A controlled atmosphere temperature treatment system is a specialized setup used in industrial processes, particularly for heat treatment of metals. It involves creating a controlled environment within a furnace or oven where the composition of gases (such as oxygen, carbon dioxide, and nitrogen) is precisely regulated. This system ensures that metal parts are heated and cooled under optimal conditions, minimizing oxidation, decarburization, and contamination. The controlled atmosphere enhances the mechanical properties of the metal, such as strength, toughness, and resistance to wear and corrosion. Additionally, it improves production efficiency, reduces material waste, and ensures consistent product quality. This system is widely used in industries requiring high precision and reliability in metal treatment processes.
Key Points Explained:
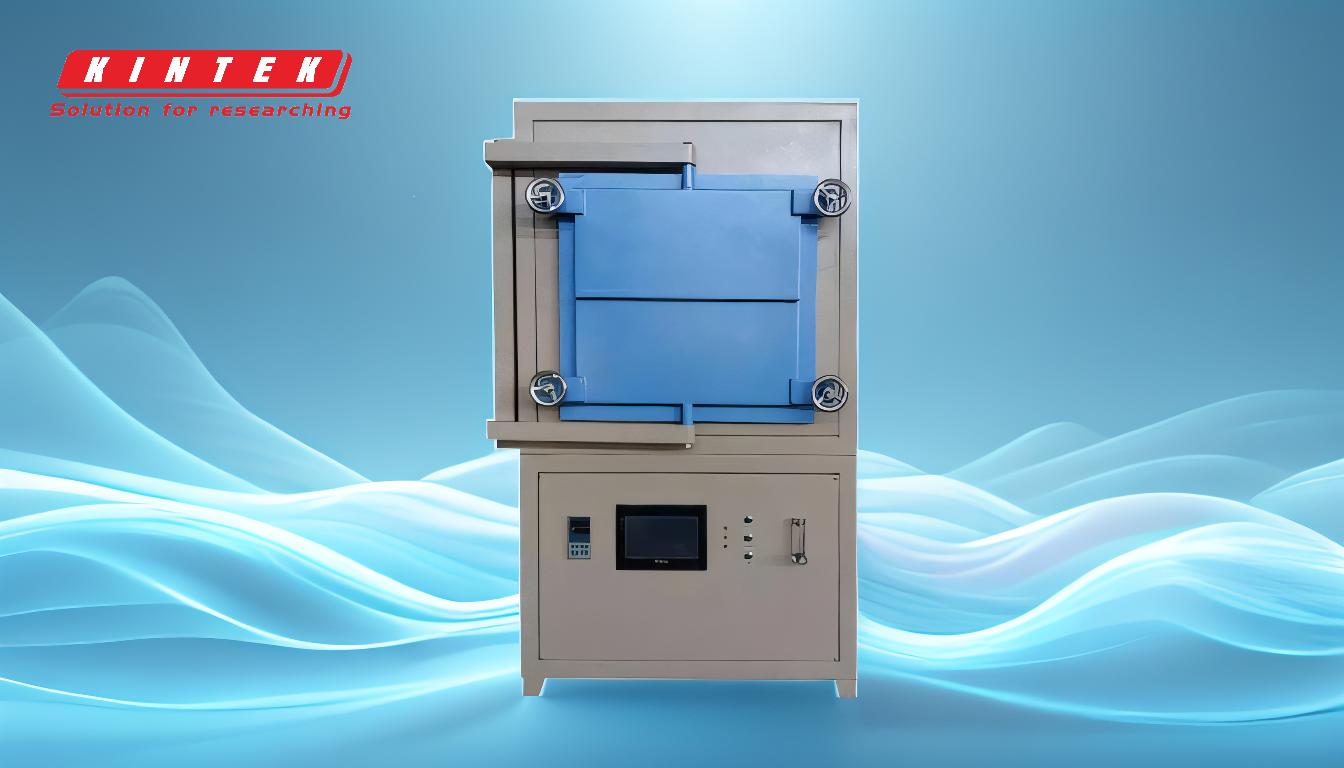
-
Definition and Purpose:
- A controlled atmosphere temperature treatment system is designed to create a precisely regulated environment for heat treatment processes.
- Its primary purpose is to enhance the mechanical properties of metal parts, such as strength, toughness, and resistance to wear and corrosion, while minimizing defects like oxidation and decarburization.
-
Components and Operation:
- The system typically includes a furnace or oven equipped with gas flow controls and sensors to monitor and adjust the atmosphere.
- Gases such as nitrogen, carbon dioxide, and oxygen are carefully mixed and circulated to achieve the desired composition.
- Temperature is precisely controlled to ensure uniform heating and cooling of the metal parts.
-
Benefits of Controlled Atmosphere:
- Improved Product Quality: By preventing oxidation and decarburization, the system ensures consistent and high-quality results.
- Enhanced Mechanical Properties: The controlled environment allows for precise alteration of the metal's microstructure, improving its performance.
- Increased Efficiency: The system reduces material waste and processing time, leading to higher productivity.
- Reduced Contamination: The controlled atmosphere minimizes the risk of contamination from external elements, ensuring the integrity of the metal parts.
-
Applications:
- Heat Treatment of Metals: Used in processes like annealing, carburizing, and quenching to improve the properties of steel and other alloys.
- Industrial Manufacturing: Commonly employed in industries such as automotive, aerospace, and tool manufacturing, where high precision and reliability are critical.
- Complex Part Processing: Simplifies the treatment of complex-shaped parts by using low-carbon steel and later performing carbon infiltration.
-
Key Features:
- Precision Control: The system allows for strict control of gas composition and temperature, ensuring optimal conditions for heat treatment.
- Automation and Mechanization: Facilitates automated processes, reducing labor intensity and improving consistency.
- Versatility: Can be used for various heat treatment processes, including carbon reinforcement and repair treatments.
-
Advantages Over Traditional Methods:
- Reduced Oxidation: The controlled atmosphere significantly reduces the risk of oxidation, which can degrade the quality of metal parts.
- Improved Surface Quality: By preventing decarburization, the system enhances the surface quality and mechanical properties of the treated parts.
- Cost Efficiency: The system reduces material waste and energy consumption, leading to cost savings in the long run.
-
Challenges and Considerations:
- Initial Investment: The setup and maintenance of a controlled atmosphere system can be costly, requiring specialized equipment and expertise.
- Complexity: The process requires precise control and monitoring, which can be challenging without proper training and equipment.
- Safety Concerns: Handling and regulating gases in a controlled environment requires strict safety protocols to prevent accidents.
In summary, a controlled atmosphere temperature treatment system is a sophisticated solution for enhancing the quality and performance of metal parts through precise control of the heating environment. Its benefits in terms of product quality, efficiency, and versatility make it an essential tool in modern industrial manufacturing.
Summary Table:
Aspect | Details |
---|---|
Purpose | Enhances mechanical properties of metals, minimizes oxidation and defects. |
Key Components | Furnace/oven, gas flow controls, sensors, and precise temperature systems. |
Benefits | Improved product quality, enhanced efficiency, reduced contamination. |
Applications | Automotive, aerospace, tool manufacturing, and complex part processing. |
Key Features | Precision control, automation, versatility in heat treatment processes. |
Advantages | Reduced oxidation, improved surface quality, cost efficiency. |
Challenges | High initial investment, complexity, and safety concerns. |
Ready to optimize your metal treatment processes? Contact us today to learn more about controlled atmosphere systems!