Sputtering is a physical vapor deposition (PVD) technique used to deposit thin films of materials onto substrates. It involves bombarding a target material with energetic ions, typically from a noble gas like argon, causing atoms to be ejected from the target's surface. These ejected atoms then travel through a vacuum and deposit onto a substrate, forming a thin film. The process is highly versatile and can be used for both conductive and insulating materials, making it suitable for a wide range of applications in industries such as semiconductors, optics, and coatings. Sputtering can be categorized into several types, including DC sputtering, RF sputtering, ion-beam sputtering, reactive sputtering, and HiPIMS, each with unique characteristics and applications.
Key Points Explained:
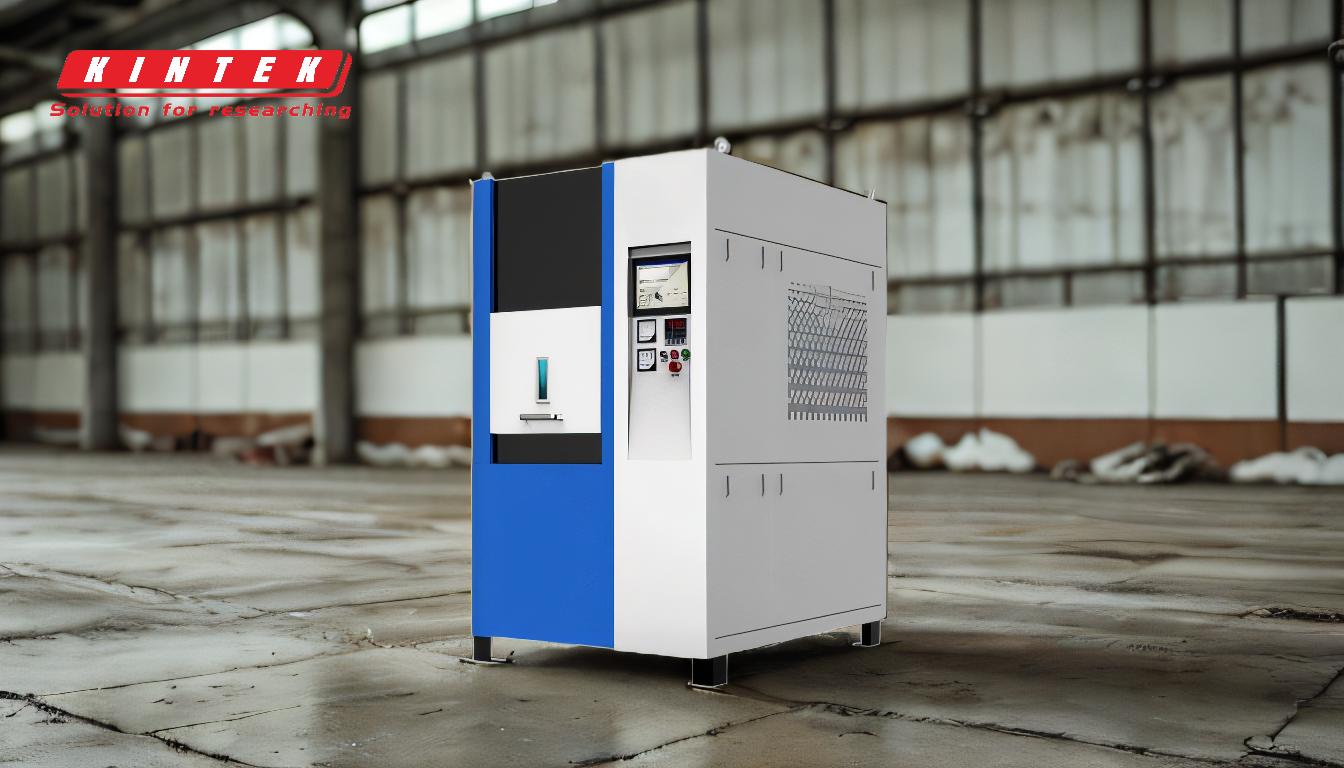
-
Definition and Basic Mechanism of Sputtering:
- Sputtering is a physical process where atoms from a solid target material are ejected into the gas phase due to bombardment by energetic ions, typically from a noble gas like argon.
- The ejected atoms, now in the gas phase, travel through a vacuum and deposit onto a substrate, forming a thin film.
- This process is highly accurate and is used to produce precision coatings and thin films.
-
Key Components of the Sputtering Process:
- Target Material: The material from which atoms are ejected. It can be conductive or insulating.
- Substrate: The surface onto which the ejected atoms are deposited.
- Plasma: Created by ionizing a gas (usually argon) using a potential difference or electromagnetic excitation. The plasma consists of ions that are accelerated toward the target.
- Vacuum Chamber: The process occurs under vacuum conditions to ensure that the ejected atoms travel freely and deposit uniformly on the substrate.
-
Types of Sputtering:
- DC Sputtering: Uses a direct current (DC) power supply to create the plasma. It is commonly used for depositing conductive materials.
- RF Sputtering: Uses radio frequency (RF) power to create the plasma. This method is suitable for depositing insulating materials because it avoids charge buildup on the target.
- Ion-Beam Sputtering: Involves directing a focused beam of ions at the target. This method offers precise control over the deposition process and is often used for high-precision applications.
- Reactive Sputtering: Involves introducing a reactive gas (e.g., oxygen or nitrogen) into the sputtering chamber. The reactive gas reacts with the ejected target atoms to form a compound (e.g., oxides or nitrides) on the substrate.
- HiPIMS (High-Power Impulse Magnetron Sputtering): A variant of DC sputtering that uses short, high-power pulses to create a dense plasma. This results in high-quality, dense films with excellent adhesion.
-
Advantages of Sputtering:
- Versatility: Can deposit a wide range of materials, including metals, alloys, and ceramics.
- High Precision: Produces thin films with excellent uniformity and control over thickness.
- Material Purity: The process can produce chemically pure coatings, as it does not require the use of solvents or other chemicals.
- Substrate Compatibility: Can deposit films on a wide variety of substrates, including those that are not electrically conductive.
-
Applications of Sputtering:
- Semiconductors: Used to deposit thin films of conductive and insulating materials in the fabrication of integrated circuits and other semiconductor devices.
- Optics: Used to create anti-reflective coatings, mirrors, and other optical components.
- Coatings: Used to apply wear-resistant, corrosion-resistant, and decorative coatings on various materials.
- Solar Cells: Used to deposit thin films in the production of photovoltaic cells.
-
Challenges and Considerations:
- Vacuum Requirements: The process must be performed under vacuum, which can be costly and time-consuming.
- Target Erosion: The target material is gradually eroded, requiring periodic replacement.
- Energy Consumption: Some sputtering methods, such as HiPIMS, require significant energy input, which can increase operational costs.
In summary, sputtering is a highly versatile and precise technique for depositing thin films of various materials onto substrates. Its various types, including DC, RF, ion-beam, reactive sputtering, and HiPIMS, offer flexibility for different applications, making it a cornerstone technology in industries ranging from semiconductors to optics and coatings.
Summary Table:
Aspect | Details |
---|---|
Definition | Physical vapor deposition (PVD) technique for thin film deposition. |
Key Components | Target material, substrate, plasma, vacuum chamber. |
Types | DC, RF, ion-beam, reactive sputtering, HiPIMS. |
Advantages | Versatility, high precision, material purity, substrate compatibility. |
Applications | Semiconductors, optics, coatings, solar cells. |
Challenges | Vacuum requirements, target erosion, energy consumption. |
Discover how sputtering can enhance your projects—contact our experts today!