Black PVD (Physical Vapor Deposition) coating is a thin-film coating process that creates a durable, protective, and aesthetically pleasing layer on a substrate. The black color is achieved by using specific materials and reactive gases during the PVD process. Typically, black PVD coatings are made from compounds like titanium nitride (TiN), titanium carbonitride (TiCN), or titanium aluminum nitride (TiAlN), which are formed by reacting metal targets with gases such as nitrogen or carbon. These coatings are highly adherent, corrosion-resistant, and provide a sleek black finish, making them popular in industries like jewelry, automotive, and consumer electronics.
Key Points Explained:
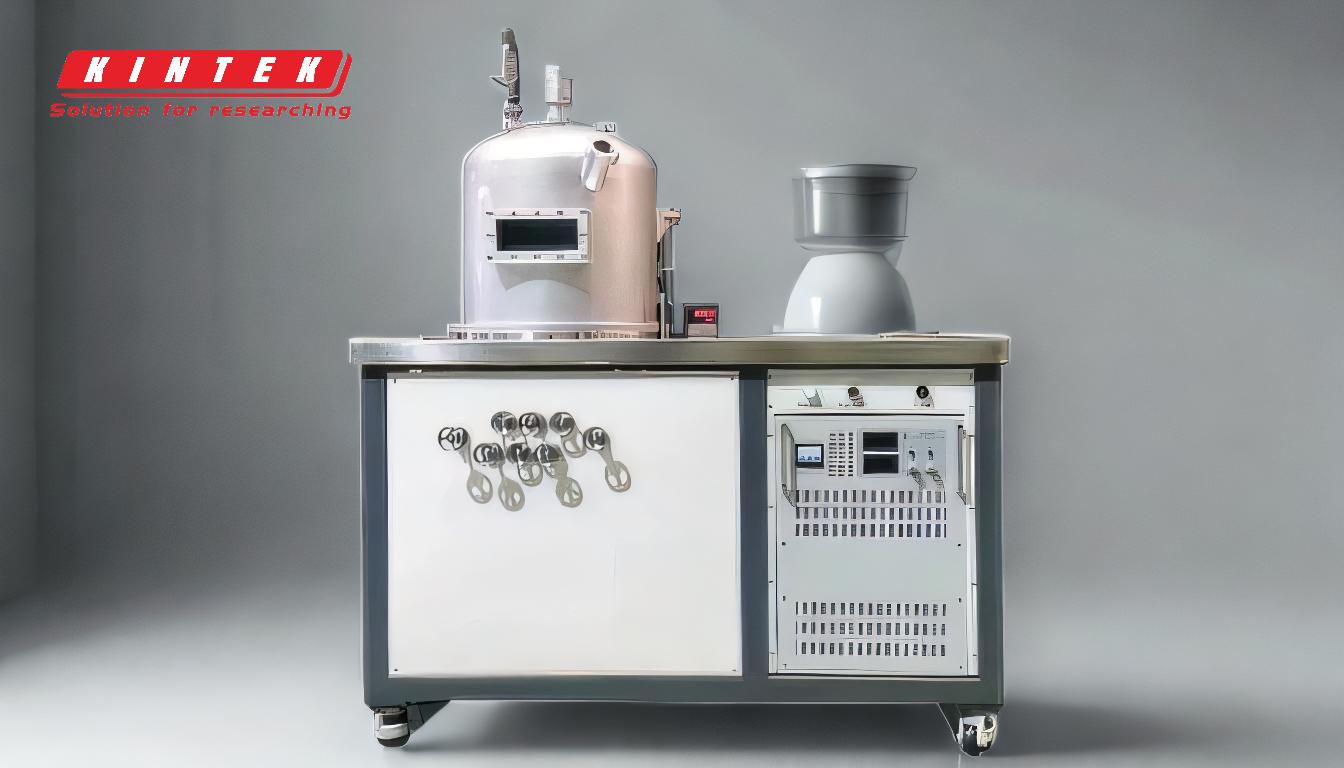
-
Composition of Black PVD Coating:
- Black PVD coatings are typically made from titanium-based compounds such as:
- Titanium Nitride (TiN): A hard, wear-resistant coating that can appear black under certain conditions.
- Titanium Carbonitride (TiCN): A combination of titanium, carbon, and nitrogen, which enhances hardness and provides a darker finish.
- Titanium Aluminum Nitride (TiAlN): Known for its high-temperature stability and dark appearance.
- These materials are chosen for their durability, corrosion resistance, and ability to achieve a black finish.
- Black PVD coatings are typically made from titanium-based compounds such as:
-
Role of Reactive Gases:
- The black color is achieved by introducing reactive gases like nitrogen (N₂) or carbon-containing gases (e.g., methane, CH₄) during the PVD process.
- These gases react with the metal target (e.g., titanium) to form compounds like TiN or TiCN, which contribute to the black appearance.
-
PVD Process Steps:
- The PVD process involves several key steps:
- Evaporation: The target material (e.g., titanium) is vaporized using high-energy sources like electron beams, ion bombardment, or cathodic arcs.
- Transportation: The vaporized atoms are transported through a vacuum chamber to the substrate.
- Reaction: The metal atoms react with reactive gases (e.g., nitrogen) to form compounds like TiN or TiCN.
- Deposition: The resulting compound forms a thin, adherent layer on the substrate, creating the black PVD coating.
- The PVD process involves several key steps:
-
Properties of Black PVD Coating:
- Durability: The coating is highly resistant to wear, scratches, and corrosion.
- Aesthetic Appeal: The black finish is sleek and modern, making it ideal for decorative applications like jewelry and watches.
- Environmental Friendliness: PVD is a clean process that produces minimal waste compared to traditional coating methods.
-
Applications of Black PVD Coating:
- Jewelry: Used to create a black, corrosion-resistant finish on rings, watches, and other accessories.
- Automotive: Applied to components like rims, trim, and engine parts for both protection and aesthetics.
- Consumer Electronics: Used on smartphones, laptops, and other devices for a premium look and durability.
- Industrial Tools: Enhances the lifespan and performance of cutting tools and molds.
-
Advantages Over Other Coating Methods:
- Thickness: PVD coatings are extremely thin (microns thick) but highly effective.
- Adhesion: The coating bonds strongly to the substrate, preventing flaking or peeling.
- Customizability: The process allows for precise control over the coating's composition and properties.
By understanding the materials, process, and benefits of black PVD coating, purchasers can make informed decisions about its use in various applications.
Summary Table:
Aspect | Details |
---|---|
Composition | Titanium-based compounds (TiN, TiCN, TiAlN) |
Reactive Gases | Nitrogen (N₂), carbon-containing gases (e.g., methane, CH₄) |
Process Steps | Evaporation, transportation, reaction, deposition |
Properties | Durable, corrosion-resistant, sleek black finish, eco-friendly |
Applications | Jewelry, automotive, consumer electronics, industrial tools |
Advantages | Thin, strong adhesion, customizable, wear-resistant |
Ready to enhance your products with black PVD coating? Contact us today to learn more!