Sputtering RF (Radio Frequency) bias refers to the application of an alternating electric field in the sputtering process, which allows for the deposition of insulating materials and improves film quality. RF sputtering is particularly useful for non-conductive targets, as the alternating field prevents charge buildup. The bias in RF sputtering influences the energy and direction of ions, impacting the sputtering yield, deposition rate, and film uniformity. By controlling the RF bias, users can optimize the process for specific materials and applications, ensuring better adhesion, reduced defects, and improved film properties.
Key Points Explained:
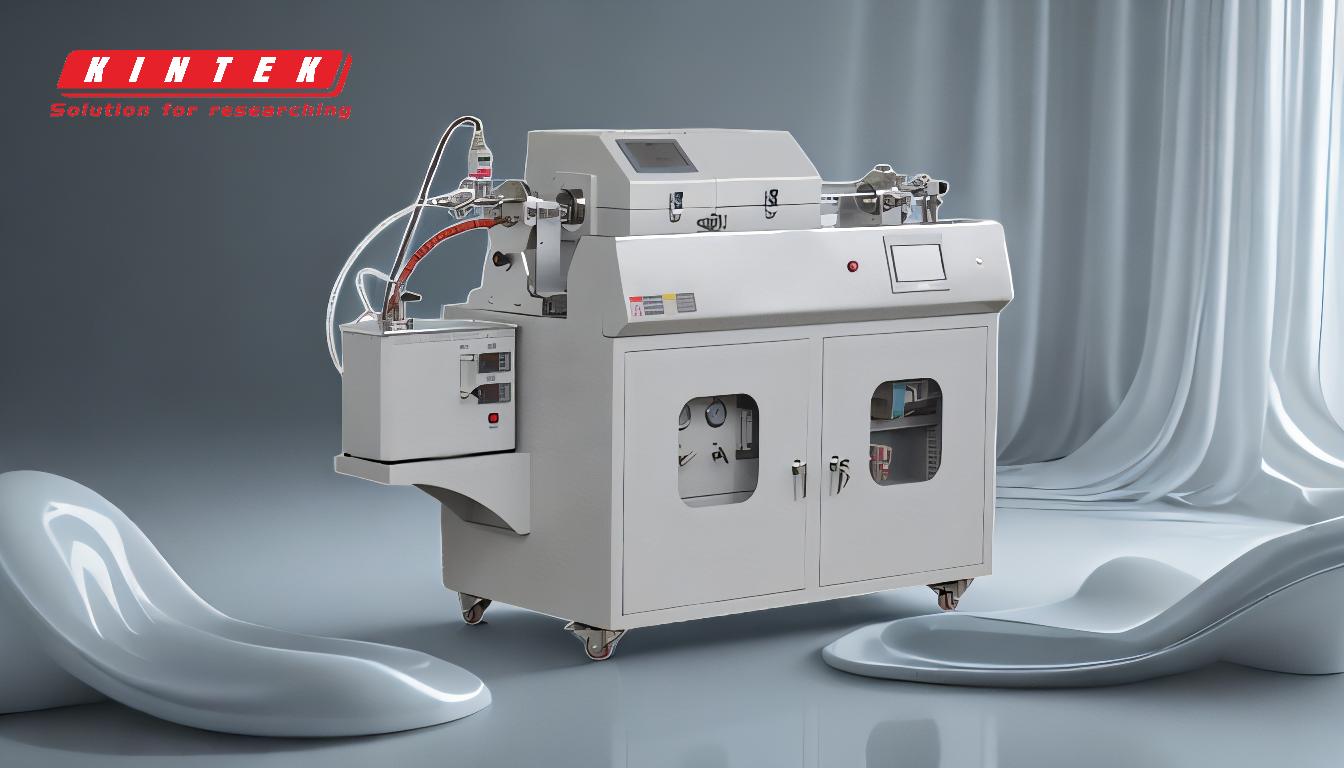
-
Definition of RF Sputtering Bias:
- RF sputtering bias refers to the alternating electric field applied between the target and the substrate in RF sputtering systems.
- This bias alternates at radio frequencies (typically 13.56 MHz), allowing for the deposition of both conductive and insulating materials.
-
Role of RF Bias in Sputtering:
- Charge Neutralization: In RF sputtering, the alternating field prevents charge buildup on insulating targets, which is a limitation in DC sputtering.
- Ion Energy Control: The RF bias controls the energy of ions impacting the target, influencing the sputtering yield and the kinetic energy of ejected particles.
- Directionality: The oscillating field affects the trajectory of ions and ejected atoms, improving film uniformity and coverage.
-
Factors Influencing RF Sputtering Bias:
- Frequency: The frequency of the RF signal (typically 13.56 MHz) determines how quickly the electric field alternates, impacting ion motion and energy transfer.
- Power: Higher RF power increases the energy of ions, leading to a higher sputtering yield but may also cause excessive heating or damage to the substrate.
- Target Material: The binding energy and mass of target atoms influence the sputtering yield and the efficiency of the RF sputtering process.
- Chamber Pressure: Optimal pressure ensures sufficient ion collisions for efficient sputtering while minimizing scattering of ejected particles.
-
Advantages of RF Sputtering Bias:
- Versatility: RF sputtering can deposit both conductive and insulating materials, making it suitable for a wide range of applications.
- Improved Film Quality: The controlled ion energy and directionality result in better film adhesion, reduced defects, and improved uniformity.
- Reduced Arcing: The alternating field minimizes arcing, which is common in DC sputtering with insulating targets.
-
Challenges and Considerations:
- Complexity: RF sputtering systems are more complex and expensive than DC sputtering systems due to the need for RF generators and impedance matching networks.
- Heat Management: High RF power can lead to excessive heating, requiring careful thermal management to avoid substrate damage.
- Process Optimization: Achieving the desired film properties requires precise control of RF power, frequency, and chamber conditions.
-
Applications of RF Sputtering Bias:
- Insulating Films: RF sputtering is widely used for depositing insulating materials like oxides (e.g., SiO₂, Al₂O₃) and nitrides (e.g., Si₃N₄).
- Semiconductor Manufacturing: It is essential for creating thin films in semiconductor devices, such as gate dielectrics and passivation layers.
- Optical Coatings: RF sputtering is used to produce high-quality optical coatings with precise thickness and uniformity.
In summary, RF sputtering bias is a critical parameter in the sputtering process, enabling the deposition of insulating materials and improving film quality. By understanding and optimizing the factors influencing RF bias, users can achieve better control over the sputtering process, leading to superior film properties and broader application possibilities.
Summary Table:
Aspect | Details |
---|---|
Definition | Alternating electric field (13.56 MHz) for depositing conductive/insulating materials. |
Key Role | Prevents charge buildup, controls ion energy, and improves film uniformity. |
Advantages | Versatility, improved film quality, reduced arcing. |
Challenges | System complexity, heat management, process optimization. |
Applications | Insulating films, semiconductor manufacturing, optical coatings. |
Optimize your sputtering process with RF bias—contact our experts today for tailored solutions!