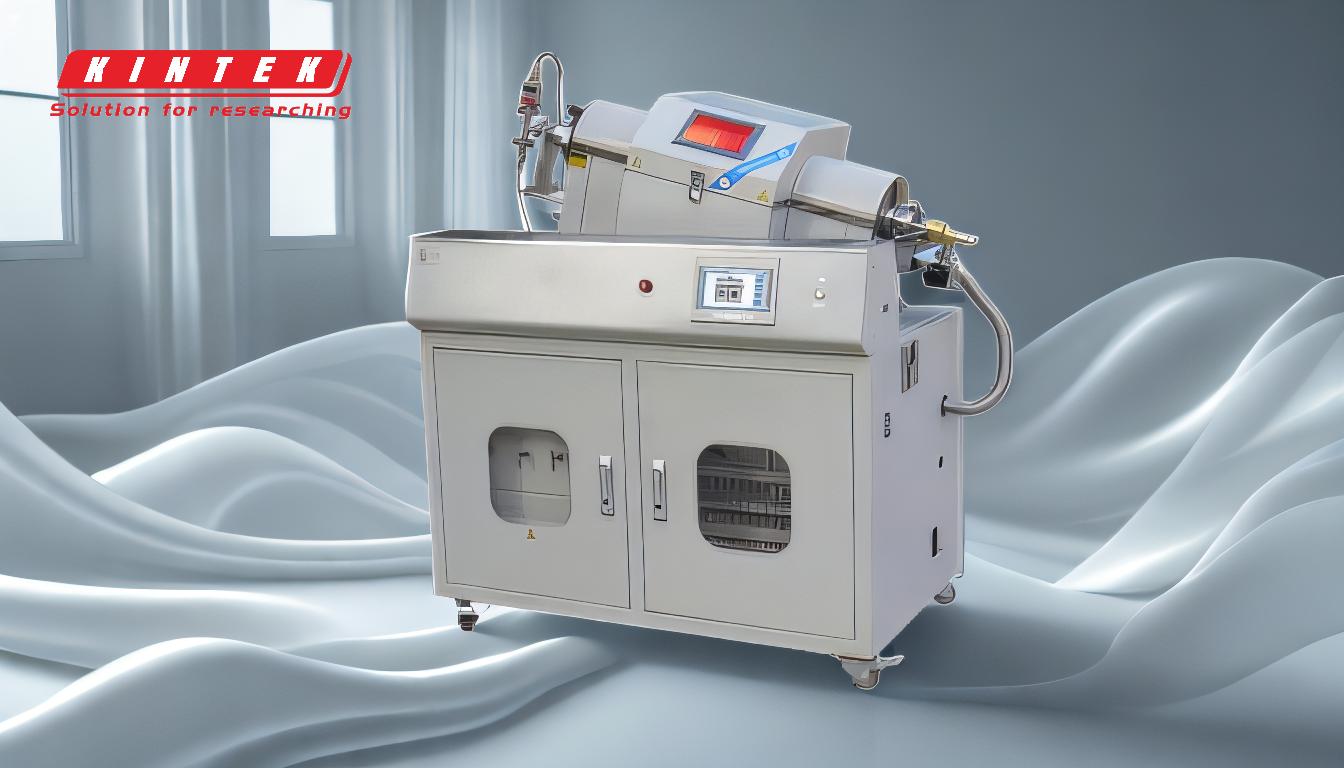
-
Inert Gases in PVD:
- Argon (Ar): The most commonly used inert gas in PVD, particularly in sputtering processes. Argon is chosen because it is chemically inert, meaning it does not react with the target material. Its atomic weight is close to that of many target materials, making it efficient for momentum transfer during sputtering.
- Neon (Ne): Used for sputtering light elements due to its low atomic weight, which matches well with lighter target materials.
- Krypton (Kr) and Xenon (Xe): These heavier inert gases are used for sputtering heavy elements. Their higher atomic weights make them more effective in transferring momentum to heavier target materials.
