The lifespan of a mold depends on several factors, including the material it is made from, the type of production process it is used in, the complexity of the part being molded, and the maintenance practices followed. Generally, molds can last anywhere from tens of thousands to millions of cycles, depending on these variables. High-quality molds made from durable materials like hardened steel can last significantly longer than those made from softer materials like aluminum. Proper maintenance, such as regular cleaning, lubrication, and timely repairs, also plays a crucial role in extending a mold's lifespan. Understanding these factors helps in making informed decisions about mold selection and maintenance.
Key Points Explained:
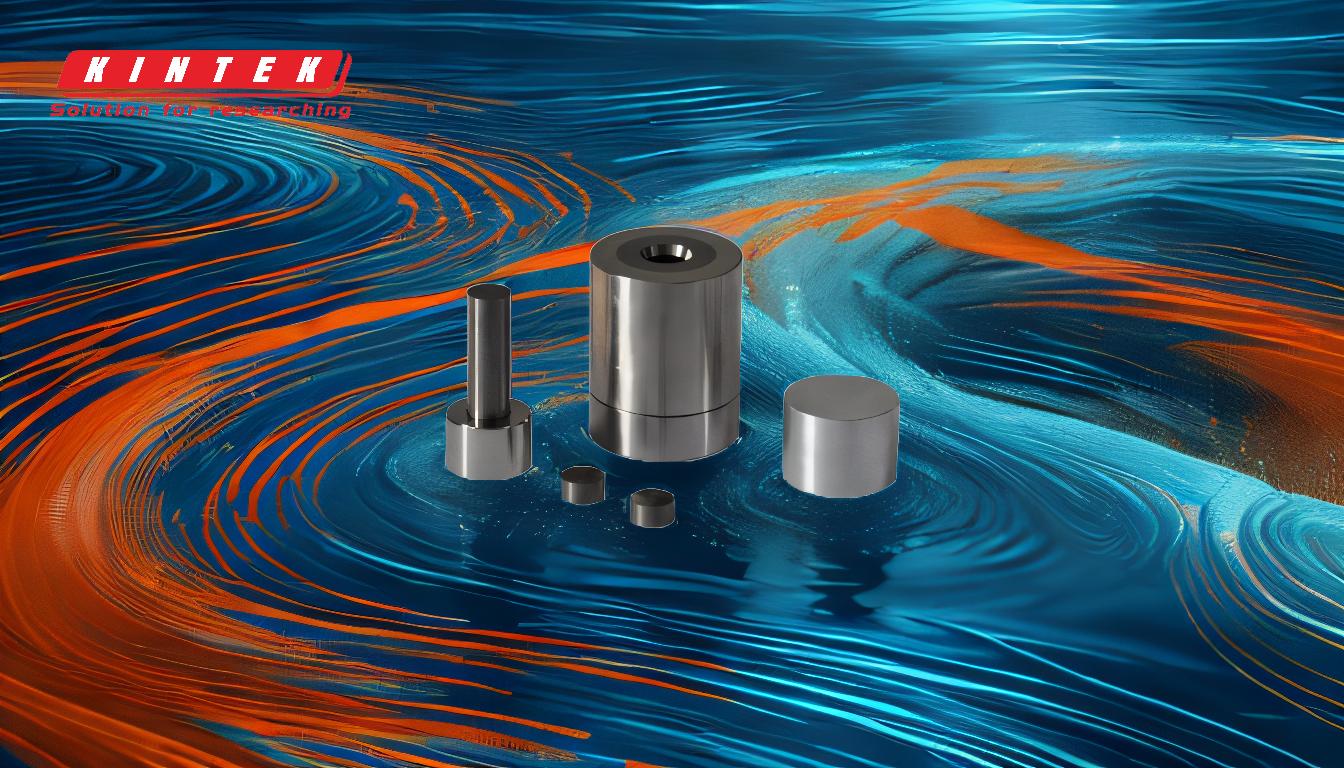
-
Material of the Mold:
- The material used to construct the mold is one of the most critical factors affecting its lifespan. Molds made from hardened steel are more durable and can withstand higher pressures and temperatures, making them suitable for high-volume production. These molds can last for millions of cycles.
- On the other hand, molds made from softer materials like aluminum are less expensive and easier to machine but have a shorter lifespan, typically lasting for tens of thousands of cycles. Aluminum molds are often used for prototyping or low-volume production.
-
Type of Production Process:
- The production process also significantly impacts the lifespan of a mold. Injection molding, for example, involves high pressures and temperatures, which can wear down the mold over time. The complexity of the part being molded also plays a role; intricate designs with thin walls or fine details can cause more stress on the mold, leading to faster wear and tear.
- Blow molding and rotational molding are generally less stressful on molds compared to injection molding, potentially extending the mold's lifespan.
-
Maintenance Practices:
- Regular maintenance is essential for prolonging the life of a mold. This includes cleaning the mold after each production run to remove any residual material, lubricating moving parts to reduce friction, and inspecting the mold for signs of wear or damage.
- Timely repairs are crucial; addressing minor issues before they become major problems can significantly extend the mold's lifespan. Neglecting maintenance can lead to premature failure, requiring costly repairs or replacement.
-
Production Volume:
- The number of cycles a mold undergoes directly affects its lifespan. High-volume production runs put more stress on the mold, leading to faster wear and tear. Conversely, molds used in low-volume production or for prototyping may last longer due to fewer cycles.
- It's important to match the mold's material and design with the expected production volume to ensure optimal performance and longevity.
-
Environmental Factors:
- The operating environment can also impact the lifespan of a mold. Factors such as humidity, temperature fluctuations, and exposure to corrosive materials can accelerate wear and corrosion. Using molds in controlled environments and applying protective coatings can help mitigate these effects.
-
Design and Complexity:
- The design of the mold and the complexity of the part being produced can influence its lifespan. Molds with simple designs and fewer moving parts are generally more durable and easier to maintain.
- Complex molds with intricate details, undercuts, or thin walls are more prone to wear and may require more frequent maintenance and repairs.
-
Quality of Manufacturing:
- The quality of the mold's manufacturing process also plays a role in its lifespan. Precision machining, proper heat treatment, and high-quality materials contribute to a longer-lasting mold.
- Poorly manufactured molds may have defects or inconsistencies that lead to premature failure.
By considering these factors, manufacturers can make informed decisions about mold selection, maintenance, and replacement, ultimately optimizing production efficiency and reducing costs.
Summary Table:
Factor | Impact on Mold Lifespan |
---|---|
Material | Hardened steel molds last millions of cycles; aluminum molds last tens of thousands. |
Production Process | Injection molding is more stressful; blow/rotational molding extends lifespan. |
Maintenance | Regular cleaning, lubrication, and timely repairs significantly extend lifespan. |
Production Volume | High-volume production accelerates wear; low-volume molds last longer. |
Environmental Factors | Humidity, temperature, and corrosive materials can reduce lifespan. |
Design and Complexity | Simple designs last longer; complex molds require more maintenance. |
Quality of Manufacturing | Precision machining and high-quality materials ensure longer-lasting molds. |
Maximize your mold's lifespan with expert guidance—contact us today for tailored solutions!