Sputtering and evaporation are two primary Physical Vapor Deposition (PVD) techniques used to deposit thin films onto substrates. Sputtering involves bombarding a target material with high-energy ions in a plasma environment, causing atoms to be ejected and deposited onto a substrate. This method offers high purity, precise control, and excellent adhesion. In contrast, evaporation uses thermal energy to vaporize a source material, which then condenses onto the substrate. While evaporation is simpler and offers high deposition rates, it often lacks the uniformity and material versatility of sputtering. Both methods have distinct advantages and limitations, making them suitable for different applications in industries like electronics, optics, and coatings.
Key Points Explained:
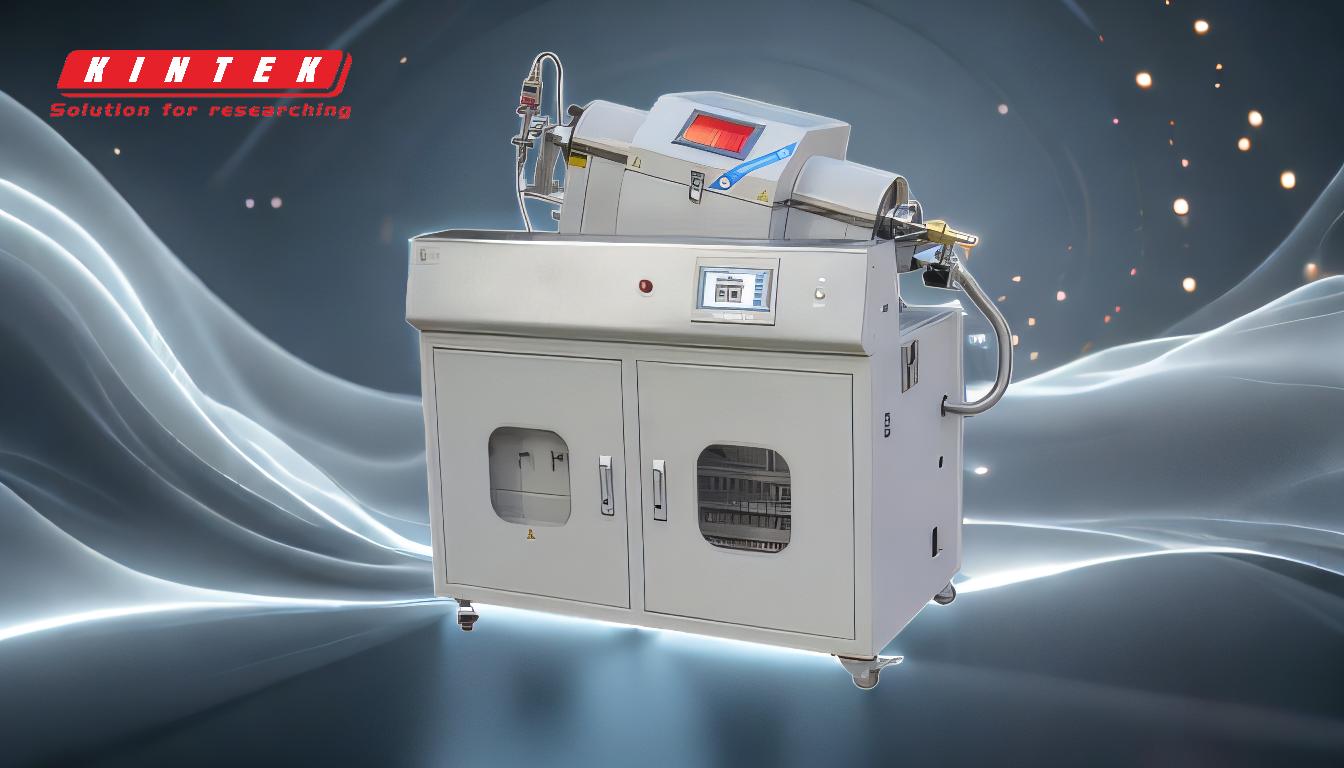
-
Mechanism of Deposition:
- Sputtering: Occurs in a plasma environment where high-energy ions bombard a target material, ejecting atoms that deposit onto a substrate. This process is highly controlled and allows for precise thin-film deposition at the atomic level.
- Evaporation: Relies on thermal energy to vaporize a source material, which then condenses onto a substrate. This method is simpler but less precise compared to sputtering.
-
Deposition Environment:
- Sputtering: Takes place in a plasma environment, often referred to as the "fourth state of nature," characterized by high temperatures and kinetic energies. This results in purer and more precise thin films.
- Evaporation: Utilizes conventional heating methods, making it less complex but also less capable of achieving the same level of purity and precision.
-
Material Compatibility and Versatility:
- Sputtering: Offers greater versatility in terms of material compatibility and can deposit a wide range of materials, including metals, alloys, and compounds. It also allows for greater color versatility through modulation.
- Evaporation: While suitable for a wide range of materials, it is often limited to simpler applications and typically requires additional processes, such as spray painting, to achieve desired colors.
-
Deposition Rate and Uniformity:
- Sputtering: Generally has a lower deposition rate compared to evaporation, except for pure metals. However, it offers better film homogeneity and smaller grain sizes, resulting in more uniform and high-quality films.
- Evaporation: Provides high deposition rates and excellent uniformity when used with masks or planetary systems. However, without these aids, uniformity can be poor.
-
Adhesion and Film Quality:
- Sputtering: Produces films with better adhesion and higher energy of deposited species, leading to superior film quality and durability.
- Evaporation: Films tend to have lower adhesion and are more prone to issues like absorbed gas, which can affect film quality.
-
System Complexity and Cost:
- Sputtering: More complex and expensive due to the need for a plasma environment and precise control mechanisms.
- Evaporation: Simpler and less costly, making it more accessible for basic applications but less suitable for advanced, high-precision tasks.
-
Applications:
- Sputtering: Ideal for applications requiring high precision, purity, and durability, such as in the electronics and optics industries.
- Evaporation: Suitable for simpler applications where high deposition rates and cost-effectiveness are prioritized over precision and film quality.
By understanding these key differences, equipment and consumable purchasers can make informed decisions based on the specific requirements of their applications, ensuring optimal performance and cost-efficiency.
Summary Table:
Aspect | Sputtering | Evaporation |
---|---|---|
Mechanism | High-energy ions bombard a target in a plasma environment. | Thermal energy vaporizes a source material. |
Deposition Environment | Plasma environment (high purity, precise control). | Conventional heating (simpler, less precise). |
Material Versatility | High; compatible with metals, alloys, and compounds. | Limited; suited for simpler applications. |
Deposition Rate | Lower, except for pure metals. | High deposition rates. |
Uniformity | Better film homogeneity and smaller grain sizes. | Good with masks or planetary systems; poor without. |
Adhesion & Quality | Superior adhesion and film quality. | Lower adhesion; prone to absorbed gas issues. |
System Complexity | More complex and expensive. | Simpler and cost-effective. |
Applications | Electronics, optics (high precision, purity, and durability). | Simpler applications (high deposition rates, cost-effectiveness). |
Need help choosing the right PVD technique for your application? Contact our experts today!