Sintering of metallic powders is a critical heat treatment process in powder metallurgy where metal particles are heated to just below their melting point, allowing them to fuse together while retaining their beneficial properties. This process involves several key steps, including selecting the appropriate metal powder composition, compacting the powder into the desired shape, and sintering the compacted powder in a controlled environment to achieve structural integrity and optimal material properties. The sintering process can be compared to ice cubes fusing at their contact points before melting, as it involves bonding particles through heat without fully liquefying the material. This method is widely used to create high-strength, durable metal components with precise shapes and properties.
Key Points Explained:
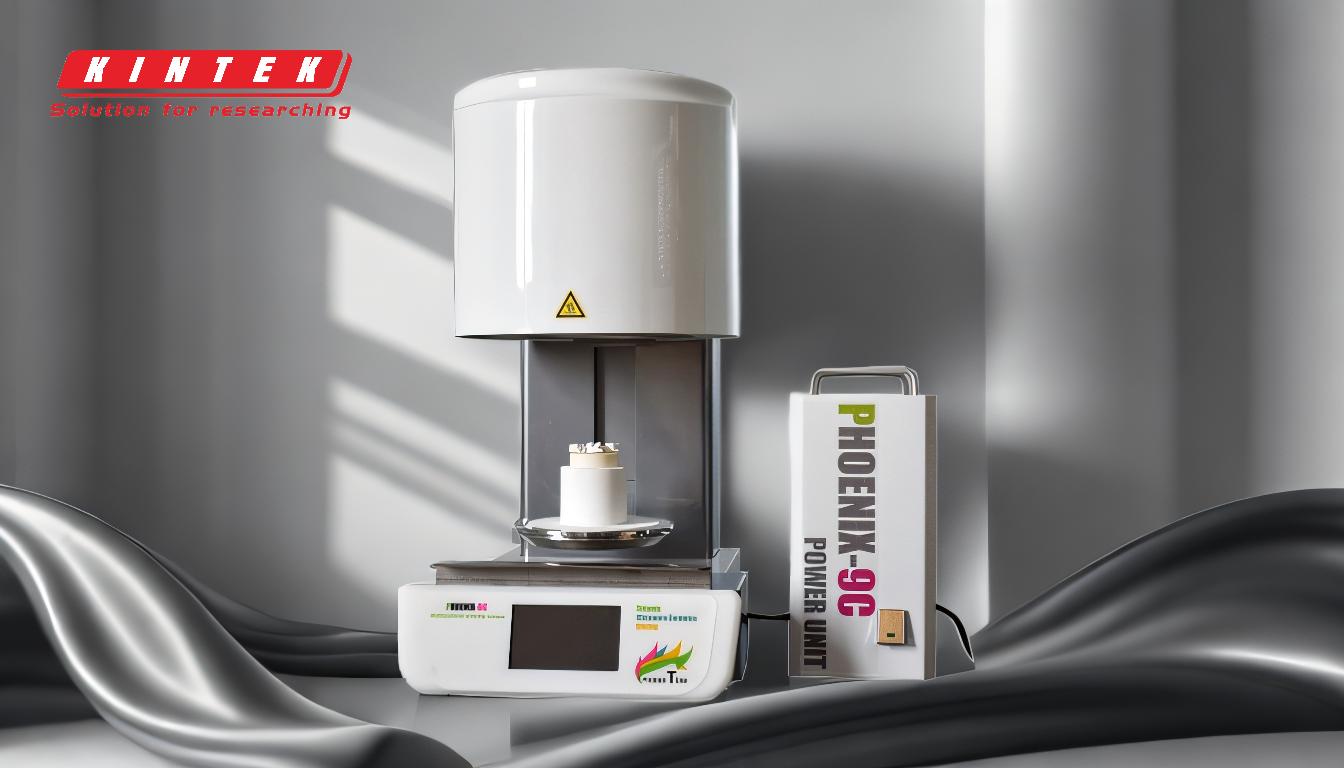
-
Definition and Purpose of Sintering:
- Sintering is a heat treatment process used in powder metallurgy to fuse metal particles together without melting them completely.
- The primary purpose is to create a solid, dense, and structurally sound metal part with improved mechanical properties, such as strength and hardness.
-
Stages of the Sintering Process:
- Powder Selection: The process begins with selecting the appropriate metal powder composition, which determines the final properties of the sintered product. Common metals include iron, nickel, molybdenum, and copper, often mixed with lubricants or additives.
- Compaction: The selected powder is pressed into the desired shape using a die press under high pressure. This forms a "green" part with initial strength but limited structural integrity.
- Sintering: The green part is heated in a sintering furnace to a temperature just below the melting point of the metal. This causes the particles to bond together, reducing porosity and increasing density, resulting in a solid and durable component.
-
Key Steps in the Sintering Operation:
- Cloth and Material Preparation: Laying the base material and mixing components on the sintering machine.
- Ignition: Igniting the surface of the material and maintaining a high temperature to initiate the bonding process.
- Sintering Control: Precise control of parameters such as air volume, vacuum, layer thickness, speed, and sintering endpoint to ensure optimal bonding and material properties.
-
Mechanisms of Sintering:
- Solid-State Sintering: Particles bond through diffusion and grain growth at temperatures below the melting point. This is common in processes involving iron and other metals.
- Liquid-State Sintering: At least one material is in a liquid state, which flows into pores and enhances bonding. This is used for materials like tungsten carbide and cemented carbide.
-
Post-Sintering Treatments:
- After sintering, additional treatments such as cooling, machining, or surface finishing may be applied to achieve the desired final properties and dimensions.
-
Applications and Benefits:
- Sintering is widely used in industries such as automotive, aerospace, and electronics to produce complex, high-strength components with precise shapes.
- The process offers benefits such as material efficiency, cost-effectiveness, and the ability to create parts with tailored properties.
By understanding these key points, a purchaser of equipment or consumables for sintering can make informed decisions about the materials, processes, and machinery required to achieve high-quality sintered metal products.
Summary Table:
Key Aspect | Description |
---|---|
Definition | Heat treatment process to fuse metal particles without melting them completely. |
Stages | Powder selection, compaction, and sintering in a controlled environment. |
Mechanisms | Solid-state sintering (diffusion) and liquid-state sintering (bonding). |
Applications | Automotive, aerospace, and electronics industries. |
Benefits | Material efficiency, cost-effectiveness, and tailored properties. |
Ready to enhance your metal component production? Contact us today to learn more about sintering solutions!