The Chemical Vapor Deposition (CVD) method is a widely used technique in the synthesis of nanomaterials. It involves the chemical reaction of vapor-phase precursors to form solid materials on a substrate. This process is highly versatile and can be used to produce a variety of nanomaterials, including thin films, nanotubes, and nanoparticles. CVD is favored for its ability to produce high-purity, high-performance materials with precise control over composition and structure. The method is used in various industries, including electronics, optics, and energy storage, due to its scalability and the high quality of the materials it produces.
Key Points Explained:
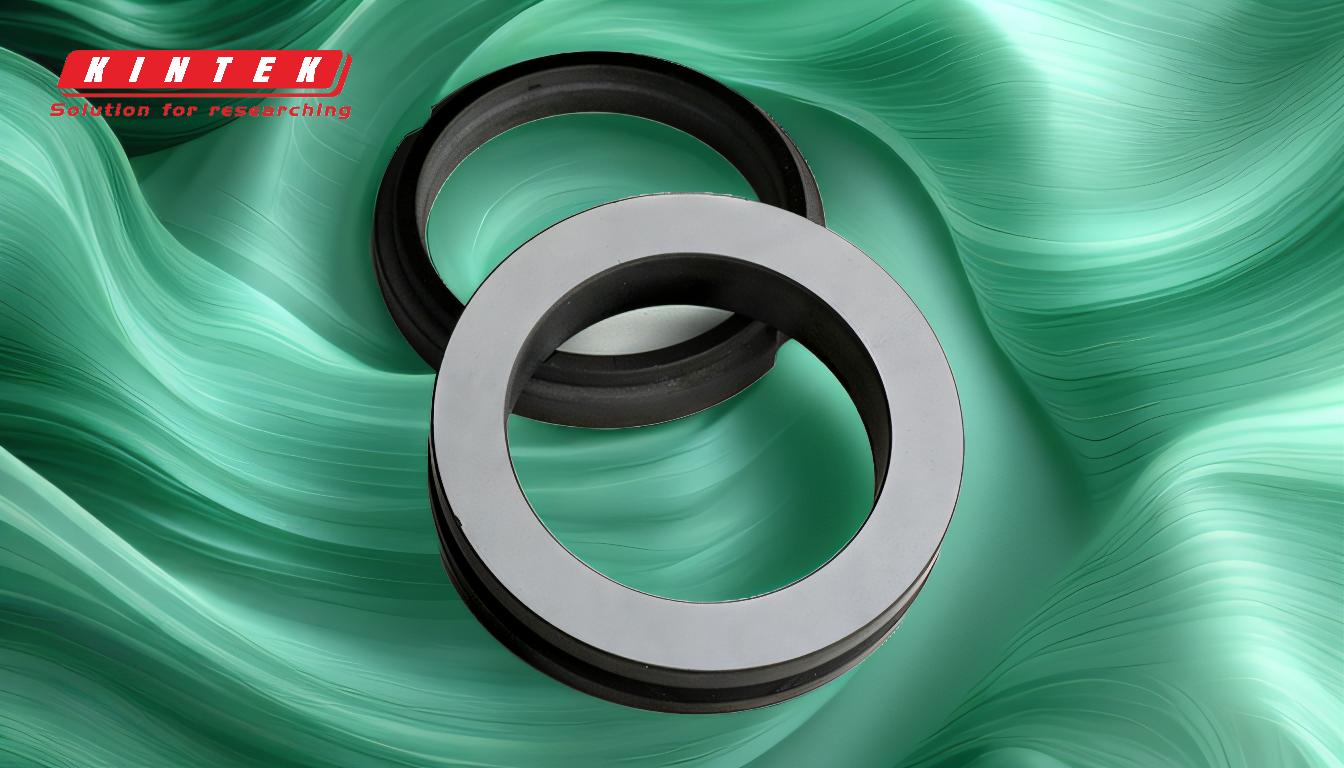
-
Definition of CVD:
- Chemical Vapor Deposition (CVD) is a process where chemical reactions in the vapor phase are used to deposit solid materials onto a substrate. This method is essential in the production of nanomaterials due to its precision and control over material properties.
-
Process Overview:
- Precursor Introduction: Gaseous or vaporized precursors are introduced into a reaction chamber.
- Chemical Reaction: These precursors undergo chemical reactions, often facilitated by heat, plasma, or catalysts, to form the desired material.
- Deposition: The reaction products deposit onto a substrate, forming a thin film or nanostructure.
- Byproduct Removal: Any gaseous byproducts are removed from the chamber.
-
Types of CVD:
- Atmospheric Pressure CVD (APCVD): Operates at atmospheric pressure, suitable for large-scale production.
- Low-Pressure CVD (LPCVD): Conducted under reduced pressure, offering better control over film thickness and uniformity.
- Plasma-Enhanced CVD (PECVD): Uses plasma to enhance the chemical reaction, allowing for lower temperature processes.
- Metal-Organic CVD (MOCVD): Employs metal-organic precursors, commonly used for compound semiconductors.
-
Applications in Nanomaterials:
- Thin Films: Used in semiconductor devices, solar cells, and protective coatings.
- Nanotubes and Nanowires: Essential for electronic, photonic, and sensor applications.
- Nanoparticles: Applied in catalysis, drug delivery, and energy storage.
-
Advantages of CVD:
- High Purity: Produces materials with minimal impurities.
- Precision: Allows for precise control over material composition and structure.
- Versatility: Can be used to deposit a wide range of materials, including metals, semiconductors, and ceramics.
- Scalability: Suitable for both laboratory-scale research and industrial production.
-
Challenges and Considerations:
- Cost: High equipment and operational costs.
- Complexity: Requires careful control of process parameters.
- Safety: Handling of toxic or flammable precursors necessitates stringent safety measures.
-
Future Directions:
- Advanced Precursors: Development of new precursors for more efficient and safer processes.
- Nanostructure Control: Enhanced techniques for controlling the size, shape, and arrangement of nanostructures.
- Integration with Other Technologies: Combining CVD with other nanofabrication methods for multifunctional materials.
The CVD method is a cornerstone in the field of nanomaterials, offering unparalleled control and versatility in material synthesis. Its continued development and integration with emerging technologies hold promise for groundbreaking advancements in various industries.
Summary Table:
Aspect | Details |
---|---|
Definition | Chemical reactions in vapor phase deposit solid materials onto a substrate. |
Process Steps | Precursor introduction → Chemical reaction → Deposition → Byproduct removal |
Types of CVD | APCVD, LPCVD, PECVD, MOCVD |
Applications | Thin films, nanotubes, nanoparticles |
Advantages | High purity, precision, versatility, scalability |
Challenges | High cost, complexity, safety concerns |
Future Directions | Advanced precursors, nanostructure control, integration with other methods |
Discover how CVD can revolutionize your material synthesis—contact our experts today!