The Chemical Vapor Deposition (CVD) method is a widely used technique for the preparation of nanomaterials. It involves the deposition of a solid material from a gaseous phase onto a substrate, where chemical reactions occur at the surface of the substrate. This process is particularly useful for creating thin films and coatings with precise control over thickness, composition, and structure. CVD is employed in various industries, including electronics, optics, and materials science, to produce high-quality nanomaterials with specific properties.
Key Points Explained:
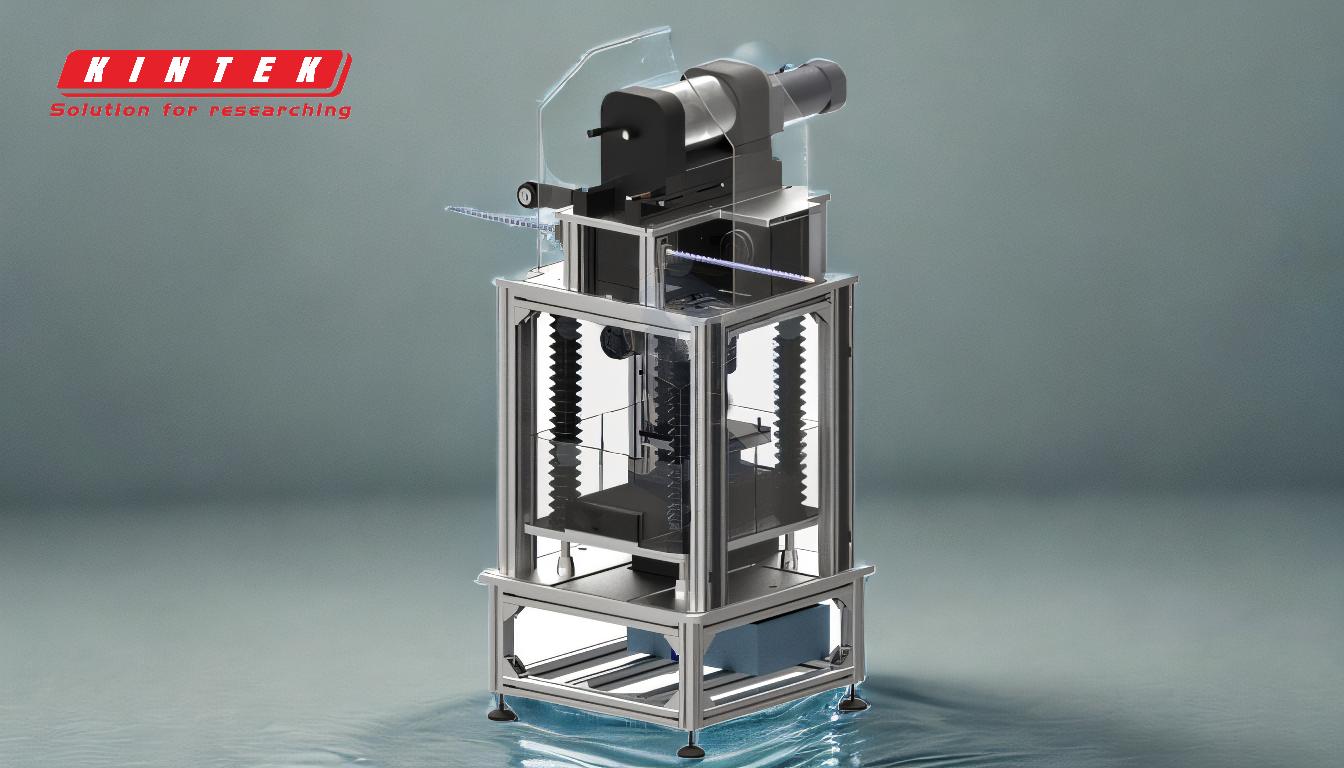
-
Basic Principle of CVD:
- CVD involves the use of volatile precursors that are introduced into a reaction chamber. These precursors react or decompose on a heated substrate, forming a solid deposit. The process typically occurs under controlled temperature and pressure conditions to ensure the desired material properties.
-
Types of CVD:
- Atmospheric Pressure CVD (APCVD): Operates at atmospheric pressure, suitable for large-scale production.
- Low-Pressure CVD (LPCVD): Conducted under reduced pressure, offering better uniformity and step coverage.
- Plasma-Enhanced CVD (PECVD): Utilizes plasma to enhance chemical reactions, allowing deposition at lower temperatures.
- Metal-Organic CVD (MOCVD): Uses metal-organic precursors, commonly used for compound semiconductors.
-
Advantages of CVD:
- High Purity: Produces materials with high purity and controlled composition.
- Uniformity: Ensures uniform coatings and thin films, even on complex geometries.
- Versatility: Can deposit a wide range of materials, including metals, semiconductors, and ceramics.
-
Applications of CVD:
- Electronics: Used in the fabrication of integrated circuits, solar cells, and LEDs.
- Optics: Produces anti-reflective coatings and optical filters.
- Materials Science: Creates protective coatings, wear-resistant layers, and nanocomposites.
-
Role of Vacuum in CVD:
- Reduced Pressure: Similar to short path vacuum distillation, vacuum conditions in CVD help lower the reaction temperature and reduce unwanted side reactions. This is particularly beneficial for depositing materials that are sensitive to high temperatures.
- Enhanced Control: Vacuum environments allow for better control over the deposition process, leading to higher quality and more consistent results.
-
Comparison with Other Methods:
- Physical Vapor Deposition (PVD): Unlike CVD, PVD involves physical processes like sputtering or evaporation, without chemical reactions. CVD generally offers better step coverage and is more suitable for complex geometries.
- Sol-Gel Process: While sol-gel is a solution-based method, CVD is gas-phase, offering better control over film thickness and composition.
-
Challenges and Considerations:
- Cost: CVD equipment and precursors can be expensive, making it less accessible for small-scale operations.
- Safety: Handling volatile and sometimes toxic precursors requires stringent safety measures.
- Complexity: The process parameters (temperature, pressure, gas flow rates) need precise control to achieve the desired material properties.
In summary, the CVD method is a versatile and powerful technique for the preparation of nanomaterials, offering high purity, uniformity, and control over material properties. Its applications span across various industries, and the use of vacuum conditions enhances its efficiency and effectiveness. Understanding the principles and advantages of CVD can help in selecting the appropriate method for specific nanomaterial synthesis needs.
Summary Table:
Aspect | Details |
---|---|
Basic Principle | Deposition of solid material from gaseous phase onto a heated substrate. |
Types of CVD | APCVD, LPCVD, PECVD, MOCVD. |
Advantages | High purity, uniformity, versatility in material deposition. |
Applications | Electronics (ICs, solar cells), optics (anti-reflective coatings), materials science. |
Role of Vacuum | Reduces reaction temperature, enhances control, and improves quality. |
Challenges | High cost, safety concerns, and process complexity. |
Discover how the CVD method can revolutionize your nanomaterial synthesis—contact our experts today for tailored solutions!