Pyrolysis of lignocellulosic materials is a thermochemical process that involves heating biomass, such as wood, agricultural residues, or other plant-based materials, in the absence of oxygen. This process breaks down the complex organic polymers in lignocellulosic biomass into simpler molecules, producing bio-oil, biochar, and syngas. These products have diverse applications, including renewable energy generation, soil amendment, and chemical production. Pyrolysis has a rich historical background, dating back to ancient civilizations, and has evolved into a modern technology with significant potential for sustainable energy solutions. The process is efficient, environmentally friendly, and adaptable to both small-scale and large-scale applications.
Key Points Explained:
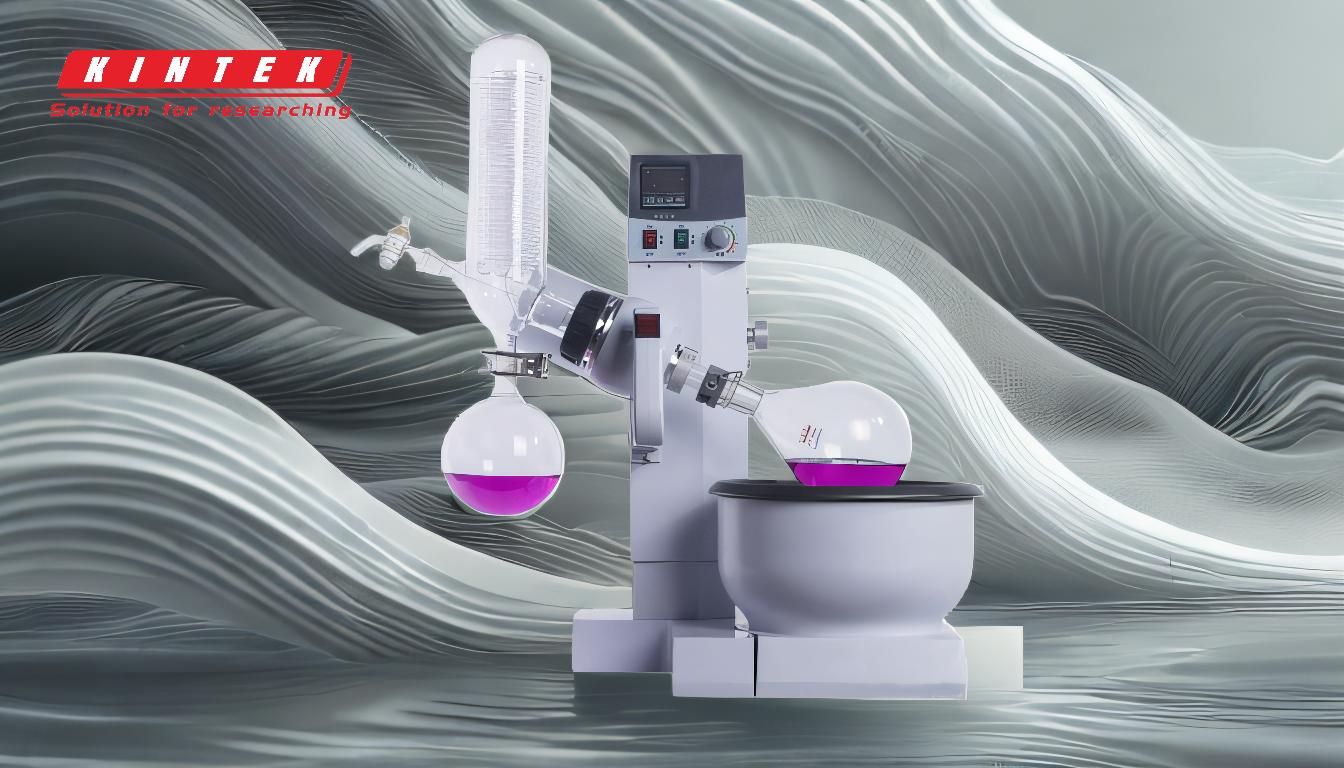
-
Definition of Pyrolysis of Lignocellulosic Materials:
- Pyrolysis is a thermochemical decomposition process that occurs when lignocellulosic biomass is heated to high temperatures (typically 500°C–700°C) in the absence of oxygen.
