Chemical vapor deposition (CVD) is a critical process in semiconductor manufacturing, enabling the deposition of high-quality, high-performance thin films onto substrates. This process involves introducing volatile precursor gases into a reaction chamber, where they decompose or react on the substrate's surface under controlled conditions of temperature, pressure, and flow rate. The resulting chemical reactions form a solid, uniform layer on the substrate, while volatile by-products are removed. CVD is widely used in industries ranging from semiconductors to packaging, as it allows for the creation of precise, nanoscale coatings essential for advanced electronics, artificial intelligence, and other high-tech applications.
Key Points Explained:
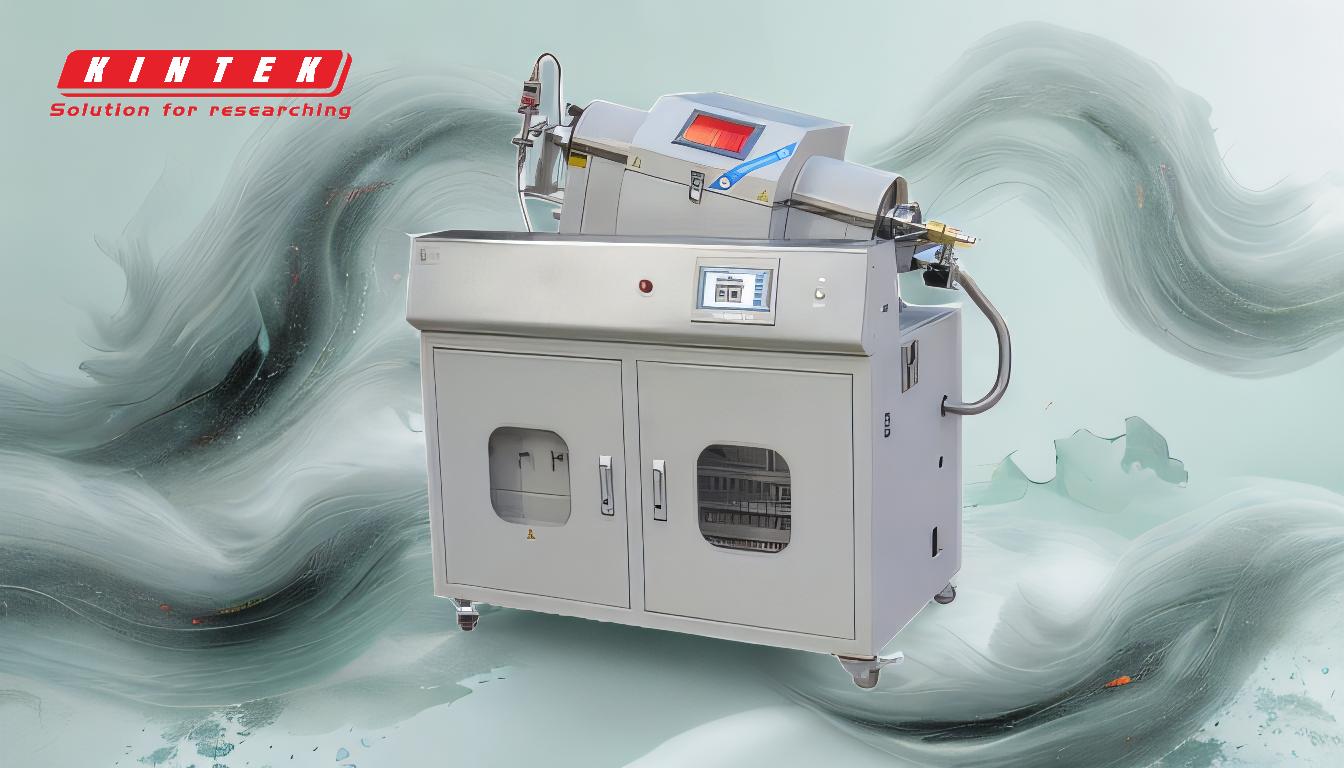
-
Definition and Purpose of CVD:
- CVD is a process used to deposit thin films of materials onto a substrate through chemical reactions.
- It is essential in semiconductor manufacturing for creating high-quality, high-performance solid materials like crystalline structures and fine powders.
- The process is versatile and used across industries, including electronics, packaging, and advanced technologies.
-
How CVD Works:
- Precursor gases are introduced into a reaction chamber, typically under vacuum conditions.
- These gases undergo decomposition or chemical reactions on the substrate's surface due to controlled temperature, pressure, and flow rate.
- The reaction results in the formation of a solid, uniform layer on the substrate, while volatile by-products are removed via gas flow.
-
Key Components of the CVD Process:
- Precursor Gases: Volatile materials that react or decompose to form the desired coating.
- Reaction Chamber: A controlled environment, often under vacuum, where the chemical reactions occur.
- Substrate: The surface onto which the thin film is deposited.
- Heating and Pressure Control: Critical for ensuring the proper decomposition and bonding of materials.
-
Types of CVD Mechanisms:
- Thermal CVD: Uses heat to drive the chemical reactions.
- Plasma-Enhanced CVD (PECVD): Utilizes plasma to lower the reaction temperature.
- Low-Pressure CVD (LPCVD): Operates at reduced pressures for better uniformity.
- Laser-Assisted CVD: Employs laser irradiation to initiate reactions.
- Photochemical CVD: Uses light to drive the chemical processes.
-
Applications of CVD:
- Semiconductors: Deposition of thin films for transistors, integrated circuits, and other electronic components.
- Packaging: Coating materials like aluminum onto packaging films (e.g., potato chip bags).
- Advanced Technologies: Creation of nanoscale materials for artificial intelligence, sensors, and other high-tech devices.
-
Advantages of CVD:
- High-quality, uniform coatings with precise control over thickness and composition.
- Ability to deposit a wide range of materials, including metals, ceramics, and polymers.
- Suitable for creating nanoscale and complex structures required in modern electronics.
-
Challenges and Considerations:
- Requires precise control of process parameters (temperature, pressure, flow rate).
- High equipment and operational costs.
- Potential for toxic by-products, necessitating proper safety and disposal measures.
-
Importance in Modern Manufacturing:
- Enables the production of smaller, more powerful, and efficient devices.
- Critical for advancements in semiconductor technology, which underpins modern electronics and computing.
- Supports innovation in industries such as renewable energy, healthcare, and telecommunications.
By understanding the principles, mechanisms, and applications of CVD, manufacturers can leverage this technology to produce cutting-edge materials and devices that drive progress across multiple industries.
Summary Table:
Aspect | Details |
---|---|
Definition | A process to deposit thin films via chemical reactions on substrates. |
Key Components | Precursor gases, reaction chamber, substrate, temperature/pressure control. |
Types of CVD | Thermal, Plasma-Enhanced (PECVD), Low-Pressure (LPCVD), Laser-Assisted. |
Applications | Semiconductors, packaging, AI, sensors, and advanced electronics. |
Advantages | High-quality, uniform coatings; nanoscale precision; versatile materials. |
Challenges | Precise control required; high costs; potential toxic by-products. |
Discover how CVD can revolutionize your manufacturing process—contact our experts today!