Grinding media balls are essential components in ball mills, used to grind materials into fine powders. Their chemical composition varies depending on the material being ground and the specific requirements of the grinding process. Common materials for grinding media include ceramic balls, flint pebbles, stainless steel balls, brass, bronze, and high-chromium cast iron. Each material has unique properties that make it suitable for specific applications. For instance, high-chromium cast iron grinding balls are composed of elements like carbon, chromium, manganese, silicon, and iron, with trace amounts of other elements like copper and rare earth metals. The choice of grinding media depends on factors such as reactivity, hardness, and the need for contamination-free grinding.
Key Points Explained:
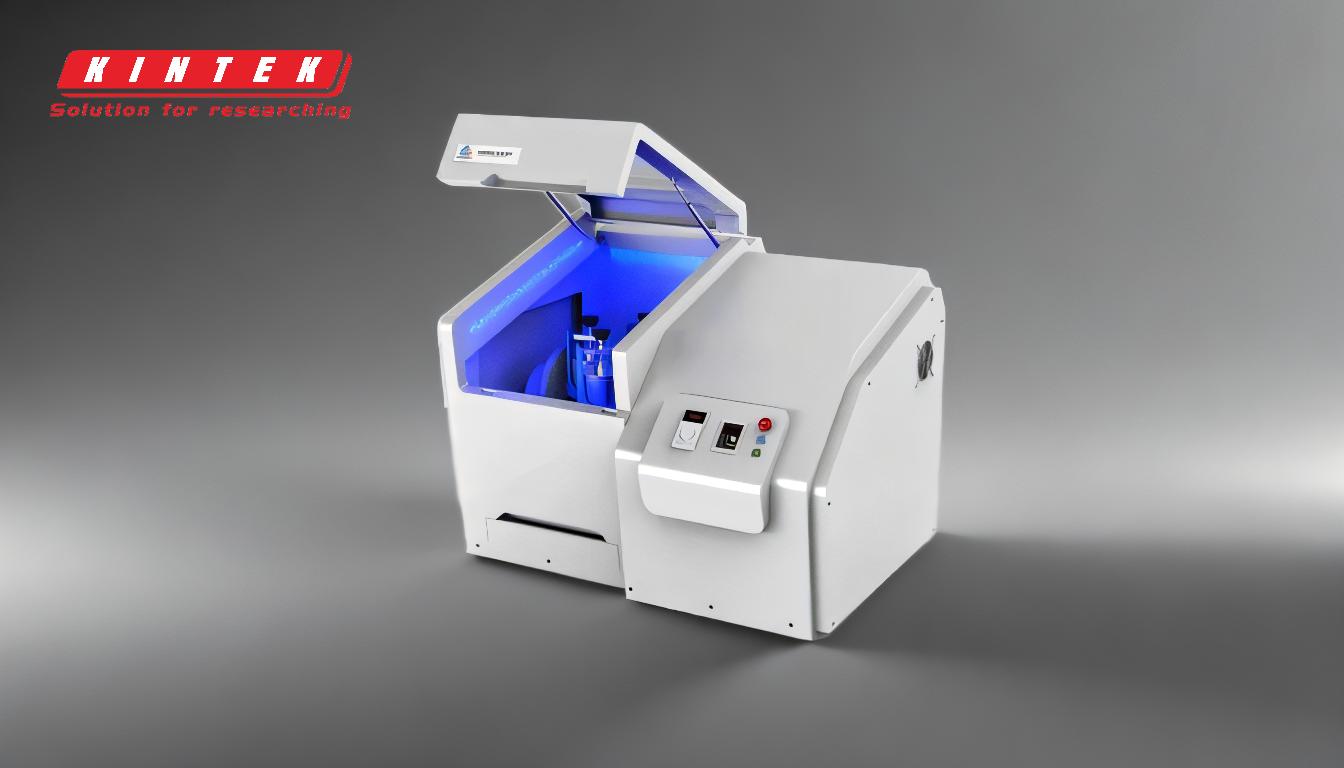
-
Types of Grinding Media Materials:
- Ceramic Balls: Made from materials like alumina or zirconia, ceramic balls are non-reactive and ideal for grinding materials where contamination must be avoided, such as in the pharmaceutical or food industries.
- Flint Pebbles: Naturally occurring and composed of silica, flint pebbles are used for grinding softer materials and are cost-effective.
- Stainless Steel Balls: Known for their durability and resistance to corrosion, stainless steel balls are suitable for grinding harder materials and are often used in industries like mining and chemical processing.
- Brass and Bronze: These alloys are softer than steel and are used for grinding materials that require a non-sparking environment, such as in the production of explosives.
- High-Chromium Cast Iron: This material is highly wear-resistant and is commonly used in mining and cement industries for grinding abrasive materials like iron ore.
-
Chemical Composition of High-Chromium Cast Iron Grinding Balls:
- Carbon (C): 2.0-3.0% - Provides hardness and wear resistance.
- Chromium (Cr): 11.0-16.0% - Enhances corrosion resistance and hardness.
- Manganese (Mn): Less than 1.50% - Improves toughness and hardenability.
- Silicon (Si): Less than 1.50% - Aids in deoxidation and improves strength.
- Copper (Cu): Less than 1.50% - Enhances corrosion resistance.
- Rare Earth Metals (Re): 0.06-0.10% - Improves the microstructure and wear resistance.
- Phosphorus (P): Less than 0.1% - Kept low to avoid brittleness.
- Sulfur (S): Less than 0.1% - Minimized to prevent cracking.
- Iron (Fe): Balance - Forms the base of the alloy.
-
Factors Influencing the Choice of Grinding Media:
- Material Being Ground: The hardness, abrasiveness, and reactivity of the material determine the type of grinding media required. For example, high-chromium cast iron is ideal for grinding abrasive materials like iron ore.
- Contamination Concerns: In industries like pharmaceuticals or food processing, non-reactive materials like ceramic balls are preferred to avoid contamination.
- Durability and Wear Resistance: Materials like stainless steel and high-chromium cast iron are chosen for their long-lasting performance in harsh grinding environments.
- Cost-Effectiveness: Flint pebbles and brass are cost-effective options for less demanding applications.
-
Applications of Different Grinding Media:
- Ceramic Balls: Used in the pharmaceutical, food, and chemical industries for grinding sensitive materials.
- Stainless Steel Balls: Commonly used in mining, cement, and chemical industries for grinding hard and abrasive materials.
- High-Chromium Cast Iron Balls: Ideal for grinding iron ore, cement clinker, and other highly abrasive materials.
- Flint Pebbles: Suitable for grinding softer materials like pigments and dyes.
- Brass and Bronze: Used in industries where non-sparking grinding media is essential, such as in the production of explosives.
By understanding the chemical composition and properties of different grinding media, purchasers can make informed decisions to select the most appropriate media for their specific grinding applications.
Summary Table:
Material | Key Properties | Applications |
---|---|---|
Ceramic Balls | Non-reactive, contamination-free | Pharmaceuticals, food, and chemical industries |
Flint Pebbles | Cost-effective, naturally occurring silica | Grinding softer materials like pigments and dyes |
Stainless Steel Balls | Durable, corrosion-resistant | Mining, cement, and chemical industries |
Brass and Bronze | Non-sparking, softer than steel | Explosives production and non-sparking environments |
High-Chromium Cast Iron | Highly wear-resistant, ideal for abrasive materials | Mining and cement industries for grinding iron ore and cement clinker |
Need help selecting the right grinding media for your application? Contact our experts today for tailored advice!