- Lignocellulosic biomass includes materials like wood, agricultural residues (e.g., straw, husks), and other plant-based organic matter.
- The process breaks down the complex polymers (cellulose, hemicellulose, and lignin) in the biomass into simpler compounds, yielding three main products: bio-oil, biochar, and syngas.
-
Historical Context of Pyrolysis:
- Pyrolysis has been used for thousands of years, with early applications including the production of charcoal from wood.
- Ancient Egyptians utilized pyrolysis-derived products, such as tars and pyroligneous acid, for embalming and boat caulking.
- During the 1800s, wood pyrolysis was a major industry, producing charcoal as a primary fuel source for the industrial revolution until coal became more prevalent.
- This historical use highlights the long-standing importance of pyrolysis in converting organic materials into valuable products.
-
Mechanism of Pyrolysis:
- The process begins with feeding lignocellulosic biomass into a reactor, where it is rapidly heated in an oxygen-free environment.
- The heat causes the biomass to decompose into three primary components:
- Pyrolysis Vapor: Condenses into bio-oil upon cooling.
- Syngas: A mixture of hydrogen, carbon monoxide, and other gases.
- Biochar: A solid residue rich in carbon.
- The absence of oxygen prevents combustion, ensuring that the biomass decomposes rather than burns.
-
Products of Pyrolysis and Their Applications:
- Bio-oil: A liquid product that can be refined into transportation fuels or used directly for heating and electricity generation.
- Biochar: A solid product used as a soil amendment to improve fertility and sequester carbon, reducing greenhouse gas emissions.
- Syngas: A gaseous product that can be combusted to generate heat and electricity or further processed into chemicals and fuels.
- These products make pyrolysis a versatile process for renewable energy and sustainable resource utilization.
-
Environmental and Economic Benefits:
- Pyrolysis offers a renewable alternative to fossil fuels, reducing dependence on non-renewable energy sources.
- It contributes to mitigating climate change by converting biomass waste into useful products and reducing greenhouse gas emissions.
- The process is scalable, making it suitable for both rural energy solutions and large-scale industrial applications.
- By valorizing agricultural and forestry waste, pyrolysis supports circular economy principles and reduces waste disposal challenges.
-
Modern Applications and Future Potential:
- Pyrolysis is increasingly used in modern renewable energy systems to produce biofuels and biochemicals.
- It has the potential to replace fossil hydrocarbons in boilers, engines, and chemical production processes.
- Advances in pyrolysis technology are improving efficiency, product yields, and environmental performance, making it a key player in the transition to a low-carbon economy.
-
Challenges and Considerations:
- The process requires careful control of temperature, heating rate, and residence time to optimize product yields and quality.
- Feedstock variability (e.g., moisture content, composition) can affect the efficiency and outcomes of pyrolysis.
- Economic viability depends on factors such as feedstock availability, market demand for pyrolysis products, and technological advancements.
In summary, pyrolysis of lignocellulosic materials is a transformative process with deep historical roots and significant modern applications. It converts biomass into valuable energy and chemical products, offering a sustainable solution to global energy and environmental challenges.
Summary Table:
Aspect | Details |
---|---|
Definition | Thermochemical decomposition of biomass in the absence of oxygen. |
Key Products | Bio-oil, biochar, and syngas. |
Applications | Renewable energy, soil amendment, chemical production. |
Environmental Benefits | Reduces greenhouse gas emissions and supports circular economy principles. |
Challenges | Feedstock variability, process optimization, and economic viability. |
Discover how pyrolysis can transform your energy solutions—contact us today!