A ball mill is a versatile piece of equipment widely used in the ceramics industry for grinding, mixing, and reducing the particle size of materials. It plays a crucial role in preparing raw materials like feldspar, pigments, and other ceramic components by ensuring uniformity and fine particle size distribution. Ball mills can operate in both wet and dry systems, making them suitable for various ceramic processes. They are employed in batch or continuous operations and are scalable for small laboratory settings or large industrial applications. Additionally, planetary ball mills are used for more demanding tasks, such as mechanical alloying, which is essential for advanced ceramic production.
Key Points Explained:
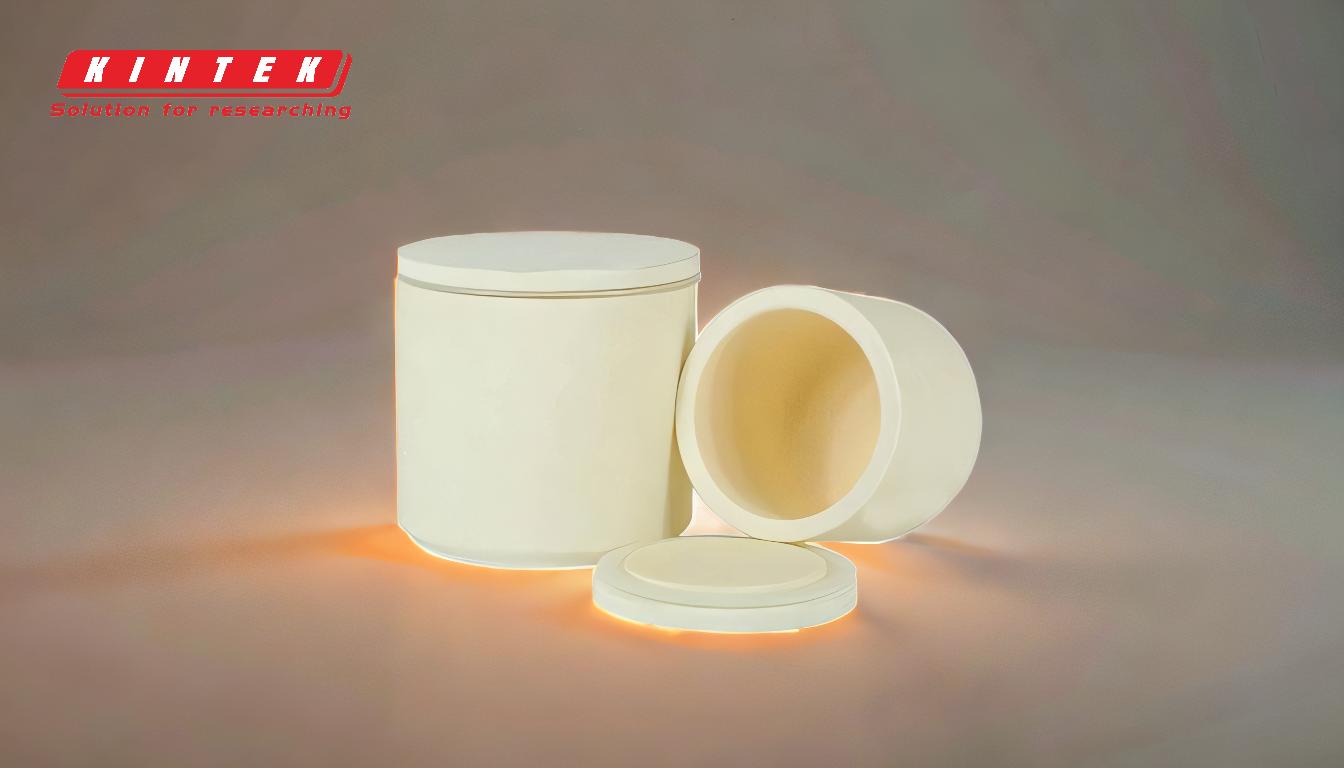
-
Primary Function in Ceramics: Grinding and Particle Size Reduction
- Ball mills are primarily used to grind ceramic raw materials like feldspar, pigments, and other minerals into fine powders.
- Reducing particle size is critical in ceramics to ensure uniformity, improve material reactivity, and achieve desired properties in the final product.
- The grinding process also helps eliminate agglomeration, ensuring a consistent and homogeneous mixture.
-
Wet and Dry Grinding Systems
- Ball mills can operate in both wet and dry conditions, making them adaptable to different ceramic processes.
- Wet grinding is often preferred for materials that require slurry formation, while dry grinding is suitable for powders or materials that are sensitive to moisture.
- The choice between wet and dry grinding depends on the specific requirements of the ceramic application.
-
Batch and Continuous Operations
- Ball mills can function in batch mode, where a specific quantity of material is processed at a time, or in continuous mode, where materials are fed and discharged continuously.
- Batch operations are ideal for small-scale or laboratory settings, while continuous operations are more efficient for large-scale industrial production.
- This flexibility allows ceramic manufacturers to tailor the milling process to their production needs.
-
Scalability for Small and Large Applications
- Ball mills are available in various sizes, from small laboratory-scale units to large industrial machines.
- Small-scale mills are used for research, development, and testing of ceramic materials, while large-scale mills are employed in mass production.
- This scalability ensures that ball mills can meet the needs of both small-scale artisans and large ceramic manufacturers.
-
Advanced Applications: Planetary Ball Mills
- Planetary ball mills are a specialized type of ball mill used for more demanding applications, such as mechanical alloying and advanced ceramic production.
- These mills provide higher energy input, enabling finer grinding and more efficient mixing of materials.
- They are particularly useful for creating advanced ceramics with specific mechanical, thermal, or electrical properties.
-
Role in Material Property Modification
- Ball mills not only grind materials but also modify their properties, such as particle shape and surface characteristics.
- This modification is essential for achieving desired properties in ceramic products, such as strength, durability, and aesthetic qualities.
- The mechanical energy from the milling process can also induce chemical or physical changes in the materials, enhancing their performance in ceramic applications.
-
Applications Beyond Ceramics
- While ball mills are widely used in ceramics, their versatility extends to other industries, including cement, fertilizers, and glass production.
- This cross-industry applicability highlights the importance of ball mills as a fundamental tool in material processing.
In summary, ball mills are indispensable in the ceramics industry for grinding, mixing, and modifying raw materials. Their adaptability to different processes, scalability, and ability to handle advanced applications make them a critical tool for achieving high-quality ceramic products. Whether used in small-scale research or large-scale production, ball mills ensure the consistency and performance of ceramic materials.
Summary Table:
Key Feature | Description |
---|---|
Primary Function | Grinding and reducing particle size of ceramic raw materials like feldspar and pigments. |
Wet and Dry Grinding | Operates in both wet (slurry formation) and dry (powder) conditions. |
Batch and Continuous Modes | Suitable for small-scale (batch) and large-scale (continuous) operations. |
Scalability | Available in sizes for lab research to industrial production. |
Advanced Applications | Planetary ball mills for mechanical alloying and advanced ceramic production. |
Material Property Modification | Modifies particle shape and surface characteristics for desired ceramic properties. |
Cross-Industry Use | Also used in cement, fertilizers, and glass production. |
Looking for the perfect ball mill for your ceramic production? Contact our experts today to find the right solution!