The best aluminum alloy for brazing is typically based on the Al-Si system, with a silicon content (w(si)) ranging from 7% to 12%. This system is favored due to its excellent brazeability, strength, color consistency, plating, and corrosion resistance. Specifically, the Al-Si system with a silicon content of 11.7% is a eutectic system, which means it has a eutectic temperature of 577°C, making it a standard brazing material suitable for various aluminum alloys with relatively high melting points. The brazing process requires maintaining a high vacuum level, precise temperature control, and uniform heating to ensure optimal results.
Key Points Explained:
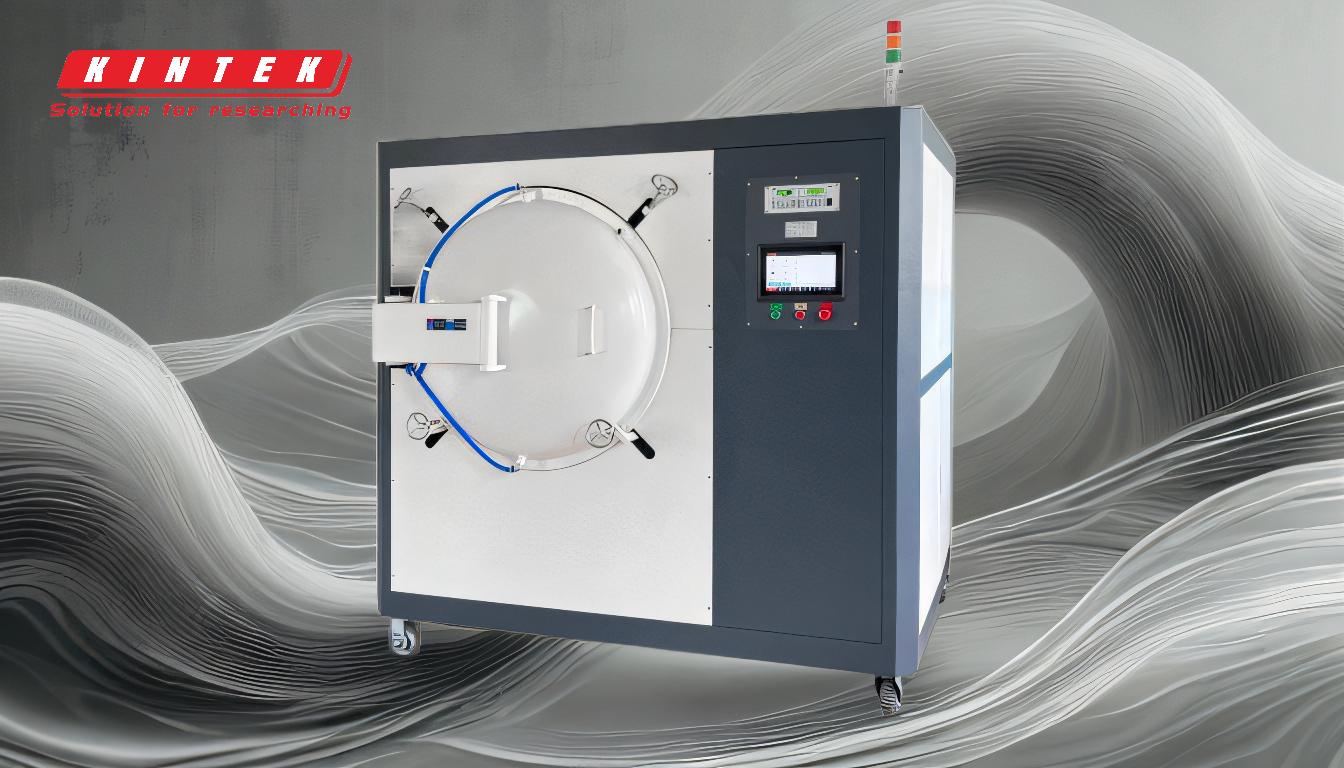
-
Al-Si System as the Best Alloy for Brazing:
- The Al-Si system, particularly with a silicon content of 7% to 12%, is widely regarded as the best aluminum alloy for brazing. This system offers a balance of properties that are essential for effective brazing, including brazeability, strength, and corrosion resistance. The silicon content plays a crucial role in determining the melting point and flow characteristics of the brazing alloy.
-
Eutectic Al-Si System (11.7% Si):
- The Al-Si system with a silicon content of 11.7% is a eutectic system. This means it has a specific composition where the alloy melts and solidifies at a single temperature, in this case, 577°C. This eutectic temperature is advantageous because it allows for brazing at a relatively low temperature compared to other aluminum alloys, reducing the risk of damaging the base material.
-
Benefits of the Al-Si System:
- Brazeability: The Al-Si system provides excellent wetting and flow characteristics, which are essential for forming strong and reliable brazed joints.
- Strength: The brazed joints formed with Al-Si alloys have high toughness and bending strength, making them suitable for structural applications.
- Color Consistency: The alloy maintains the color of the base material, which is important for aesthetic applications.
- Plating and Corrosion Resistance: The Al-Si system offers good resistance to corrosion and can be easily plated, enhancing its durability in various environments.
-
Vacuum Brazing Requirements:
- Vacuum Levels: Maintaining a vacuum level in the range of 10^-5 mbar or better is crucial for preventing oxidation and ensuring the quality of the brazed joint.
- Temperature Control: The parts must be heated to a temperature range of 575-590°C, depending on the specific alloy. Temperature uniformity within ±5.5°C is essential to avoid thermal stresses and ensure even brazing.
- Furnace Type: Multiple-zone temperature-controlled furnaces are recommended to achieve the necessary temperature uniformity and control.
-
Cycle Times and Part Configuration:
- The cycle time for vacuum brazing depends on several factors, including the type of furnace, the configuration of the parts being brazed, and how the parts are fixtured. Proper fixturing ensures that the parts are held in the correct position during the brazing process, which is critical for achieving uniform heating and cooling.
In summary, the Al-Si system, particularly the eutectic Al-Si with 11.7% silicon, is the best aluminum alloy for brazing due to its excellent properties and suitability for vacuum brazing processes. The process requires precise control of vacuum levels, temperature, and part fixturing to achieve optimal results.
Summary Table:
Key Feature | Details |
---|---|
Best Alloy System | Al-Si system (7-12% silicon) |
Eutectic Composition | 11.7% silicon, eutectic temperature of 577°C |
Key Benefits | Brazeability, strength, color consistency, plating, corrosion resistance |
Vacuum Brazing Requirements | High vacuum (10^-5 mbar), precise temperature control (575-590°C ±5.5°C) |
Furnace Type | Multiple-zone temperature-controlled furnaces |
Ready to optimize your brazing process with the Al-Si system? Contact our experts today for tailored solutions!