Powder sintering is a manufacturing process where powdered materials are compacted and heated to a temperature below their melting point, causing the particles to bond and form a solid mass. This process leverages diffusion mechanisms such as surface diffusion, viscous flow, evaporative coalescence, bulk diffusion, and grain boundary diffusion to fuse particles together. It is particularly useful for materials with high melting points, such as tungsten and molybdenum. The process involves stages like powder compacting, heating, and forming, which result in materials with improved density, strength, and mechanical properties. Sintering is widely used in industries to produce components with tight tolerances and specific material characteristics.
Key Points Explained:
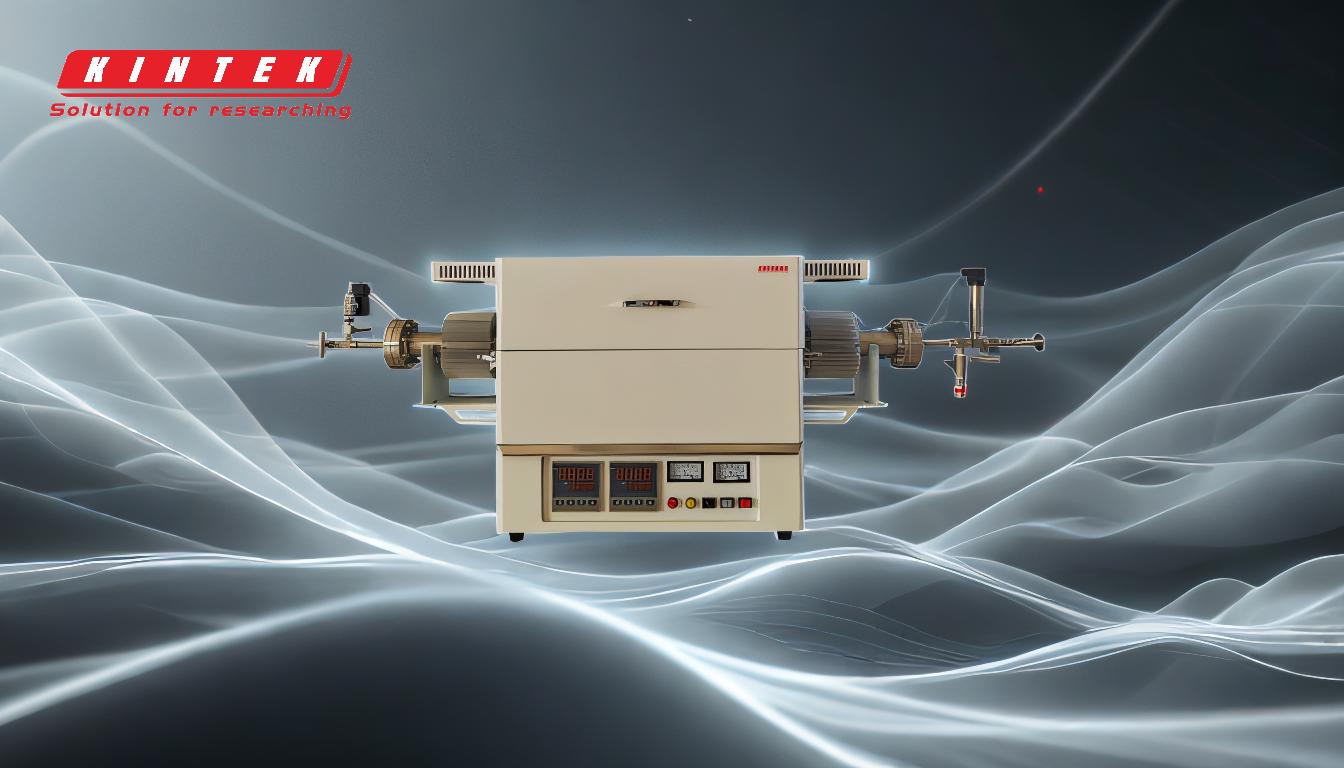
-
Definition of Powder Sintering:
- Powder sintering is a process that compacts and forms a solid mass of material by applying heat or pressure without melting the material to the point of liquefaction. This allows the atoms in the particles to diffuse across boundaries, fusing them into a single solid piece.
-
Mechanisms of Sintering:
- The sintering process involves several diffusion mechanisms:
- Surface Diffusion: Atoms move along the surface of particles.
- Viscous Flow: Particles deform and flow under heat and pressure.
- Evaporative Coalescence: Material evaporates and re-condenses to join particles.
- Bulk Diffusion: Atoms migrate through the interior of particles.
- Grain Boundary Diffusion: Atoms move along the boundaries between particles.
- These mechanisms collectively reduce surface energy and close pores, leading to denser and stronger materials.
- The sintering process involves several diffusion mechanisms:
-
Stages of Powder Sintering:
- Powder Compacting: The initial stage involves mechanical densification through cold or hot pressing to create a "green part." This stage ensures tight tolerances and low drying shrinkage.
- Heating: The material is heated in a furnace at a temperature below its melting point. This induces particle bonding through diffusion mechanisms without complete melting.
- Forming: The homogeneous mixture is placed into a press mold to create a billet with specific shape, size, and density.
-
Applications and Materials:
- Sintering is particularly useful for materials with extremely high melting points, such as tungsten and molybdenum. It is also used for ceramics, where a slurry of water, deflocculant, binder, and ceramic powder is spray-dried before sintering.
- The process is widely used in industries to produce components with precise dimensions and enhanced mechanical properties.
-
Benefits of Sintering:
- Improved Density: The reduction of pores during sintering results in higher-density materials.
- Enhanced Mechanical Properties: Sintered materials exhibit improved strength, hardness, and temperature conductivity.
- Tight Tolerances: The process allows for the production of components with precise dimensions and low shrinkage.
-
Challenges and Considerations:
- The sintering temperature must be carefully controlled to avoid melting the material while ensuring sufficient particle bonding.
- The properties of the powdered materials, such as particle size and composition, significantly influence the final characteristics of the sintered part.
By understanding these key points, equipment and consumable purchasers can make informed decisions about the sintering process and its applications in their industries.
Summary Table:
Aspect | Details |
---|---|
Definition | Compacts and heats powdered materials below melting point to form solid mass. |
Mechanisms | Surface diffusion, viscous flow, evaporative coalescence, bulk diffusion, grain boundary diffusion. |
Stages | Powder compacting, heating, forming. |
Applications | Used for high-melting-point materials like tungsten, molybdenum, and ceramics. |
Benefits | Improved density, enhanced mechanical properties, tight tolerances. |
Challenges | Precise temperature control and material properties influence final outcomes. |
Discover how powder sintering can optimize your material production—contact our experts today!