A rotary kiln is a cylindrical, inclined furnace that rotates to uniformly heat and process solid materials at high temperatures. It is used for various industrial processes such as calcination, thermal desorption, organic combustion, and sintering. Raw materials are fed into the upper end of the kiln and move downward due to the kiln's rotation and slight slope. As the materials travel through the kiln, they are exposed to hot gases, either co-current or counter-current, generated by an external furnace or internal flame. The high temperatures and controlled retention times facilitate chemical reactions or physical changes in the materials, making rotary kilns essential for industries like cement production, waste treatment, and metal processing.
Key Points Explained:
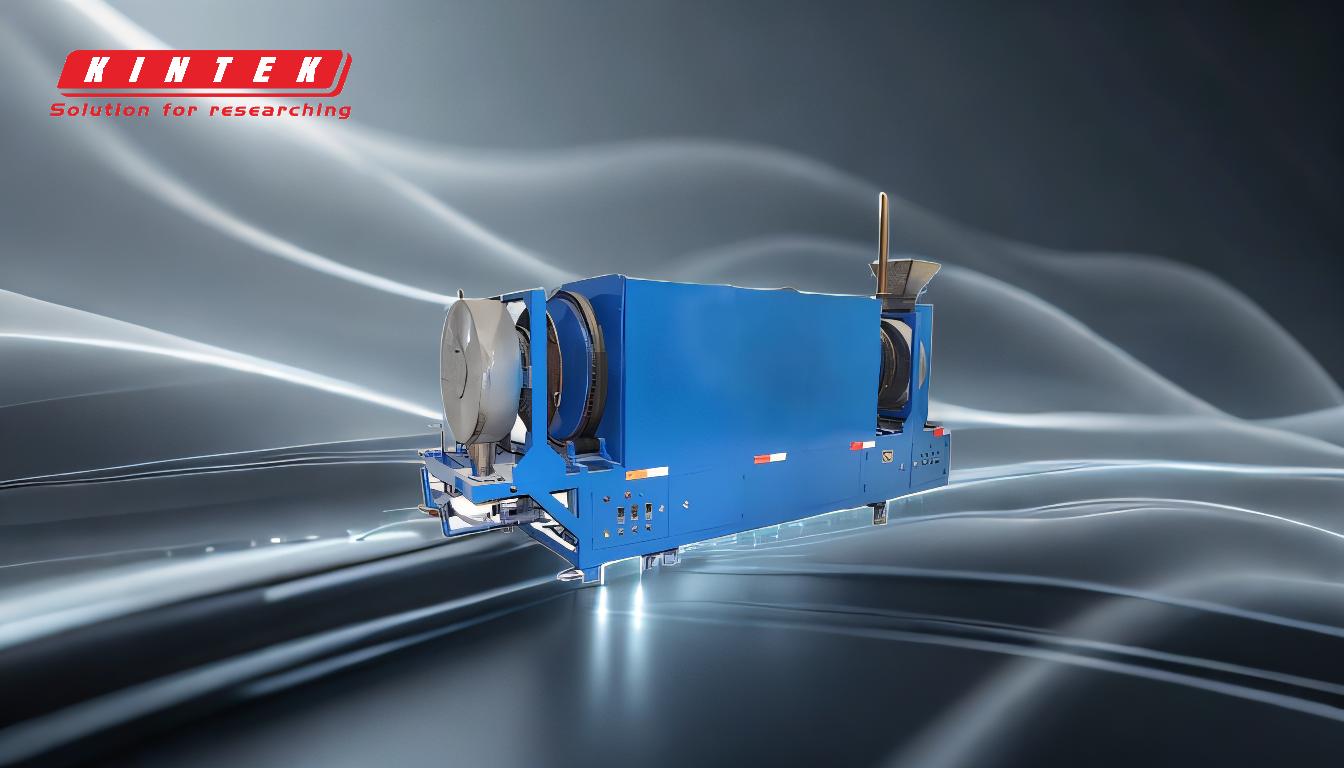
-
Structure and Operation of a Rotary Kiln:
- A rotary kiln is a cylindrical vessel, slightly inclined from the horizontal, that rotates slowly about its longitudinal axis.
