Chemical vapor deposition (CVD) is a sophisticated process used to create thin films or coatings on a substrate by inducing chemical reactions in the vapor phase. This method is widely employed in industries such as semiconductors, optics, and materials science due to its precision and versatility. The process involves several key steps, including the transportation of gaseous reactants to the substrate, adsorption, chemical reactions on the surface, and the formation of a solid film. The resulting coatings can range from metals to semiconductors, depending on the target materials and deposition conditions. CVD is distinct from physical vapor deposition (PVD) as it relies on chemical reactions rather than physical processes like evaporation or sputtering.
Key Points Explained:
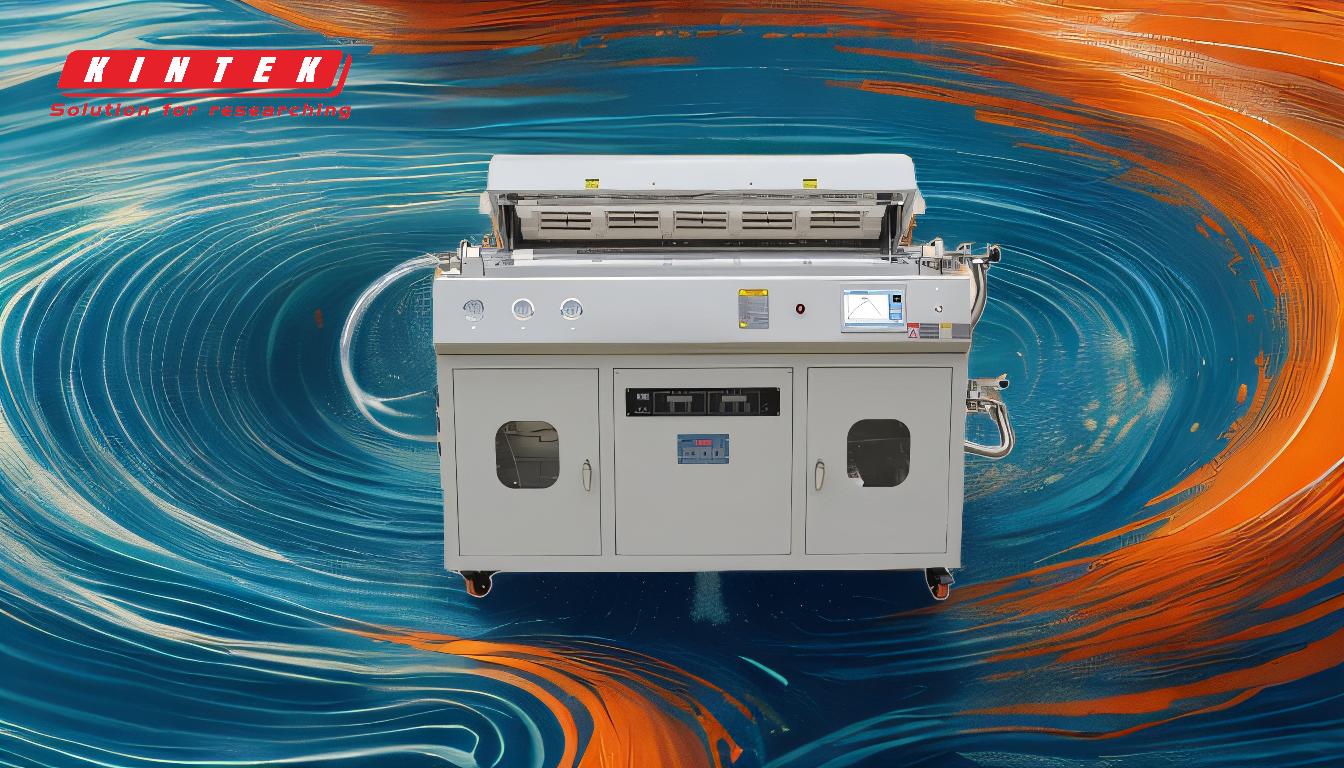
-
Definition and Purpose of CVD:
- Chemical vapor deposition (CVD) is a process where a thin solid film is formed on a substrate through chemical reactions in the vapor phase. This method is used to deposit materials such as metals, semiconductors, and polymers onto surfaces for applications in electronics, optics, and protective coatings.
-
Steps Involved in the CVD Process:
- Transport of Reacting Gases: Gaseous reactants are transported to the substrate surface.
- Adsorption: The reactants adsorb onto the substrate surface.
- Chemical Reactions: Heterogeneous surface-catalyzed reactions occur, leading to the formation of solid products.
- Surface Diffusion: The species diffuse to growth sites on the substrate.
- Nucleation and Growth: The solid film nucleates and grows on the substrate.
- Desorption and Removal: Gaseous byproducts desorb from the surface and are transported away.
-
Key Process Elements:
- Target Materials: These can include metals, semiconductors, or polymers, depending on the desired film properties.
- Deposition Technologies: Techniques such as plasma-enhanced CVD (PECVD), atomic layer deposition (ALD), and atmospheric pressure CVD (APCVD) are used to control the deposition process.
- Chamber Pressure and Substrate Temperature: These parameters significantly influence the rate and quality of film deposition.
-
Comparison with Physical Vapor Deposition (PVD):
- Unlike PVD, which relies on physical processes like evaporation or sputtering, CVD involves chemical reactions to form the film. This distinction allows CVD to produce more complex and high-quality coatings.
-
Applications of CVD:
- CVD is used in the fabrication of semiconductor devices, optical coatings, and protective layers. It is also employed in the production of advanced materials like graphene and carbon nanotubes.
-
Advantages of CVD:
- High precision and control over film thickness and composition.
- Ability to deposit a wide range of materials.
- Suitable for large-scale and complex geometries.
-
Challenges in CVD:
- Requires precise control of process parameters such as temperature, pressure, and gas flow rates.
- Can involve toxic or hazardous chemicals, necessitating careful handling and safety measures.
In summary, chemical vapor deposition is a versatile and precise method for depositing thin films on substrates through chemical reactions in the vapor phase. Its applications span various industries, and its ability to produce high-quality coatings makes it a critical technology in modern manufacturing and materials science.
Summary Table:
Aspect | Details |
---|---|
Definition | A process to form thin solid films via chemical reactions in the vapor phase. |
Key Steps | Transport, adsorption, chemical reactions, surface diffusion, nucleation, desorption. |
Target Materials | Metals, semiconductors, polymers. |
Deposition Technologies | PECVD, ALD, APCVD. |
Applications | Semiconductors, optical coatings, advanced materials like graphene. |
Advantages | High precision, versatile material deposition, suitable for complex geometries. |
Challenges | Requires precise control of parameters; handling of toxic chemicals. |
Discover how CVD can enhance your manufacturing process—contact our experts today!