Sputtering is a key technique in physical vapor deposition (PVD) used to deposit thin films onto substrates. It involves the generation of plasma, typically using argon gas, which contains energetic ions and electrons. These ions bombard a target material, ejecting atoms from its surface. The ejected atoms then travel through the plasma and deposit onto a substrate, forming a thin, uniform layer. This process is widely used in industries such as semiconductors, optics, and coatings due to its ability to produce high-quality, dense films with excellent adhesion and low residual stress, even at relatively low temperatures.
Key Points Explained:
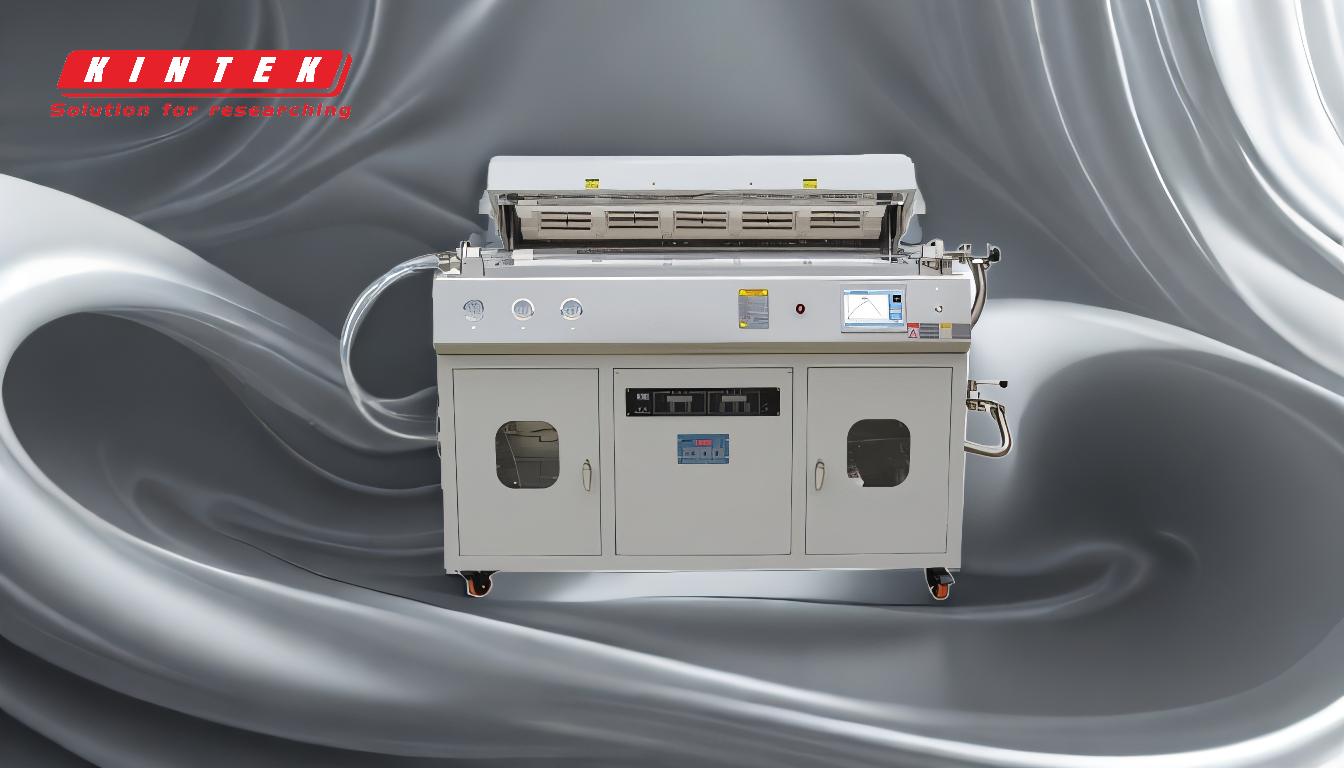
-
Definition of Sputtering:
- Sputtering is a physical vapor deposition (PVD) mechanism where atoms are ejected from the surface of a material (the target) when it is struck by high-energy particles, typically argon ions.
- This process occurs in a vacuum chamber, where a controlled gas (usually argon) is introduced and ionized to create a plasma.
-
Role of Plasma:
- Plasma is a key component in sputtering. It is generated by electrically energizing a cathode within the vacuum chamber, creating a self-sustaining plasma.
- The plasma contains argon ions and electrons, which are accelerated toward the target material due to the electric field.
-
Ion Bombardment and Ejection of Atoms:
- The argon ions in the plasma collide with the target material, transferring their energy to the target's surface atoms.
- When the energy transfer is sufficient, atoms are ejected (sputtered) from the target surface. This process is known as physical sputtering.
-
Deposition of Sputtered Atoms:
- The ejected atoms travel through the plasma and deposit onto a substrate placed within the chamber.
- The atoms form a thin, uniform layer on the substrate, creating a high-quality thin film.
-
Advantages of Sputtering:
- High-Quality Films: Sputtering produces dense, uniform films with excellent adhesion to the substrate.
- Low Residual Stress: The process can achieve low residual stress in the deposited films, which is critical for many applications.
- Versatility: Sputtering can be used with a wide range of materials, including metals, alloys, and ceramics.
- Low-Temperature Deposition: Films can be deposited at temperatures below 150 °C, making it suitable for temperature-sensitive substrates.
-
Applications of Sputtering:
- Semiconductors: Used for depositing thin films in integrated circuits and other electronic components.
- Optics: Applied in the production of anti-reflective coatings, mirrors, and optical filters.
- Coatings: Used for wear-resistant, decorative, and protective coatings on various materials.
- Magnetic Storage: Employed in the fabrication of magnetic thin films for data storage devices.
-
Process Control and Parameters:
- Gas Pressure: The pressure of the argon gas in the chamber affects the sputtering rate and film quality.
- Power Supply: The power applied to the cathode influences the energy of the ions and the rate of sputtering.
- Target Material: The choice of target material determines the composition of the deposited film.
- Substrate Temperature: While sputtering can be performed at low temperatures, controlling the substrate temperature can influence film properties.
-
Comparison to Other PVD Techniques:
- Sputtering is often compared to evaporation, another PVD technique. While evaporation involves heating the target material to produce a vapor, sputtering relies on ion bombardment.
- Sputtering typically produces films with better adhesion and uniformity compared to evaporation, making it the preferred method for many applications.
By understanding these key points, equipment and consumable purchasers can make informed decisions about the use of sputtering in their processes, ensuring optimal performance and cost-effectiveness.
Summary Table:
Key Aspect | Details |
---|---|
Definition | Sputtering is a PVD process where atoms are ejected from a target material by ion bombardment. |
Role of Plasma | Plasma, generated using argon gas, contains ions that bombard the target. |
Advantages | High-quality films, low residual stress, versatility, low-temperature deposition. |
Applications | Semiconductors, optics, coatings, magnetic storage. |
Process Parameters | Gas pressure, power supply, target material, substrate temperature. |
Comparison to Evaporation | Sputtering offers better adhesion and uniformity than evaporation. |
Discover how sputtering can enhance your thin film processes—contact our experts today!