Plasma Chemical Vapor Deposition (PCVD) is a specialized form of chemical vapor deposition that utilizes plasma to enhance the chemical reactions required for depositing thin films or coatings onto substrates. Unlike traditional CVD, which relies on thermal energy to drive the reactions, PCVD employs plasma—a highly energized state of matter consisting of ions, electrons, and neutral particles—to achieve the same goal. This method is particularly advantageous for depositing high-quality thin films at lower temperatures, making it suitable for temperature-sensitive materials. PCVD is widely used in industries such as semiconductors, optics, and energy storage, where precision and material integrity are critical.
Key Points Explained:
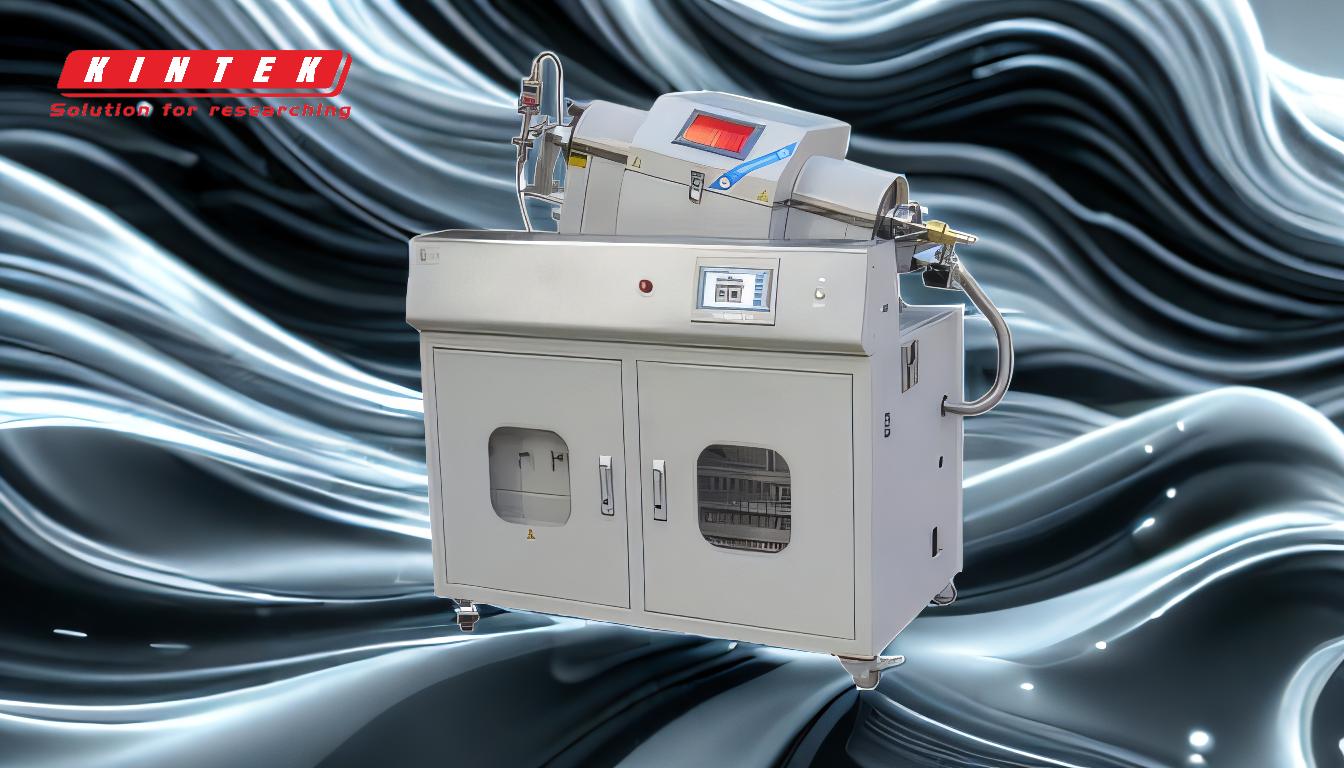
-
Definition and Mechanism of Plasma Chemical Vapor Deposition (PCVD):
- PCVD is a variant of chemical vapor deposition that uses plasma to activate and sustain the chemical reactions necessary for thin film deposition.
- Plasma is generated by applying an electric field to a gas, which ionizes the gas and creates a highly reactive environment. This plasma enhances the reactivity of the precursor gases, allowing for deposition at lower temperatures compared to thermal CVD.
-
Advantages of PCVD Over Traditional CVD:
- Lower Temperature Operation: PCVD enables thin film deposition at significantly lower temperatures, which is beneficial for temperature-sensitive substrates.
- Enhanced Film Quality: The use of plasma results in better control over film properties such as density, uniformity, and adhesion.
- Versatility: PCVD can deposit a wide range of materials, including metals, ceramics, and semiconductors, making it suitable for diverse applications.
-
Applications of PCVD:
- Semiconductor Industry: PCVD is used to deposit thin films of silicon dioxide, silicon nitride, and other materials critical for semiconductor device fabrication.
- Optical Coatings: It is employed to create anti-reflective, protective, and functional coatings on lenses and mirrors.
- Energy Storage: PCVD is used in the production of thin-film batteries and supercapacitors, where precise control over film properties is essential.
-
Types of PCVD Systems:
- Low-Pressure PCVD: Operates under reduced pressure to minimize contamination and improve film uniformity.
- Atmospheric Pressure PCVD: Suitable for large-scale industrial applications where vacuum systems are impractical.
- Remote Plasma CVD: Separates the plasma generation region from the deposition zone, reducing damage to the substrate.
-
Challenges and Considerations:
- Complexity: PCVD systems are more complex than traditional CVD systems, requiring precise control over plasma parameters such as power, pressure, and gas flow.
- Cost: The equipment and operational costs for PCVD are generally higher due to the need for plasma generation and control systems.
- Material Compatibility: Not all materials are suitable for PCVD, as the plasma environment can sometimes cause damage or unwanted reactions.
-
Future Trends in PCVD:
- Integration with Other Technologies: Combining PCVD with other deposition techniques, such as atomic layer deposition (ALD), to achieve even greater control over film properties.
- Development of New Precursors: Research into new precursor materials that can be efficiently activated by plasma, expanding the range of materials that can be deposited.
- Sustainability: Efforts to reduce the environmental impact of PCVD processes by using greener precursors and optimizing energy consumption.
In summary, Plasma Chemical Vapor Deposition is a powerful and versatile technique for depositing high-quality thin films and coatings. Its ability to operate at lower temperatures and produce superior film properties makes it indispensable in many high-tech industries. However, the complexity and cost of PCVD systems require careful consideration when selecting this method for specific applications.
Summary Table:
Aspect | Details |
---|---|
Definition | PCVD uses plasma to deposit thin films at lower temperatures. |
Advantages | Lower temperature operation, enhanced film quality, and material versatility. |
Applications | Semiconductors, optical coatings, and energy storage. |
Types of PCVD Systems | Low-pressure, atmospheric pressure, and remote plasma CVD. |
Challenges | Complexity, higher costs, and material compatibility issues. |
Future Trends | Integration with ALD, new precursors, and sustainability improvements. |
Interested in leveraging PCVD for your projects? Contact our experts today to learn more!