Sputter-coated glass refers to glass that has undergone a sputter coating process, where a thin film of material is deposited onto the glass surface using a technique called sputtering. This process involves bombarding a target material with high-energy ions in a vacuum chamber, causing atoms to be ejected and deposited onto the glass substrate. Sputter coating is widely used in various industries, including optics, electronics, and architecture, to enhance the glass's properties, such as reflectivity, conductivity, or durability. The resulting coatings can be functional (e.g., anti-reflective, conductive) or decorative, depending on the application.
Key Points Explained:
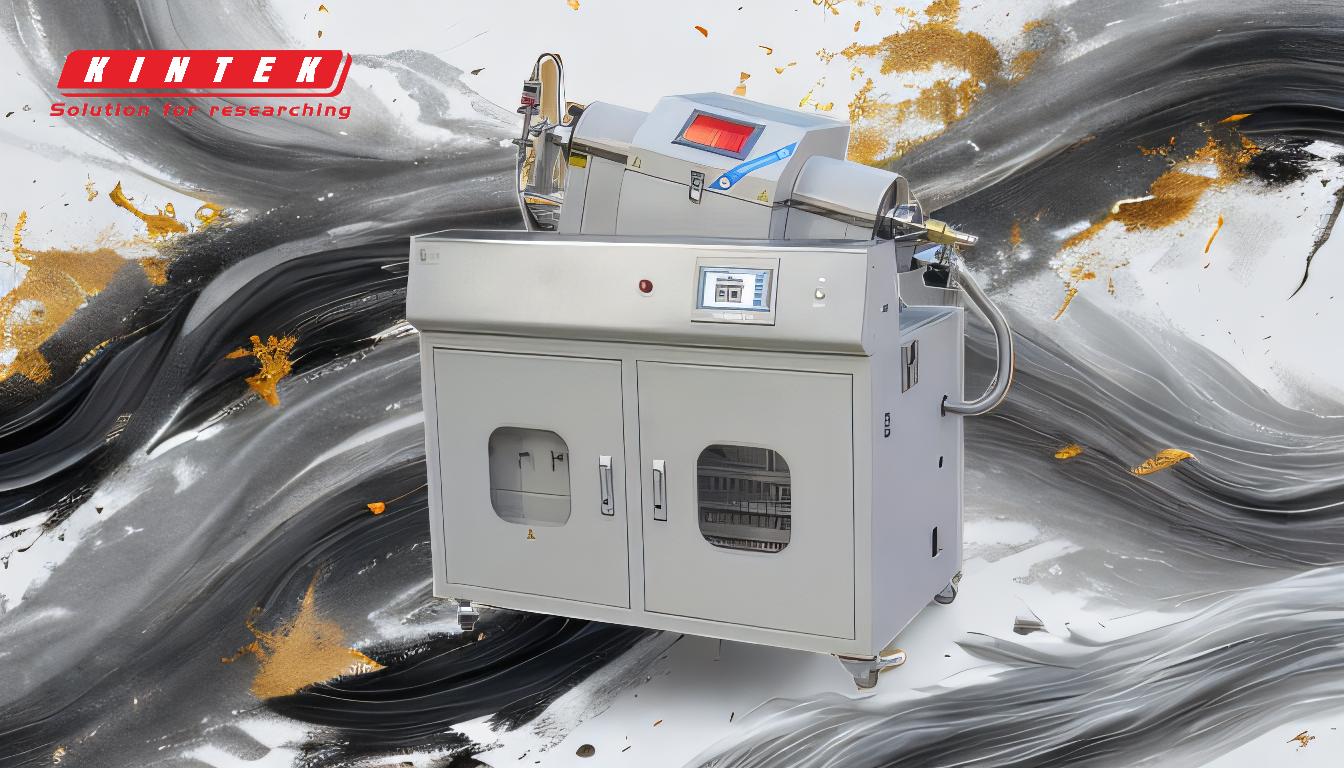
-
What is Sputter Coating?
- Sputter coating is a physical vapor deposition (PVD) process where atoms from a solid target material are ejected into a gas phase due to bombardment by high-energy ions. These atoms are then deposited onto a substrate, such as glass, forming a thin, uniform film.
- The process occurs in a vacuum chamber, often using inert gases like argon to facilitate the sputtering.
-
How Does Sputter Coating Work?
- A target material (e.g., metal, oxide) is placed in a vacuum chamber and bombarded with high-energy ions, typically from an inert gas like argon.
- The bombardment causes atoms from the target to be ejected and deposited onto the substrate (e.g., glass).
- The process requires specialized chilling to manage the heat generated during sputtering.
-
Types of Sputter Coating Techniques
- Magnetron Sputtering: A widely used method for thin film deposition, known for its high speed, low temperature, and low damage characteristics. It is used in industries like semiconductors, optics, and microelectronics.
- Reactive Sputtering: Involves introducing reactive gases (e.g., oxygen or nitrogen) into the chamber to create compound films (e.g., oxides or nitrides).
- HIPIMS (High-Power Impulse Magnetron Sputtering): A technique that uses high-power pulses to achieve dense, high-quality coatings.
-
Applications of Sputter-Coated Glass
- Optical Devices: Used to create functional films with properties like anti-reflectivity, reflectivity, or polarization.
- Architectural Glass: Enhances properties such as energy efficiency, durability, and aesthetics (e.g., low-emissivity coatings).
- Electronics: Provides conductive or insulating layers for devices like displays, sensors, and solar panels.
- Decorative Coatings: Adds aesthetic appeal to glass surfaces for use in interior design or consumer products.
-
Benefits of Sputter-Coated Glass
- Uniformity: The process produces highly uniform and consistent coatings.
- Versatility: A wide range of materials can be sputtered, including metals, oxides, and nitrides.
- Durability: Sputter-coated films are typically more durable and adherent compared to other coating methods.
- Customizability: Properties like thickness, composition, and functionality can be tailored to specific applications.
-
Challenges in Sputter Coating
- Heat Management: The process generates significant heat, requiring specialized cooling systems.
- Cost: Equipment and operational costs can be high, especially for large-scale industrial applications.
- Complexity: Achieving precise control over film properties requires advanced technology and expertise.
In summary, sputter-coated glass is a versatile and high-performance material created through the sputter coating process. It is widely used in industries requiring precise and durable thin films, offering benefits such as uniformity, durability, and customizability. However, the process also presents challenges, including heat management and cost, which must be addressed to optimize its use.
Summary Table:
Aspect | Details |
---|---|
Process | Sputter coating uses high-energy ions to deposit thin films on glass. |
Techniques | Magnetron Sputtering, Reactive Sputtering, HIPIMS. |
Applications | Optics, architectural glass, electronics, decorative coatings. |
Benefits | Uniformity, versatility, durability, customizability. |
Challenges | Heat management, cost, complexity. |
Learn how sputter-coated glass can elevate your projects—contact our experts today!