An inert atmosphere is primarily used to create a controlled environment where reactive gases like oxygen are minimized or eliminated. This is crucial in applications such as heat treatment, where oxidation or contamination can degrade the quality of materials like steel. Inert gases like nitrogen and argon are commonly used to provide this protective environment. They prevent unwanted chemical reactions, reduce oxidation, and ensure the integrity of materials during processes such as bonding, curing, and heat-treating. Additionally, inert atmospheres are used in fields like engineering and food preservation to slow down degradation, reduce contamination, and enhance safety by minimizing fire and explosion risks.
Key Points Explained:
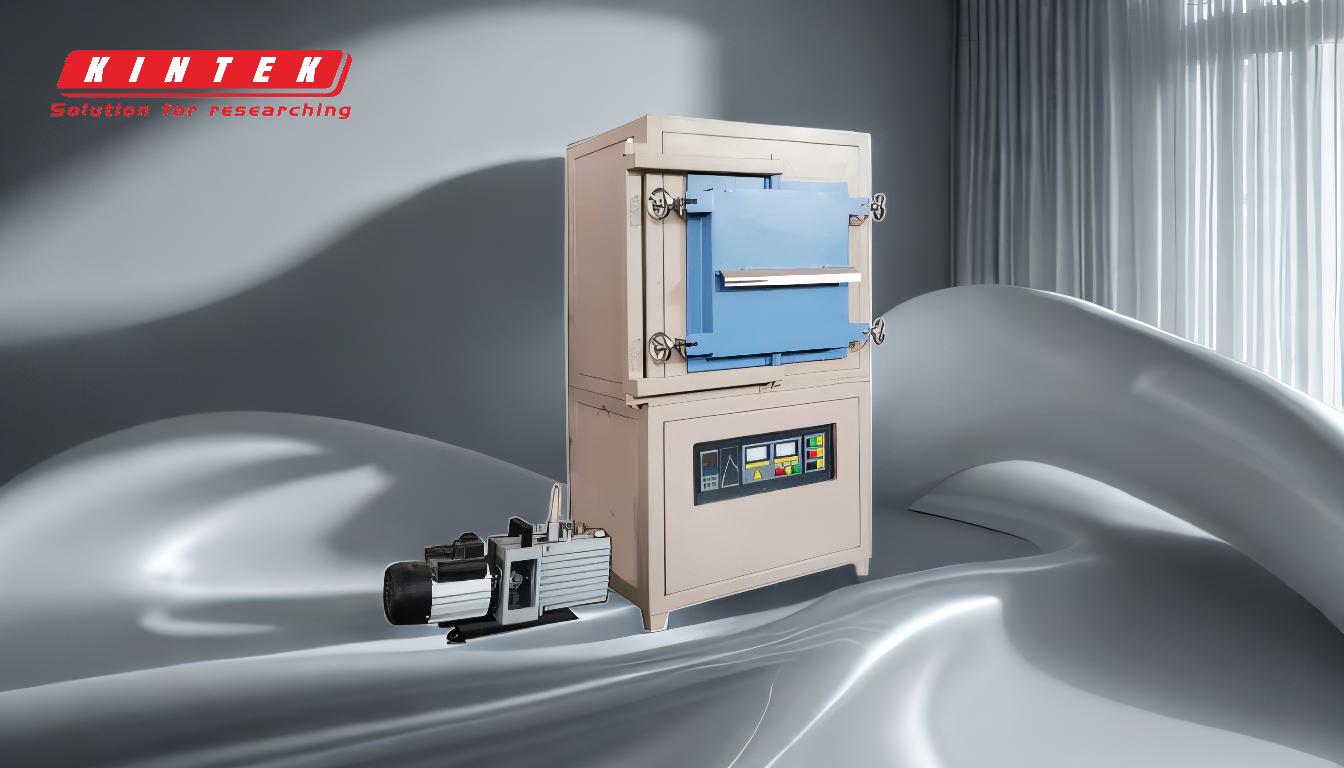
-
Prevention of Oxidation and Contamination:
- Inert atmospheres are used to protect materials from oxidation and contamination during heat treatment. Oxidation can degrade the quality of metals like steel, while contamination from reactive gases can alter their properties.
- By replacing the ambient air with inert gases like nitrogen or argon, the environment becomes unreactive, ensuring that materials retain their desired properties and structural integrity.
-
Common Applications:
- Heat Treatment: Inert atmospheres are widely used in furnaces for heat-treating metals. This ensures that the materials do not react with oxygen or other gases, maintaining their strength and durability.
- Bonding and Curing: Inert atmospheres are used in processes like adhesive bonding and curing, where exposure to oxygen or moisture could compromise the quality of the final product.
- Food Preservation: Inert gases are used to extend the shelf life of food products by slowing down oxidation and microbial growth.
-
Types of Inert Gases:
- Nitrogen: The most commonly used inert gas due to its availability and cost-effectiveness. It is non-reactive with most materials, making it ideal for creating a protective atmosphere.
- Argon: Another widely used inert gas, particularly in applications requiring higher purity or where nitrogen might not be suitable.
-
Equipment and Technology:
- Inert gas atmosphere furnaces are equipped with precision microprocessor-based temperature controls to ensure consistent and accurate heat treatment.
- Energy-efficient insulation is used to optimize cost savings and maintain high-quality performance.
-
Benefits of Inert Atmospheres:
- Reduced Reaction Rates: Slows down or prevents unwanted chemical reactions, ensuring the stability of materials.
- Oxidation Prevention: Protects materials from oxidation, which can weaken or degrade them.
- Contamination Control: Minimizes the risk of contamination from reactive gases or particles.
- Safety: Reduces the risk of fire and explosions, particularly in environments where flammable materials are present.
- Vacuum Creation: Inert atmospheres can be used to create a vacuum, which is essential in certain scientific and industrial processes.
-
Cross-Industry Applications:
- Engineering: Used in welding, metal fabrication, and semiconductor manufacturing to prevent oxidation and contamination.
- Food Industry: Extends the shelf life of perishable goods by replacing oxygen with inert gases in packaging.
- Scientific Research: Provides a controlled environment for experiments and processes that require the absence of reactive gases.
By understanding these key points, a purchaser of equipment or consumables can make informed decisions about the use of inert atmospheres in their specific applications, ensuring optimal performance and cost-effectiveness.
Summary Table:
Key Aspect | Details |
---|---|
Purpose | Minimize reactive gases like oxygen to protect materials and ensure safety. |
Common Gases | Nitrogen (cost-effective), Argon (high purity). |
Applications | Heat treatment, bonding, curing, food preservation, and scientific research. |
Benefits | Prevents oxidation, reduces contamination, enhances safety, and creates vacuum environments. |
Equipment | Precision-controlled furnaces with energy-efficient insulation. |
Learn how inert atmospheres can optimize your processes—contact our experts today!