Plasma nitriding is a surface hardening process used to enhance the wear resistance, fatigue strength, and corrosion resistance of metal components. It involves the use of a plasma discharge to introduce nitrogen into the surface of the material, forming a hard nitride layer. This process is particularly advantageous for its ability to operate at lower temperatures, minimizing distortion and maintaining the core strength of the material. It is suitable for a wide range of ferrous and non-ferrous materials, making it a versatile choice for various industrial applications.
Key Points Explained:
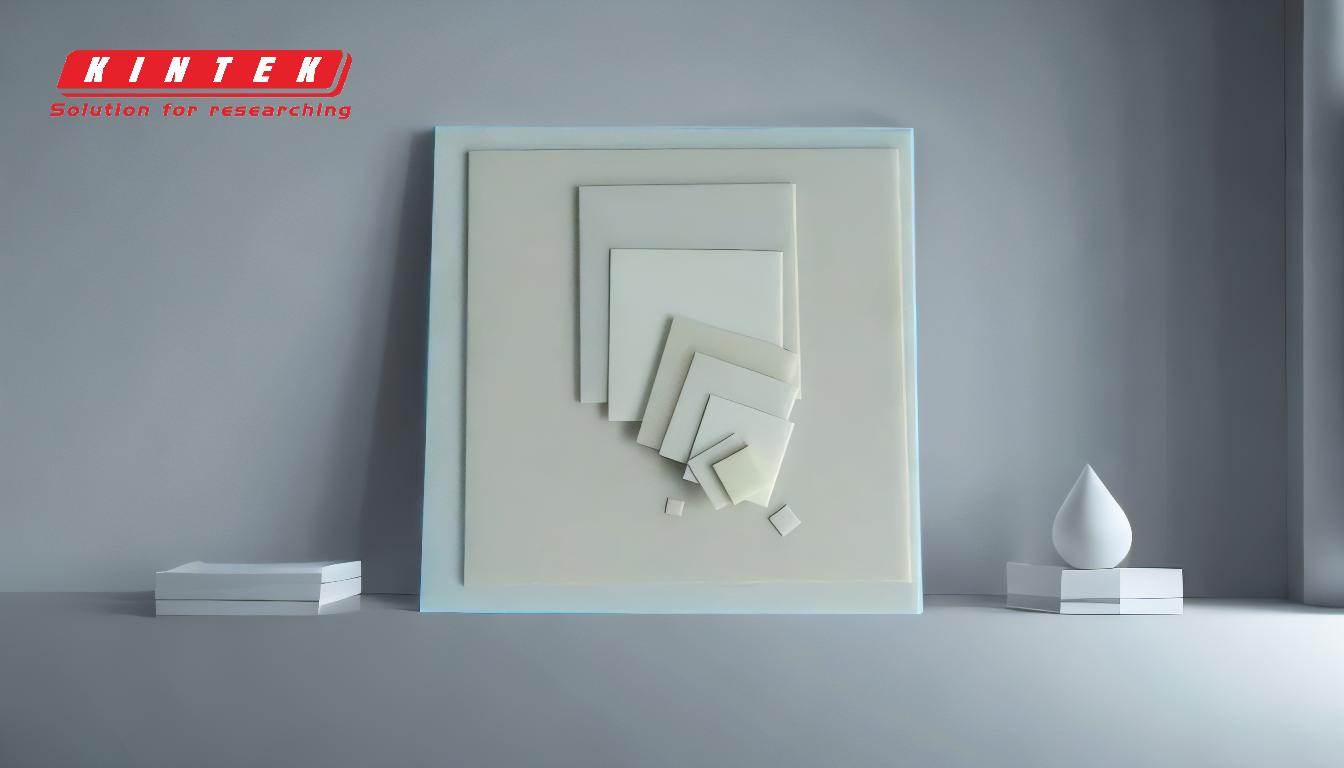
-
Process Overview:
- Plasma nitriding is a thermochemical process that uses a plasma discharge to introduce nitrogen into the surface of a material.
- The process typically involves placing the workpiece in a vacuum chamber, where a plasma is generated by applying a high voltage between the workpiece (cathode) and the chamber wall (anode).
- Nitrogen ions from the plasma are accelerated towards the workpiece, where they penetrate the surface and form a hard nitride layer.
-
Temperature Control:
- Temperature is a critical factor in plasma nitriding, as it directly affects the kinetics of the nitriding process.
- The process can be carried out at relatively low temperatures (up to 350°C), which is particularly beneficial for materials that require precise dimensional stability.
- Low-temperature nitriding minimizes distortion and maintains the high core strength of low-temperature hardened steel.
-
Advantages of Plasma Nitriding:
- Speed: Plasma nitriding is much faster than conventional nitriding techniques, reducing processing time.
- Control: Proper control of temperature, atmosphere composition, and discharge parameters allows for excellent microstructure and better control of the final product’s surface composition, structure, and properties.
- Environmental Impact: The process is environmentally harmless, as it does not produce harmful by-products.
- Versatility: It can be applied to a wide range of materials, including ferrous materials, sintered steels, cast iron, high-alloy tool steels, stainless steels, nickel-based alloys, titanium, and aluminum alloys.
-
Applications:
- Plasma nitriding is used in a variety of industrial applications, including gears, crankshafts, camshafts, cam lifters, valve parts, extruder screws, die casting tools, forging dies, cold forming tools, injectors, plastic forming tools, long shafts, axles, couplings, and engine parts.
- The process is particularly beneficial for components that require high wear resistance, fatigue strength, and corrosion resistance.
-
Comparison with Gas Nitriding:
- Gas nitriding involves placing the workpiece in a sealed space and introducing ammonia gas, which is then heated to 500-580°C for several to dozens of hours.
- At temperatures above 400°C, ammonia decomposes into hydrogen and reactive nitrogen atoms, which are absorbed by the steel surface and diffuse internally to form a nitride layer.
- Plasma nitriding, on the other hand, operates at lower temperatures and offers better control over the process parameters, resulting in a more uniform and controlled nitride layer.
-
Material Compatibility:
- Plasma nitriding is suitable for all ferrous materials, sintered steels, cast iron, high-alloy tool steels, stainless steels, nickel-based alloys, titanium, and aluminum alloys.
- This wide range of material compatibility makes plasma nitriding a versatile choice for various industrial applications.
In summary, plasma nitriding is a highly effective surface hardening process that offers numerous advantages over conventional nitriding techniques. Its ability to operate at lower temperatures, combined with excellent control over process parameters, makes it a preferred choice for enhancing the performance and longevity of critical components in various industries.
Summary Table:
Aspect | Details |
---|---|
Process | Uses plasma discharge to introduce nitrogen into the material surface. |
Temperature Range | Operates at low temperatures (up to 350°C), minimizing distortion. |
Advantages | Faster than conventional methods, precise control, eco-friendly, versatile. |
Applications | Gears, crankshafts, camshafts, engine parts, and more. |
Material Compatibility | Ferrous and non-ferrous materials, including stainless steel and titanium. |
Learn how plasma nitriding can improve your components' performance—contact our experts today!