Sintered metals are materials formed by compacting and heating metal powders below their melting point, resulting in a solid structure with controlled porosity and strength. This process is widely used in industries such as automotive, aerospace, and biomedical engineering to create durable and precise components. Examples of sintered metals include automotive gears, turbine blades, and prosthetic joints. The sintering process mimics natural phenomena, such as the compaction of snow into ice, where pressure and heat transform loose particles into a cohesive structure.
Key Points Explained:
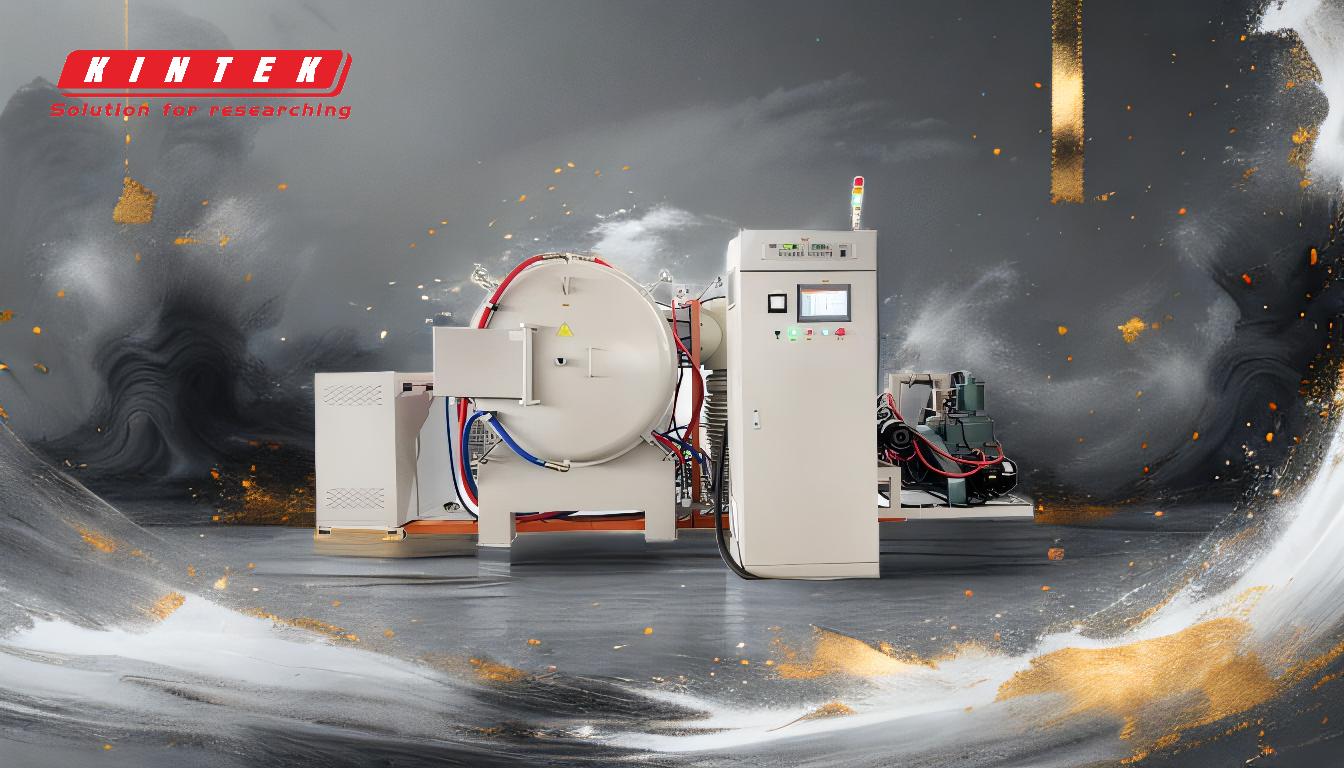
-
Definition of Sintered Metals:
- Sintered metals are created by compacting metal powders and heating them below their melting point. This process bonds the particles together, forming a solid structure with specific mechanical properties, such as strength and porosity.
- The sintering process is crucial for producing components with complex shapes and high precision, which are difficult to achieve through traditional manufacturing methods.
-
Examples of Sintered Metal Components:
- Automotive Parts: Sintered metals are used to manufacture gears, actuators, and other components that require high durability and wear resistance. These parts are essential for the smooth operation of vehicles.
- Electrical Components: Switchgear and other electrical parts are often made from sintered metals due to their excellent conductivity and mechanical strength.
- Cutting Tools: Tools such as milling cutters, drills, and reamers are produced using sintering to ensure hardness and longevity.
- Aerospace Components: Fuel valve components, actuators, and turbine blades are examples of sintered metals used in the aerospace industry, where lightweight and high-performance materials are critical.
- Biomedical Implants: Prosthetic joints and other implants are made from sintered metals because of their biocompatibility and ability to integrate with human tissue.
-
Sintering Process and Its Analogy:
- The sintering process involves applying heat and pressure to metal powders without completely melting them. This allows the particles to bond at their contact points, creating a cohesive structure.
- A simple analogy for sintering is the compaction of snow into ice. When a child compacts snow by applying pressure, the snow particles bond together to form a solid mass. Similarly, in sintering, heat and pressure transform loose metal particles into a solid component.
-
Advantages of Sintered Metals:
- Cost-Effectiveness: Sintering reduces material waste and allows for the production of complex shapes without extensive machining.
- Material Versatility: A wide range of metals and alloys can be sintered, including iron, copper, and titanium.
- Controlled Porosity: The porosity of sintered metals can be tailored to specific applications, such as filters or self-lubricating bearings.
- High Precision: Sintering enables the production of components with tight tolerances and intricate designs.
-
Applications Across Industries:
- Sintered metals are indispensable in industries that require high-performance materials. For example, in the automotive industry, they are used for transmission components and engine parts. In the biomedical field, they are utilized for implants that mimic the properties of natural bone.
By understanding the sintering process and its applications, purchasers of equipment and consumables can make informed decisions about the materials and components they need for specific industrial applications.
Summary Table:
Category | Examples of Sintered Metal Components |
---|---|
Automotive Parts | Gears, actuators, transmission components |
Electrical Parts | Switchgear, conductive components |
Cutting Tools | Milling cutters, drills, reamers |
Aerospace Parts | Turbine blades, fuel valve components, actuators |
Biomedical Implants | Prosthetic joints, bone implants |
Need sintered metal components for your industry? Contact us today to explore customized solutions!