Mold filling analysis is a critical process in the injection molding industry, where sophisticated computer programs are used to simulate and predict the flow and cooling of molten plastic during the injection molding process. This analysis helps manufacturers optimize mold design, improve product quality, and reduce production costs by identifying potential issues such as air traps, weld lines, and uneven cooling before the mold is manufactured. By simulating the entire injection molding process, mold filling analysis ensures that the plastic material fills the mold cavity uniformly and solidifies correctly, leading to high-quality finished products.
Key Points Explained:
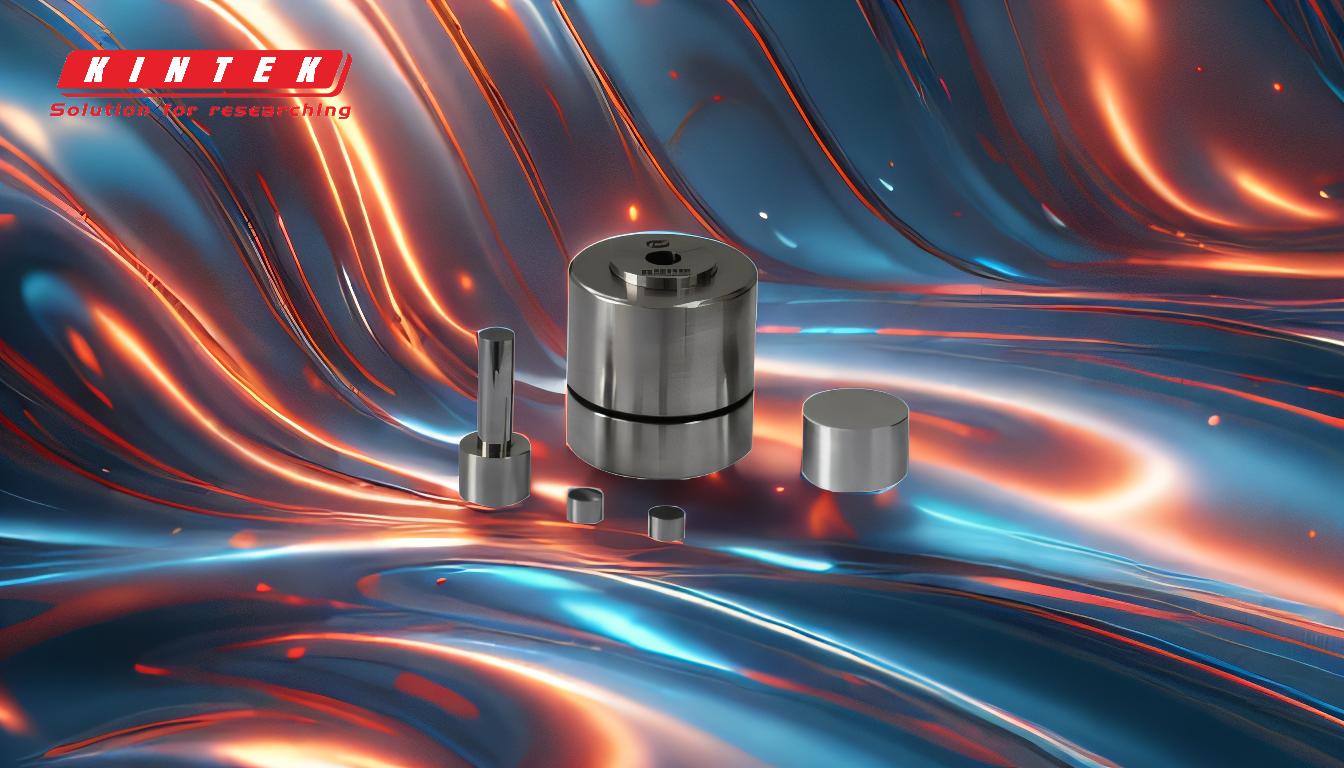
-
Definition of Mold Filling Analysis:
- Mold filling analysis is a simulation technique used in the injection molding industry to predict how molten plastic will flow and cool within a mold cavity.
- It involves the use of advanced computer software to model the injection molding process, including the filling, packing, and cooling phases.
-
Purpose and Importance:
- Optimization of Mold Design: By simulating the injection molding process, manufacturers can identify and address potential design flaws in the mold before it is manufactured. This reduces the risk of defects in the final product.
- Improvement of Product Quality: Mold filling analysis helps ensure that the plastic material fills the mold cavity uniformly, minimizing issues such as air traps, weld lines, and sink marks.
- Cost Reduction: By identifying potential problems early in the design phase, manufacturers can avoid costly mold modifications and production delays.
-
Key Phases in Mold Filling Analysis:
- Filling Phase: This phase simulates how the molten plastic flows into the mold cavity. The software predicts the flow front, pressure distribution, and potential flow-related defects.
- Packing Phase: After the mold cavity is filled, the packing phase ensures that additional material is injected to compensate for shrinkage as the plastic cools and solidifies.
- Cooling Phase: The cooling phase simulates how the plastic solidifies and cools within the mold. Proper cooling is essential to prevent warping and ensure dimensional stability of the final product.
-
Benefits of Mold Filling Analysis:
- Early Detection of Defects: The analysis can identify potential defects such as air traps, weld lines, and short shots before the mold is manufactured.
- Improved Material Utilization: By optimizing the flow and cooling of the plastic, manufacturers can reduce material waste and improve the efficiency of the injection molding process.
- Enhanced Product Performance: Uniform filling and cooling lead to better mechanical properties and overall performance of the final product.
-
Software Used in Mold Filling Analysis:
- Various software tools are available for mold filling analysis, including Autodesk Moldflow, SOLIDWORKS Plastics, and Moldex3D. These tools use finite element analysis (FEA) and computational fluid dynamics (CFD) to simulate the injection molding process accurately.
-
Considerations for Purchasers:
- When purchasing equipment or consumables for injection molding, it is essential to consider the compatibility of the materials with mold filling analysis software. This ensures that the simulation results are accurate and reliable.
- Purchasers should also evaluate the software's ability to integrate with their existing design and manufacturing processes, as well as the level of technical support provided by the software vendor.
In conclusion, mold filling analysis is an indispensable tool in the injection molding industry, enabling manufacturers to optimize mold design, improve product quality, and reduce production costs. By simulating the entire injection molding process, this analysis ensures that the plastic material fills the mold cavity uniformly and solidifies correctly, leading to high-quality finished products.
Summary Table:
Aspect | Details |
---|---|
Definition | Simulation technique to predict molten plastic flow and cooling in molds. |
Purpose | Optimize mold design, improve product quality, and reduce production costs. |
Key Phases | Filling, packing, and cooling phases. |
Benefits | Early defect detection, improved material use, enhanced product performance. |
Software Tools | Autodesk Moldflow, SOLIDWORKS Plastics, Moldex3D. |
Purchaser Considerations | Material compatibility, software integration, and technical support. |
Ready to optimize your injection molding process? Contact us today for expert guidance and solutions!