Sputtering is a physical vapor deposition (PVD) technique used to deposit thin films onto substrates. It involves creating a plasma in a vacuum chamber using an inert gas, typically argon. High-energy ions from the plasma bombard a target material, ejecting atoms or molecules from the target. These ejected particles then travel through the vacuum and deposit onto a substrate, forming a thin film. Sputtering is widely used in industries such as semiconductors, optics, and coatings due to its ability to produce high-quality, uniform films with precise control over thickness and composition.
Key Points Explained:
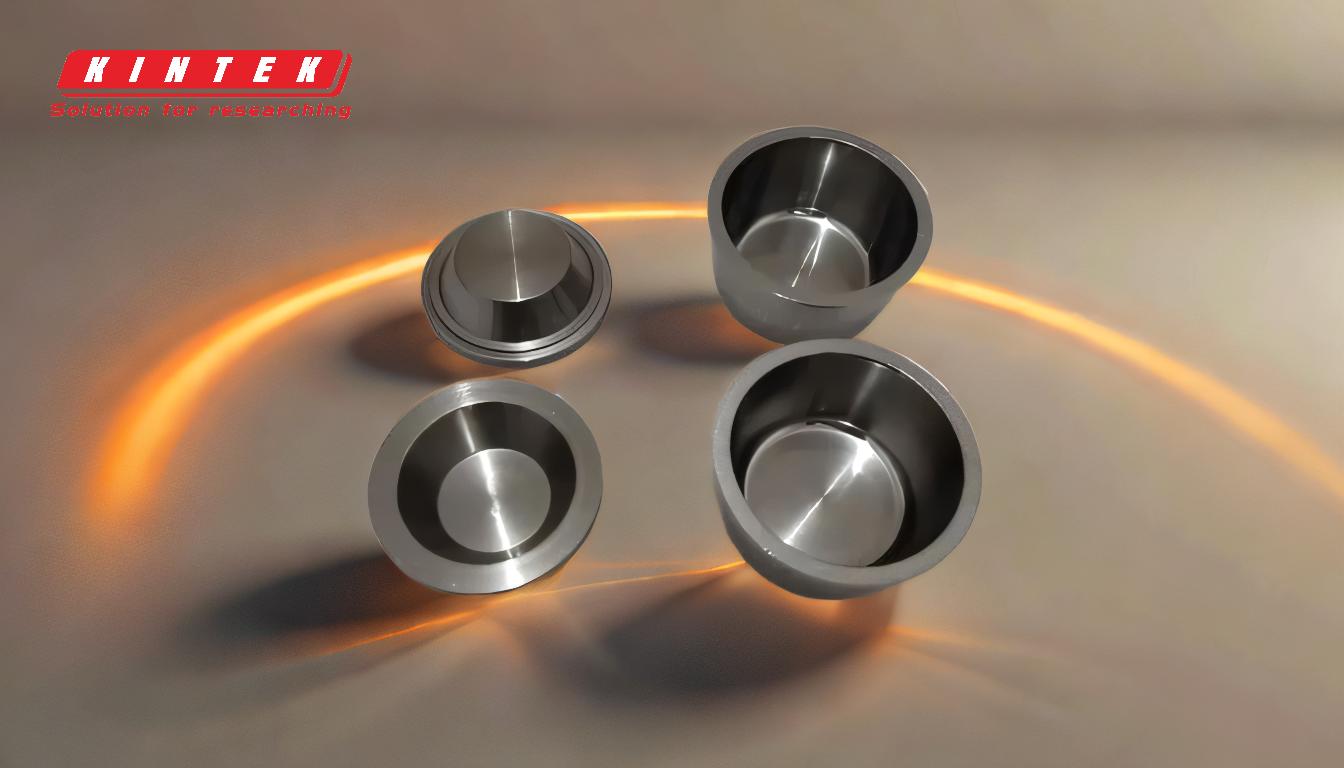
-
Definition and Basic Principle of Sputtering:
- Sputtering is a PVD method where atoms or molecules are ejected from a solid target material due to bombardment by high-energy ions.
- The ejected particles form a vapor stream that deposits onto a substrate, creating a thin film.
- This process occurs in a vacuum chamber to minimize contamination and ensure controlled deposition.
-
Components of the Sputtering System:
- Vacuum Chamber: Maintains a low-pressure environment to prevent contamination and allow efficient particle travel.
- Target Material: The solid material from which atoms or molecules are ejected. It is typically a metal or compound.
- Substrate: The surface onto which the ejected particles are deposited to form the thin film.
- Inert Gas (e.g., Argon): Introduced into the chamber to create a plasma when ionized.
- Cathode and Anode: Electrodes that generate the electric field necessary to ionize the gas and accelerate ions toward the target.
-
Mechanism of Sputtering:
- A voltage is applied between the cathode (target) and anode, creating an electric field.
- Inert gas atoms are ionized, forming a plasma of positively charged ions and free electrons.
- The positively charged ions are accelerated toward the negatively charged target, colliding with it and ejecting target atoms or molecules.
- The ejected particles travel through the vacuum and deposit onto the substrate, forming a thin film.
-
Advantages of Sputtering:
- High-Quality Films: Produces uniform, dense, and adherent films with excellent control over thickness and composition.
- Versatility: Can deposit a wide range of materials, including metals, alloys, and compounds.
- Low Temperature: Suitable for temperature-sensitive substrates.
- Scalability: Can be used for both small-scale research and large-scale industrial applications.
-
Applications of Sputtering:
- Semiconductors: Used to deposit conductive and insulating layers in integrated circuits.
- Optics: Produces anti-reflective, reflective, and protective coatings for lenses and mirrors.
- Magnetic Storage: Deposits thin films for hard disk drives and other magnetic storage devices.
- Decorative Coatings: Creates durable and aesthetically pleasing coatings for consumer products.
-
Types of Sputtering:
- DC Sputtering: Uses a direct current (DC) power supply to generate the plasma. Suitable for conductive target materials.
- RF Sputtering: Uses radio frequency (RF) power to ionize the gas. Can deposit insulating materials.
- Magnetron Sputtering: Incorporates magnets to enhance plasma density and deposition rates, improving efficiency.
-
Considerations for Equipment and Consumables:
- Target Material Selection: Choose materials based on the desired film properties and application requirements.
- Vacuum System: Ensure the vacuum chamber and pumps can achieve and maintain the required pressure.
- Power Supply: Select a power supply (DC, RF, or pulsed) compatible with the target material and deposition process.
- Substrate Preparation: Properly clean and prepare substrates to ensure good film adhesion and quality.
- Gas Purity: Use high-purity inert gases to minimize contamination and achieve consistent results.
By understanding these key points, equipment and consumable purchasers can make informed decisions when selecting sputtering systems and materials for their specific applications.
Summary Table:
Aspect | Details |
---|---|
Definition | PVD method using high-energy ions to eject target atoms for thin film deposition. |
Key Components | Vacuum chamber, target material, substrate, inert gas, cathode, and anode. |
Advantages | High-quality films, versatility, low temperature, scalability. |
Applications | Semiconductors, optics, magnetic storage, decorative coatings. |
Types of Sputtering | DC, RF, and magnetron sputtering. |
Equipment Considerations | Target material, vacuum system, power supply, substrate prep, gas purity. |
Ready to enhance your thin film deposition process? Contact us today to find the perfect sputtering solution for your needs!