- The rotation ensures uniform heating and mixing of the materials as they move from the upper (feed) end to the lower (discharge) end.
- The slight slope facilitates the movement of materials through the kiln by gravity.
-
Heating Mechanism:
- Hot gases flow through the kiln, either in the same direction as the material (co-current) or in the opposite direction (counter-current).
- These gases are generated either by an external furnace or by a flame inside the kiln, projected from a burner-pipe.
- Common fuels include gas, oil, pulverized petroleum coke, or pulverized coal.
-
Temperature and Retention Time:
- Rotary kilns operate at high temperatures, typically ranging from 800 to 2,200°F, depending on the process.
- The material is held at a specified temperature for a precise amount of time to ensure the desired chemical reaction or physical change occurs.
- Temperature profiles are determined through chemical and thermal analyses to optimize the process.
-
Common Processes in a Rotary Kiln:
- Calcination: Heating materials to high temperatures to decompose or remove volatile components, often used in cement and lime production.
- Thermal Desorption: Removing contaminants from materials by heating, commonly used in soil remediation.
- Organic Combustion: Burning organic materials to produce energy or reduce waste volume.
- Sintering/Induration: Heating materials to form a solid mass without melting, often used in metal ore processing.
- Heat Setting: Applying heat to set or cure materials, such as in the production of ceramics.
-
Material Movement and Mixing:
- The rotation of the kiln ensures that the materials are continuously stirred and mixed, promoting uniform heating and reaction.
- This movement also prevents the materials from clumping or sticking to the kiln walls.
-
Applications of Rotary Kilns:
- Cement Production: Rotary kilns are essential for producing clinker, the main component of cement.
- Waste Treatment: Used for incinerating hazardous waste and reducing its volume.
- Metal Processing: Employed in the extraction and refining of metals, such as iron and aluminum.
- Chemical Industry: Used for processes like calcination of limestone and production of titanium dioxide.
-
Advantages of Rotary Kilns:
- Continuous Processing: Rotary kilns allow for continuous feeding and discharge of materials, making them efficient for large-scale industrial processes.
- Uniform Heating: The rotation and mixing ensure that all materials are exposed to the same temperature, leading to consistent product quality.
- Versatility: Rotary kilns can handle a wide range of materials and processes, making them adaptable to various industries.
-
Challenges and Considerations:
- High Energy Consumption: Operating at high temperatures requires significant energy input, which can be costly.
- Maintenance: The rotating mechanism and high temperatures can lead to wear and tear, requiring regular maintenance.
- Emissions Control: The combustion process can produce emissions, necessitating effective pollution control measures.
In summary, a rotary kiln is a versatile and efficient industrial furnace used for high-temperature processing of solid materials. Its design and operation facilitate uniform heating, mixing, and controlled chemical reactions, making it indispensable in industries such as cement production, waste treatment, and metal processing. Understanding the key aspects of rotary kilns can help purchasers make informed decisions when selecting equipment for specific industrial applications.
Summary Table:
Aspect | Details |
---|---|
Structure | Cylindrical, inclined vessel rotating about its longitudinal axis. |
Heating Mechanism | Co-current or counter-current hot gases from external furnace or internal flame. |
Temperature Range | 800 to 2,200°F, depending on the process. |
Common Processes | Calcination, thermal desorption, organic combustion, sintering, heat setting. |
Applications | Cement production, waste treatment, metal processing, chemical industry. |
Advantages | Continuous processing, uniform heating, versatility. |
Challenges | High energy consumption, maintenance, emissions control. |
Discover how a rotary kiln can optimize your industrial processes—contact us today for expert advice!