Sputtering is a physical vapor deposition (PVD) technique used to deposit thin films onto substrates. It involves bombarding a target material with high-energy ions, typically from a noble gas like argon, which dislodges atoms from the target. These atoms then travel through a vacuum and deposit onto a substrate, forming a thin film. Sputtering is widely used in industries such as semiconductors, optics, and coatings due to its ability to produce high-quality, uniform films with excellent adhesion and precise control over film properties. The process is versatile, working with a wide range of materials, including metals, alloys, and compounds, and can be performed at relatively low temperatures, making it suitable for sensitive substrates like plastics and organics.
Key Points Explained:
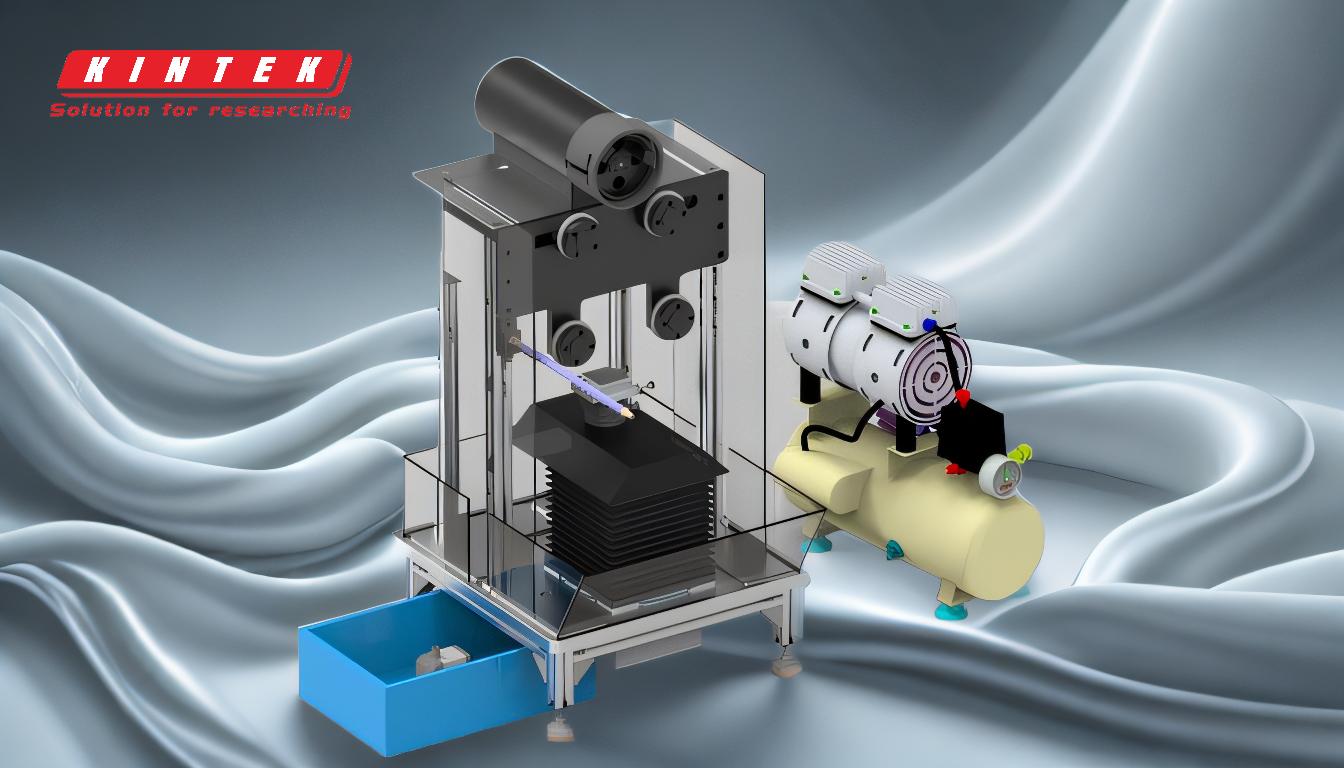
-
Mechanism of Sputtering:
- Sputtering involves the use of a noble gas plasma (usually argon) to bombard a target material.