-
Reactive Gases in PVD:
- Oxygen (O2): Used to form metal oxide coatings. When oxygen reacts with metal atoms ejected from the target, it forms compounds like titanium oxide (TiO2) or aluminum oxide (Al2O3), which are commonly used for their hardness and optical properties.
- Nitrogen (N2): Reacts with metal atoms to form metal nitrides, such as titanium nitride (TiN) or aluminum nitride (AlN). These coatings are known for their wear resistance and are often used in cutting tools and decorative coatings.
- Methane (CH4) and Acetylene (C2H2): These gases are used to form metal carbides, such as titanium carbide (TiC) or tungsten carbide (WC). Carbide coatings are valued for their hardness and resistance to wear and corrosion.
- Hydrogen (H2): Sometimes used in combination with other gases to modify the properties of the coating, such as reducing oxides or altering the microstructure of the deposited film.
-
Process Gas Input System:
- The gases are supplied from gas cylinders and are controlled through a series of valves and meters before entering the vacuum chamber. This ensures precise control over the gas flow rates and composition, which is critical for achieving the desired coating properties.
- The system must be carefully calibrated to maintain the correct gas mixture and pressure within the chamber, as these parameters directly affect the quality and consistency of the PVD coating.
-
Reactive Sputtering:
- In reactive sputtering, reactive gases like nitrogen or acetylene are introduced into the sputtering process. These gases chemically react with the ejected target material atoms, forming compound coatings directly on the substrate.
- This process allows for the deposition of a wide range of materials, including oxides, nitrides, and carbides, with precise control over the chemical composition and properties of the coating.
-
Applications of Different Gases:
- Argon: Used in non-reactive sputtering processes where the goal is to deposit pure metal films without chemical modification.
- Oxygen: Used to create transparent, hard, and wear-resistant oxide coatings, often used in optical and protective applications.
- Nitrogen: Commonly used in the production of hard, wear-resistant nitride coatings for tools and machinery.
- Methane/Acetylene: Used to produce carbide coatings, which are extremely hard and resistant to wear, making them suitable for cutting tools and high-stress applications.
-
Considerations for Gas Selection:
- Atomic Weight Matching: The atomic weight of the sputtering gas should be close to that of the target material to ensure efficient momentum transfer. This is why argon is commonly used for many metals, while neon, krypton, or xenon are used for lighter or heavier elements, respectively.
- Reactivity: The choice of reactive gas depends on the desired chemical composition of the coating. For example, oxygen is used for oxide coatings, nitrogen for nitride coatings, and methane or acetylene for carbide coatings.
- Process Control: The gas flow rates, pressure, and mixture must be carefully controlled to achieve the desired coating properties. This requires precise instrumentation and monitoring throughout the PVD process.
In summary, the gases used in PVD are selected based on their role in the deposition process, whether as inert gases for sputtering or reactive gases for forming compound coatings. The choice of gas, along with precise control over the process parameters, is crucial for achieving the desired coating properties in PVD applications.
Summary Table:
Gas Type | Examples | Role in PVD | Applications |
---|---|---|---|
Inert Gases | Argon (Ar), Neon (Ne) | Facilitate sputtering by ejecting target material atoms without chemical reaction | Non-reactive sputtering for pure metal films |
Reactive Gases | Oxygen (O2), Nitrogen (N2) | Chemically react with target material to form oxides, nitrides, or carbides | Hard, wear-resistant coatings for tools, optics, and decorative applications |
Reactive Gases | Methane (CH4), Acetylene (C2H2) | Form metal carbides for extreme hardness and wear resistance | Cutting tools and high-stress applications |
Reactive Gases | Hydrogen (H2) | Modifies coating properties by reducing oxides or altering microstructure | Specialized applications requiring precise coating modifications |
Need help selecting the right gases for your PVD process? Contact our experts today for tailored solutions!