Dry Film Thickness (DFT) refers to the thickness of a coating applied to a substrate, measured after the coating has cured. It represents the total thickness of the coating, whether it is a single layer or multiple layers combined. DFT is a critical parameter in coating applications, as it directly impacts the performance, durability, and quality of the coated product. Accurate measurement of DFT ensures that the coating meets specified requirements, avoiding issues such as excessive material usage (increasing costs) or insufficient thickness (compromising protection or functionality). DFT is typically measured on cured coatings at ambient temperature, making it a practical and essential metric in industries like manufacturing, construction, and automotive.
Key Points Explained:
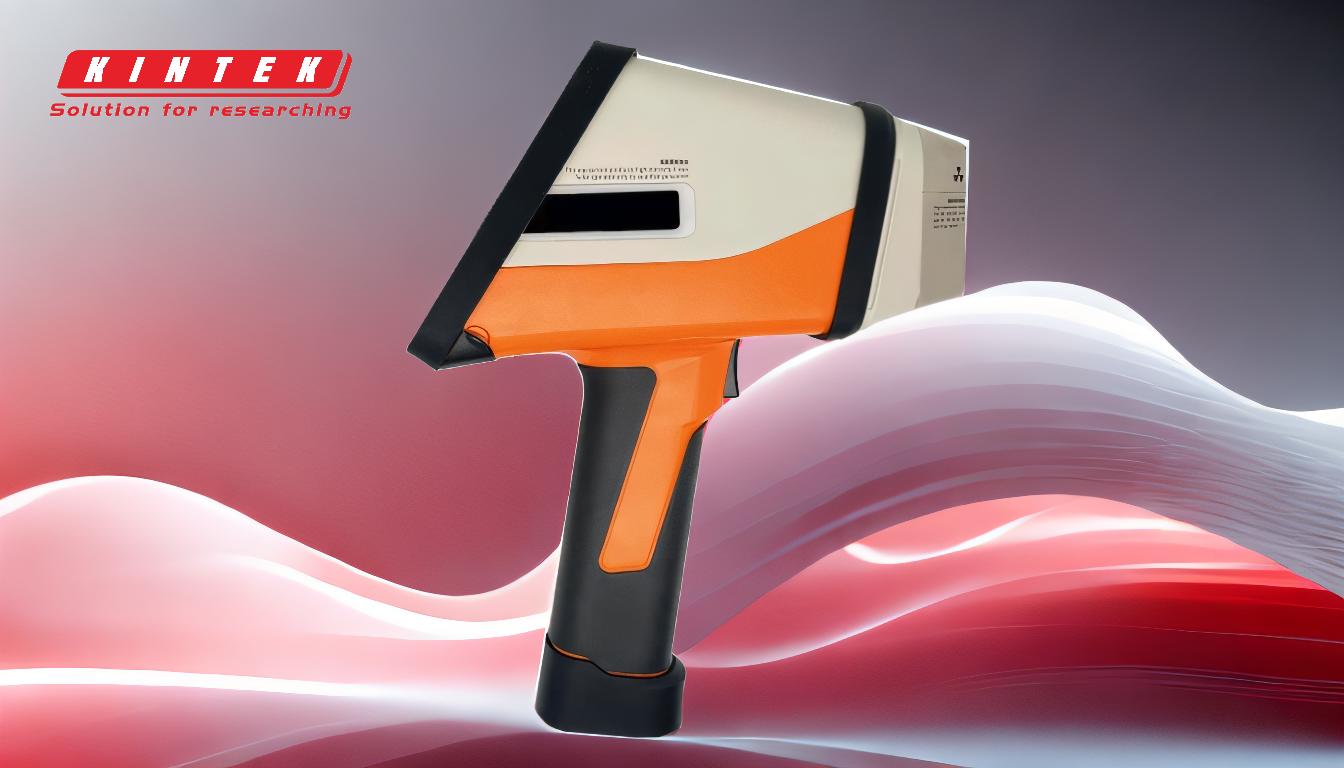
-
Definition of Dry Film Thickness (DFT):
- DFT is the thickness of a coating measured above the substrate after it has cured. It includes the total thickness of all applied layers, whether single or multiple.
- This measurement is distinct from wet film thickness, which is measured before the coating dries or cures.
-
Importance of DFT in Coating Applications:
- Quality Assurance: Proper DFT ensures that the coating provides the intended protection, such as corrosion resistance, UV protection, or aesthetic appeal.
- Cost Control: Accurate DFT measurement helps avoid over-application, which wastes material and increases costs, or under-application, which may lead to premature failure or rework.
- Compliance: Many industries have strict standards for coating thickness to meet regulatory or performance requirements. DFT measurement ensures compliance with these standards.
-
Measurement of DFT:
- DFT is measured on cured coatings at ambient temperature using tools such as magnetic gauges, ultrasonic thickness gauges, or destructive methods like cross-sectional analysis.
- The choice of measurement method depends on the substrate material, coating type, and application requirements.
-
Applications of DFT Measurement:
- Industrial Coatings: Used in machinery, pipelines, and structural steel to ensure durability and resistance to environmental factors.
- Automotive: Ensures paint and protective coatings meet thickness specifications for appearance and longevity.
- Construction: Critical for coatings on bridges, buildings, and other infrastructure to prevent corrosion and extend service life.
-
Challenges in DFT Measurement:
- Substrate Variability: Different substrates (e.g., metal, plastic, wood) require different measurement techniques.
- Coating Complexity: Multi-layer coatings or coatings with varying textures can complicate accurate measurement.
- Environmental Factors: Temperature, humidity, and surface conditions can affect both the application and measurement of coatings.
-
Best Practices for DFT Control:
- Pre-Application Planning: Define the required DFT range based on the coating system and application requirements.
- Regular Monitoring: Use appropriate tools to measure DFT during and after application to ensure consistency.
- Training: Ensure applicators and inspectors are trained in proper measurement techniques and understand the importance of DFT.
In summary, DFT coating thickness is a vital parameter in coating applications, ensuring quality, cost-effectiveness, and compliance with industry standards. Accurate measurement and control of DFT are essential for achieving optimal performance and longevity of coated products.
Summary Table:
Key Aspect | Details |
---|---|
Definition | Thickness of cured coating above the substrate, including all applied layers. |
Importance | Ensures quality, cost control, and compliance with industry standards. |
Measurement Tools | Magnetic gauges, ultrasonic gauges, or cross-sectional analysis. |
Applications | Industrial, automotive, and construction coatings. |
Challenges | Substrate variability, coating complexity, and environmental factors. |
Best Practices | Pre-application planning, regular monitoring, and proper training. |
Need help with DFT coating solutions? Contact our experts today for tailored advice and support!