- High-energy ions from the plasma collide with the target, dislodging atoms through a process called the collision cascade.
- These ejected atoms travel through a vacuum and deposit onto a substrate, forming a thin film.
-
Advantages of Sputtering:
- Versatility: Sputtering can deposit a wide range of materials, including metals, alloys, compounds, and even materials with very high melting points that are difficult to evaporate.
- Precision and Control: The process allows for molecular-level precision, enabling the creation of pristine interfaces and the ability to tune film properties by controlling process parameters.
- Low Temperature Operation: Sputtering can be performed at reduced temperatures, making it suitable for coating sensitive materials like plastics, organics, and glass.
- Better Adhesion: Sputter-ejected atoms have higher kinetic energies compared to evaporated materials, resulting in better adhesion to the substrate.
- Uniformity and Density: Sputtered films are typically more uniform and have higher packing densities, even at low temperatures.
- Reproducibility and Automation: Sputter deposition is highly reproducible and easier to automate compared to other methods like thermal evaporation or E-Beam deposition.
-
Applications of Sputter Deposition:
- Optical Films: Sputtering is used to deposit optical films by oxidizing or nitriding sputtered metal ions to form oxide or nitride layers with desired compositions.
- Semiconductors: The technique is widely used in the semiconductor industry for depositing thin films of metals, dielectrics, and other materials.
- Coatings: Sputtering is used to apply protective or functional coatings on various substrates, including glass, metals, and plastics.
- Advanced Processes: Sputtering supports advanced processes like epitaxial growth, which is crucial for creating high-quality crystalline films.
-
Process Parameters and Control:
- Gas Composition: The choice of gas (e.g., argon) and the introduction of reactive gases (e.g., oxygen or nitrogen) can influence the properties of the deposited film.
- Pressure and Power: The pressure within the sputtering chamber and the power applied to the target can be adjusted to control the rate and quality of deposition.
- Substrate Positioning: The distance between the target and substrate, as well as the orientation of the substrate, can affect the uniformity and adhesion of the film.
-
Comparison with Other Deposition Methods:
- Thermal Evaporation: Unlike thermal evaporation, sputtering does not require high temperatures to vaporize the target material, making it suitable for a broader range of materials and substrates.
- E-Beam Deposition: Sputtering offers better reproducibility and simpler automation compared to E-Beam deposition, which can be more complex and less consistent.
- Chemical Vapor Deposition (CVD): Sputtering is a physical process, whereas CVD is a chemical process. Sputtering is often preferred for its ability to deposit pure films without the need for chemical precursors.
-
Maintenance and Operational Considerations:
- Maintenance-Free: Sputtering systems are generally maintenance-free, with long-lived targets that provide a stable vaporization source.
- Ultrahigh Vacuum Compatibility: The process is compatible with ultrahigh vacuum conditions, which are essential for certain high-purity applications.
- Reactive Deposition: Sputtering can easily incorporate reactive gases to form compound films, such as oxides or nitrides, directly during the deposition process.
In summary, sputtering is a highly versatile and precise method for depositing thin films, offering numerous advantages over other deposition techniques. Its ability to work with a wide range of materials, produce uniform and adherent films, and operate at low temperatures makes it a preferred choice in many industrial and research applications.
Summary Table:
Aspect | Key Details |
---|---|
Mechanism | Bombards target material with high-energy ions (e.g., argon) to deposit thin films. |
Advantages | Versatile, precise, low-temperature operation, better adhesion, uniform films. |
Applications | Semiconductors, optical films, coatings, and advanced processes like epitaxy. |
Process Control | Adjust gas composition, pressure, power, and substrate positioning for precision. |
Comparison | Superior to thermal evaporation, E-Beam, and CVD in reproducibility and purity. |
Maintenance | Maintenance-free, ultrahigh vacuum compatible, supports reactive deposition. |
Ready to explore sputtering for your next project? Contact us today to learn more!