Sputtering technology is a physical vapor deposition (PVD) technique used to create thin films on substrates by ejecting atoms from a solid target material through bombardment by high-energy ions. This process occurs in a vacuum chamber where argon plasma is ignited, and argon ions are accelerated toward a negatively charged cathode (the target). The target atoms are dislodged and then deposited onto a substrate, forming a thin film. Sputtering is widely used in industries such as semiconductors, optics, electronics, and medical devices due to its ability to produce high-quality, uniform coatings. Variations like reactive sputtering introduce reactive gases to chemically modify the deposited film, enabling the creation of compounds with specific properties.
Key Points Explained:
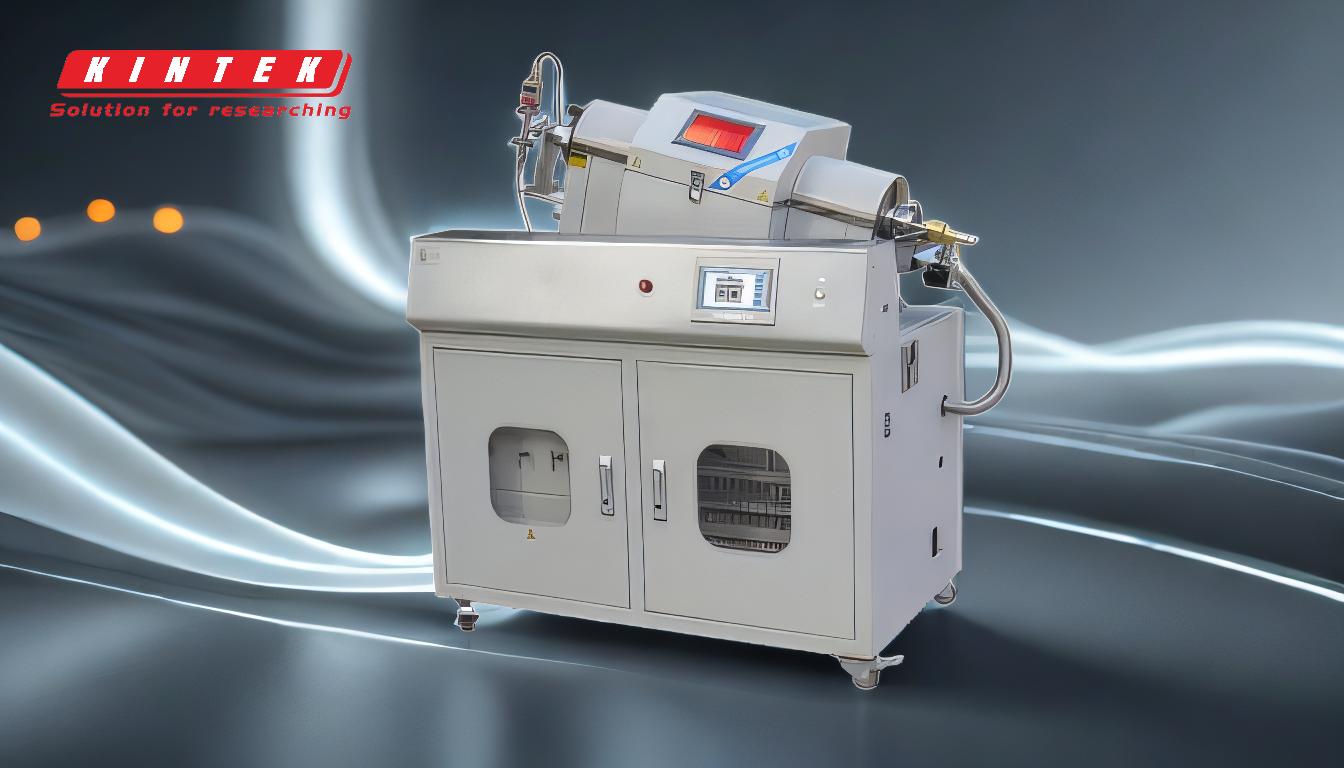
-
Basic Principle of Sputtering:
- Sputtering involves the use of a vacuum chamber where argon plasma is ignited.
- Argon ions are accelerated toward a negatively charged cathode (the sputtering target) using an electrical field.
- The high-energy argon ions bombard the target, dislodging atoms from its surface.
- These ejected atoms diffuse through the chamber and condense onto a substrate, forming a thin film.
-
Types of Sputtering:
- Standard Sputtering: Uses inert gases like argon to eject target atoms, which are then deposited onto a substrate without chemical modification.
- Reactive Sputtering: Introduces reactive gases (e.g., oxygen or nitrogen) into the chamber. The sputtered atoms react with these gases to form compounds (e.g., silicon oxide), resulting in a thin film with a different composition than the original target material.
-
Magnetron Sputtering:
- A more advanced form of sputtering where a magnetic field is used to confine the plasma, increasing the density of ions and improving the efficiency of the process.
- This method produces denser and more conformal coatings compared to traditional evaporation techniques.
-
Applications of Sputtering:
- Semiconductors: Used to deposit thin films of metals and dielectrics in integrated circuits.
- Optics: Produces anti-reflective and reflective coatings for lenses and mirrors.
- Electronics: Creates conductive layers in devices like sensors and displays.
- Medical Devices: Coats implants and instruments with biocompatible materials.
- Energy: Used in the production of solar panels and fuel cells.
-
Advantages of Sputtering:
- Produces highly uniform and dense thin films.
- Allows for precise control over film composition and thickness.
- Suitable for a wide range of materials, including metals, alloys, and ceramics.
- Enables the deposition of complex compounds through reactive sputtering.
-
Gold Sputtering:
- Gold sputtering is widely used in industries such as jewelry, optics, and electronics due to gold's excellent conductivity and corrosion resistance.
- It is also used in scanning electron microscopy (SEM) to coat specimens, improving secondary electron emission and reducing charging effects.
-
Process Conditions:
- Sputtering is typically performed under low-pressure or vacuum conditions to prevent contamination and ensure a clean deposition environment.
- The process is driven by the kinetic energy of the ions, making it highly controllable and reproducible.
By leveraging these principles and techniques, sputtering technology has become a cornerstone of modern thin-film deposition, enabling advancements across a wide range of industries.
Summary Table:
Aspect | Details |
---|---|
Basic Principle | High-energy ions bombard a target, ejecting atoms that form a thin film. |
Types | Standard, Reactive, Magnetron |
Applications | Semiconductors, Optics, Electronics, Medical Devices, Energy |
Advantages | Uniform films, precise control, versatile materials, complex compounds |
Gold Sputtering | Used in jewelry, optics, electronics, and SEM for conductivity and coatings. |
Process Conditions | Low-pressure or vacuum environment for clean, reproducible results. |
Discover how sputtering technology can enhance your projects—contact us today for expert guidance!