Deposition in nanotechnology refers to the process of applying thin layers of material onto a substrate, typically at the nanoscale. This process is essential for creating functional coatings, electronic components, and other advanced materials. Deposition techniques can be broadly categorized into physical vapor deposition (PVD) and chemical vapor deposition (CVD), each with its own set of methods and applications. These techniques are crucial for producing high-quality, defect-free thin films used in various industries, including electronics, optics, and energy.
Key Points Explained:
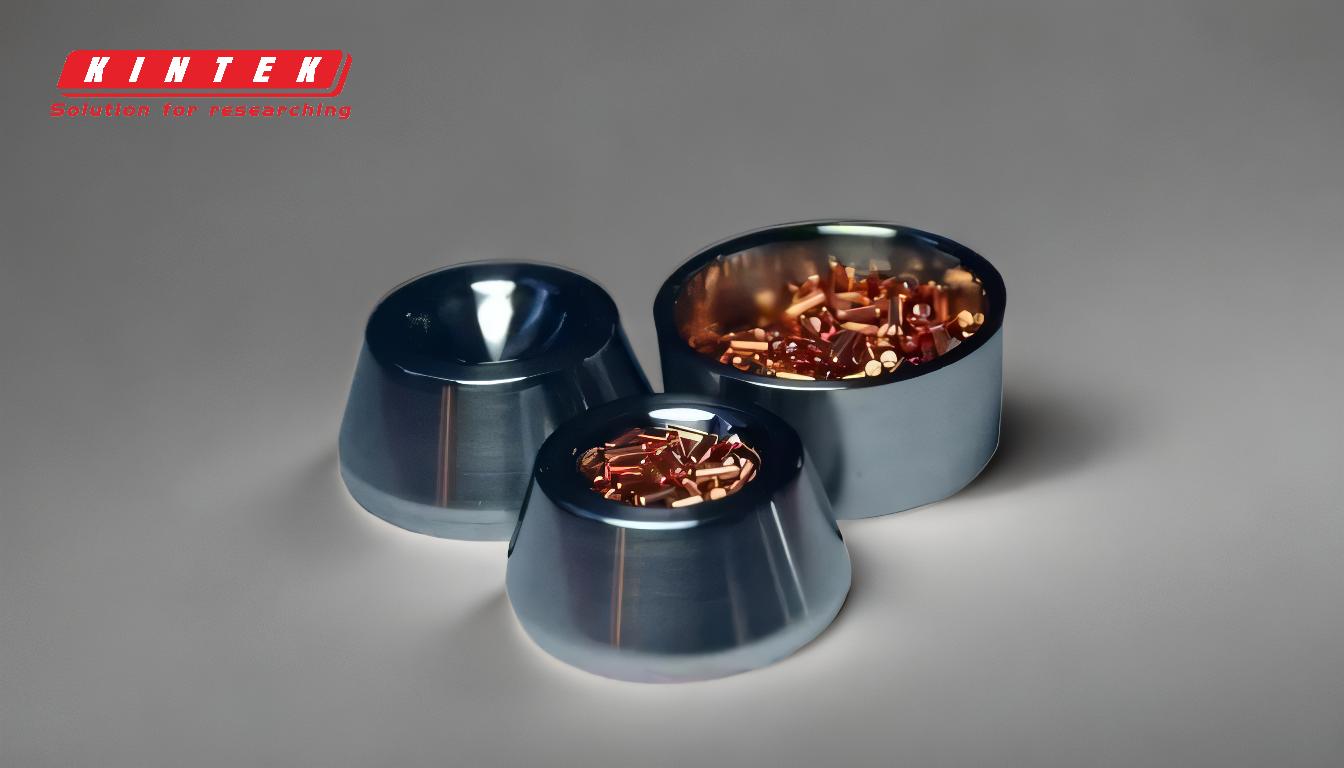
-
Definition of Deposition in Nanotechnology:
- Deposition involves the application of thin layers of material onto a substrate, often at the nanoscale.
- This process is fundamental in creating functional coatings and electronic components.
-
Categories of Deposition Techniques:
-
Physical Vapor Deposition (PVD):
- Involves the physical transfer of material from a source to the substrate.
- Common methods include evaporation and sputtering.
- Evaporation: Material is heated until it vaporizes and then condenses on the substrate.
- Sputtering: Atoms are ejected from a solid target material due to bombardment by energetic ions, then deposited on the substrate.
-
Chemical Vapor Deposition (CVD):
- Involves chemical reactions to produce a thin film on the substrate.
- Common methods include chemical bath deposition, electroplating, and thermal oxidation.
- Chemical Bath Deposition: A solution-based method where the substrate is immersed in a chemical bath to form a thin film.
- Electroplating: Uses an electric current to reduce dissolved metal cations, forming a coherent metal coating on the substrate.
- Thermal Oxidation: Involves heating the substrate in an oxygen-rich environment to form an oxide layer.
-
Physical Vapor Deposition (PVD):
-
Advantages of PVD and CVD:
-
PVD:
- Produces high-purity coatings with low levels of defects.
- Suitable for creating dense, well-adhered films.
-
CVD:
- Allows for precise control over film composition and thickness.
- Can produce uniform coatings over complex geometries.
-
PVD:
-
Common Deposition Technologies:
- Low Pressure Chemical Vapor Deposition (LPCVD): Operates at reduced pressures to enhance film uniformity.
- Plasma Enhanced Chemical Vapor Deposition (PECVD): Uses plasma to enhance chemical reactions, allowing deposition at lower temperatures.
- Atomic Layer Deposition (ALD): Provides atomic-level control over film thickness, resulting in highly uniform and conformal coatings.
- Magnetron Sputtering: A PVD technique that uses magnetic fields to confine plasma, improving deposition rates and film quality.
-
Applications of Deposition in Nanotechnology:
- Electronics: Used in the fabrication of semiconductors, transistors, and integrated circuits.
- Optics: Applied in the production of anti-reflective coatings, mirrors, and optical filters.
- Energy: Utilized in the development of photovoltaic cells, fuel cells, and batteries.
-
Importance of High-Quality Thin Films:
- High-quality thin films are essential for the performance and reliability of electronic devices.
- Techniques like PVD and CVD are crucial for producing films with minimal defects and high uniformity.
By understanding these key points, one can appreciate the critical role deposition plays in nanotechnology and the various methods available to achieve high-quality thin films.
Summary Table:
Aspect | Details |
---|---|
Definition | Applying thin layers of material onto a substrate at the nanoscale. |
Categories | Physical Vapor Deposition (PVD) and Chemical Vapor Deposition (CVD). |
PVD Methods | Evaporation, Sputtering. |
CVD Methods | Chemical Bath Deposition, Electroplating, Thermal Oxidation. |
Advantages | High-purity coatings, precise control, uniform films, and minimal defects. |
Applications | Electronics, Optics, Energy (e.g., semiconductors, mirrors, solar cells). |
Key Technologies | LPCVD, PECVD, ALD, Magnetron Sputtering. |
Discover how deposition techniques can revolutionize your projects—contact us today for expert guidance!