Sputter coating is a specialized thin-film deposition technique where atoms from a solid target material are ejected into a gas phase due to bombardment by high-energy ions. These ejected atoms then deposit onto a substrate, forming a thin, uniform layer. This process is widely used in industries such as semiconductors, electronics, optics, and healthcare. Applications range from creating computer hard disks and transparent electrodes for solar cells to coating medical implants. The process is highly versatile, enabling precise control over film thickness and composition, making it essential for advanced manufacturing and technology development.
Key Points Explained:
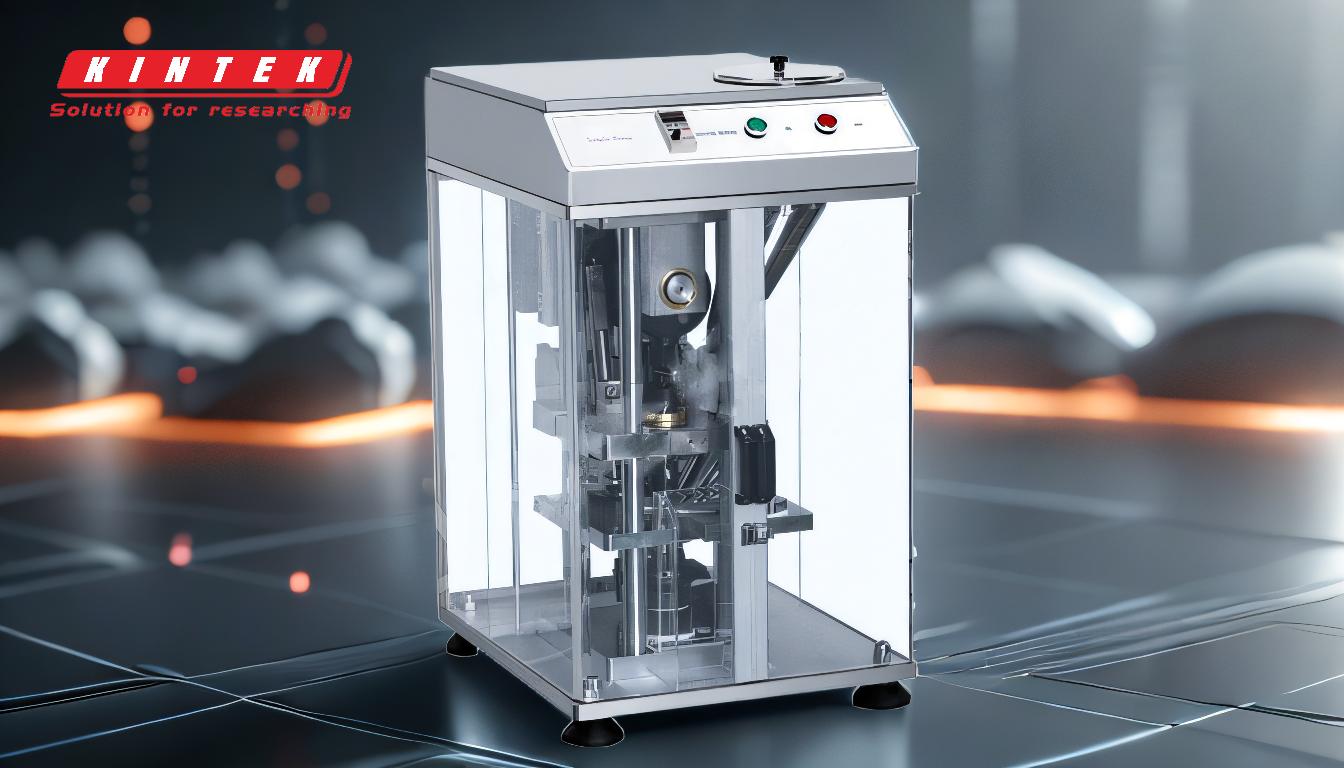
-
Definition of Sputter Coating:
- Sputter coating is a physical vapor deposition (PVD) process where a solid target material is bombarded with high-energy ions, causing atoms to be ejected and deposited onto a substrate.
- This process occurs in a vacuum chamber, ensuring a controlled environment for precise thin-film formation.
-
Mechanism of Sputtering:
- Inert gas ions (e.g., argon) are accelerated toward the target material.
- The collision transfers energy, causing atoms from the target to be ejected.
- These ejected atoms travel through the vacuum and deposit onto the substrate, forming a thin film.
-
Applications in Semiconductors and Electronics:
- Sputter coating is critical in the semiconductor industry for depositing thin films of materials like metals, oxides, and nitrides.
- It is used in the production of computer hard disks, integrated circuits, and TFT-LCD components (e.g., source, drain, and gate electrodes).
- The process enables the creation of transparent conductive films for displays and solar cells.
-
Industrial and Commercial Uses:
- Architectural and anti-reflective glass coatings.
- Solar technology, including thin-film solar cells.
- Automotive and decorative coatings.
- Tool bit coatings for enhanced durability.
- CD and DVD metal coatings for data storage.
-
Medical and Healthcare Applications:
- Sputter coating is used in medical implants to improve biocompatibility and durability.
- Ion-assisted deposition methods are employed to create specialized coatings for implants, driving demand in the healthcare sector.
-
Advantages of Sputter Coating:
- High precision and uniformity in film deposition.
- Ability to deposit a wide range of materials, including metals, alloys, and ceramics.
- Excellent adhesion of the coating to the substrate.
- Suitable for complex geometries and large-scale production.
-
Challenges and Considerations:
- The process requires specialized equipment and a vacuum environment, increasing operational costs.
- Heat generated during sputtering necessitates effective cooling systems.
- Achieving consistent results requires careful control of parameters like gas pressure, ion energy, and target-substrate distance.
-
Future Trends:
- Growing demand in renewable energy applications, such as transparent electrodes for solar cells.
- Expansion in healthcare for advanced medical implant coatings.
- Continued innovation in semiconductor manufacturing, driven by the need for smaller, more efficient devices.
Sputter coating is a foundational technology in modern manufacturing, enabling advancements in electronics, optics, energy, and healthcare. Its versatility and precision make it indispensable for producing high-performance materials and components.
Summary Table:
Aspect | Details |
---|---|
Definition | Thin-film deposition via high-energy ion bombardment in a vacuum chamber. |
Applications | Semiconductors, solar cells, medical implants, and decorative coatings. |
Advantages | High precision, uniform deposition, excellent adhesion, and versatility. |
Challenges | Requires specialized equipment, vacuum environment, and precise control. |
Future Trends | Growth in renewable energy, healthcare, and semiconductor innovations. |
Learn how sputter coating can enhance your manufacturing processes—contact our experts today!