Sputtering and evaporation are both physical vapor deposition (PVD) techniques used to deposit thin films, but sputtering offers several advantages over evaporation. Sputtering provides better adhesion due to the higher kinetic energy of sputtered atoms, which results in stronger bonding with the substrate. It also allows for better control over film properties such as roughness, grain size, and stoichiometry, making it suitable for applications requiring high morphological quality. Additionally, sputtering can deposit materials with very high melting points, which are challenging for evaporation techniques. It is also more versatile, as it can be performed in various orientations (top-down or bottom-up) and is preferred for applications like conductive coatings and silicon processing due to its superior step coverage and ease of control.
Key Points Explained:
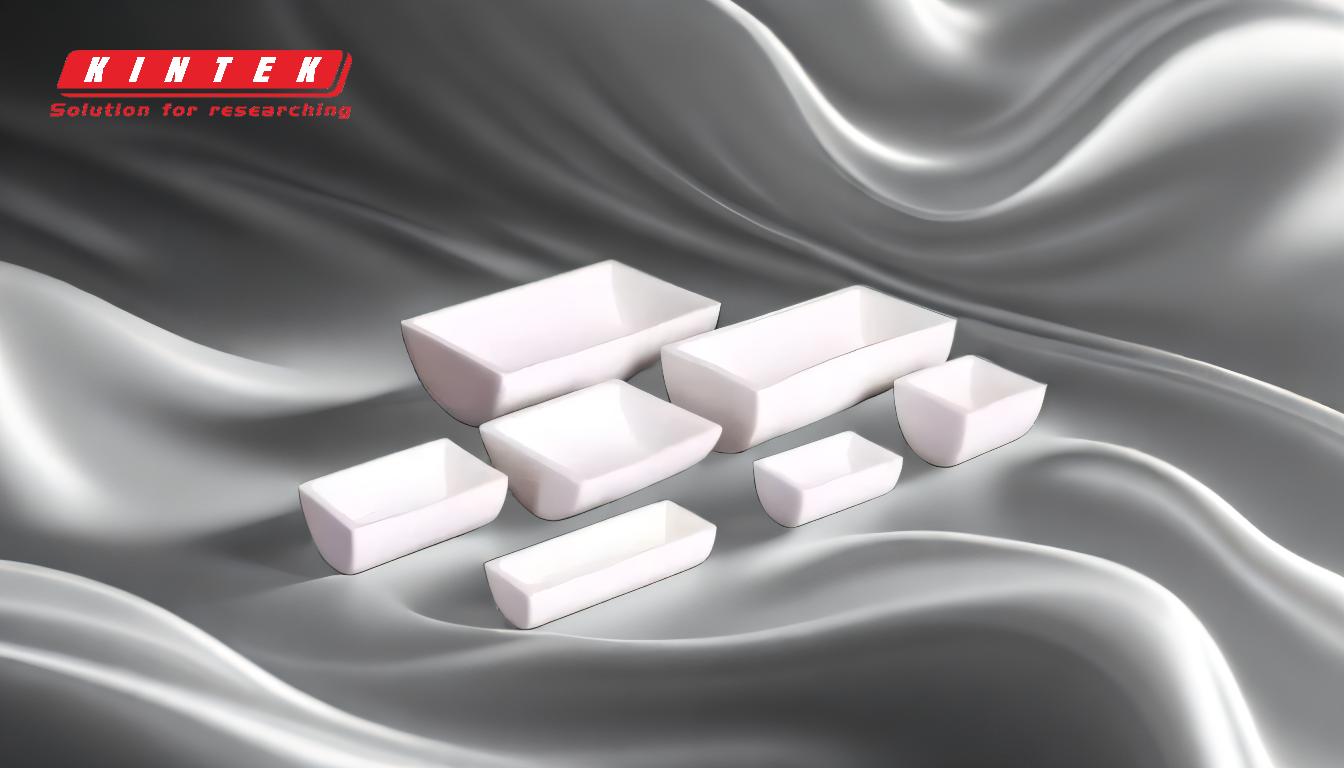
-
Higher Kinetic Energy and Better Adhesion:
- Sputtered atoms have significantly higher kinetic energy compared to evaporated materials. This higher energy leads to stronger adhesion to the substrate, as the atoms can penetrate and bond more effectively with the surface. This is particularly beneficial for applications requiring durable and long-lasting coatings.
-
Superior Morphological Quality:
- Sputtering produces smoother coatings with better control over surface properties such as roughness, grain size, and stoichiometry. This makes it ideal for applications where surface quality is critical, such as in semiconductor manufacturing or optical coatings.
-
Versatility in Material Deposition:
- Sputtering can deposit materials with very high melting points, which are difficult or impossible to evaporate. This expands the range of materials that can be used in thin-film deposition, including refractory metals and ceramics.
-
Better Step Coverage:
- In applications like silicon processing, sputtering provides superior step coverage compared to evaporation. This means that it can uniformly coat complex geometries and high-aspect-ratio features, which is essential for advanced semiconductor devices.
-
Ease of Control and Lower Cost:
- Techniques like DC sputtering are relatively simple to control and cost-effective compared to more complex methods such as RF or HIPIMS. This makes sputtering a preferred choice for applications like gold sputtering and other conductive coatings.
-
Flexibility in Deposition Orientation:
- Sputtering can be performed in various orientations, including top-down and bottom-up configurations. This flexibility allows for greater adaptability in different manufacturing environments and applications.
-
Defect-Free Coatings:
- While not entirely defect-free, sputtering and electron beam evaporation produce coatings with fewer defects compared to arc-based processes. This results in higher-quality films with improved performance characteristics.
By leveraging these advantages, sputtering has become a preferred method for many thin-film deposition applications, offering a combination of superior adhesion, control, and versatility that evaporation techniques cannot match.
Summary Table:
Advantage | Description |
---|---|
Higher Kinetic Energy | Stronger adhesion due to higher energy sputtered atoms, ideal for durable coatings. |
Superior Morphological Quality | Smoother coatings with precise control over roughness, grain size, and stoichiometry. |
Versatility in Material Deposition | Deposits high-melting-point materials, expanding thin-film material options. |
Better Step Coverage | Uniformly coats complex geometries, essential for semiconductor devices. |
Ease of Control and Lower Cost | DC sputtering is simple and cost-effective, ideal for conductive coatings. |
Flexibility in Orientation | Can be performed in top-down or bottom-up configurations for diverse applications. |
Defect-Free Coatings | Produces fewer defects compared to arc-based processes, ensuring high-quality films. |
Ready to enhance your thin-film deposition process? Contact us today to explore sputtering solutions!