Sputter deposition is a widely used physical vapor deposition (PVD) technique for depositing thin films onto substrates, such as silicon wafers, solar cells, or optical components. It involves the ejection of material from a target source through a process called sputtering, where high-energy ions (typically argon) bombard the target, causing atoms to be ejected and deposited onto the substrate. This method is highly versatile, allowing for the deposition of a wide range of materials, including metals, alloys, and compounds. It is performed under high vacuum conditions to ensure purity and is characterized by its flexibility, reliability, and effectiveness. Sputter deposition is used in various applications, including integrated circuit processing, anti-reflective coatings, and cutting tool coatings.
Key Points Explained:
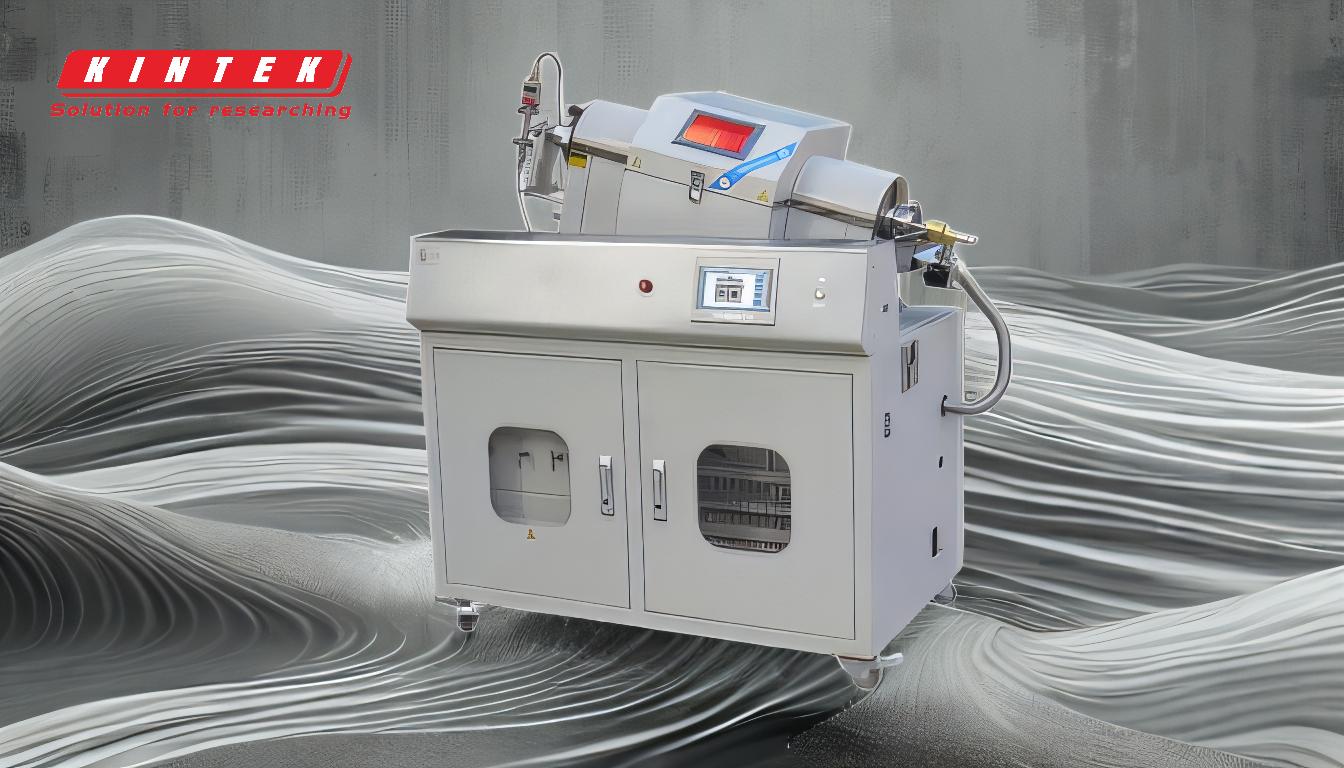
-
Definition and Process of Sputter Deposition:
- Sputter deposition is a physical vapor deposition (PVD) method where material is ejected from a target source and deposited onto a substrate.
- The process involves bombarding the target with high-energy ions (usually argon) in a vacuum chamber. These ions collide with the target, causing atoms to be ejected and deposited onto the substrate.
-
Components Involved:
- Target: The material to be deposited, connected to a negatively charged cathode.
- Substrate: The surface onto which the material is deposited, connected to a positively charged anode.
- Gas (Argon): Used to create plasma, which ionizes and bombards the target.
-
Mechanism of Sputtering:
- Free electrons in the plasma collide with argon atoms, converting them into positively charged ions.
- These ions are accelerated toward the negatively charged target, colliding with it and ejecting target atoms.
- The ejected atoms travel through the vacuum chamber and deposit onto the substrate, forming a thin film.
-
Advantages of Sputter Deposition:
- Flexibility: Can deposit a wide range of materials, including metals, alloys, and compounds.
- Purity: Performed under high vacuum conditions, ensuring high-purity films.
- Uniformity: Produces even and consistent coatings, suitable for applications requiring precise thickness control.
- Versatility: Can be used for various applications, such as integrated circuits, optical coatings, and cutting tools.
-
Applications:
- Integrated Circuit Processing: Used to deposit thin films of conductive and insulating materials in semiconductor manufacturing.
- Optical Coatings: Applied to create anti-reflective or high-emissivity coatings on glass.
- Cutting Tools: Enhances tool durability by depositing wear-resistant coatings.
- CD/DVD Coatings: Used in the production of reflective layers for optical media.
-
Historical Context:
- Sputter deposition was first observed in the mid-19th century by Grove during experiments with direct current (dc) glow discharges.
- It gained commercial applications by the 1930s but was largely replaced by thermal evaporation in the 1950s.
- Interest resurged in the late 1950s and 1960s due to advancements in vacuum technology and the introduction of radio frequency (rf) sputtering for dielectrics.
-
Challenges and Considerations:
- Resputtering: Occurs when deposited material is re-emitted due to ion bombardment, potentially affecting film quality.
- Thermal Damage: Substrates may experience thermal stress during deposition, requiring careful control of process parameters.
- Equipment Complexity: Requires specialized vacuum systems and power supplies, increasing setup and maintenance costs.
-
Future Trends:
- Continued advancements in vacuum technology and power supply systems are expected to improve deposition rates and film quality.
- Growing demand for thin films in renewable energy, electronics, and advanced manufacturing is likely to drive further innovation in sputter deposition techniques.
By understanding these key points, equipment and consumable purchasers can make informed decisions about the suitability of sputter deposition for their specific applications and ensure they select the right materials and systems for their needs.
Summary Table:
Aspect | Details |
---|---|
Definition | A PVD technique for depositing thin films by ejecting material from a target using high-energy ions. |
Key Components | Target (cathode), substrate (anode), and argon gas for plasma generation. |
Advantages | Flexibility, high purity, uniformity, and versatility in material deposition. |
Applications | Integrated circuits, optical coatings, cutting tools, and CD/DVD coatings. |
Challenges | Resputtering, thermal damage, and equipment complexity. |
Future Trends | Improved vacuum technology and growing demand in renewable energy and electronics. |
Discover how sputter deposition can enhance your applications—contact our experts today for tailored solutions!