Thin film deposition is a critical process in various industries, particularly in semiconductor manufacturing, optics, and tribology. The chemical method for thin film deposition primarily refers to Chemical Vapor Deposition (CVD), a widely used technique that involves reacting chemical substances to deposit materials onto a substrate. CVD is known for its precision, ability to produce high-quality films, and versatility in depositing a wide range of materials, including metals, semiconductors, and insulators. This method is especially favored in the semiconductor industry due to its ability to create uniform, high-purity films with excellent conformality over complex geometries.
Key Points Explained:
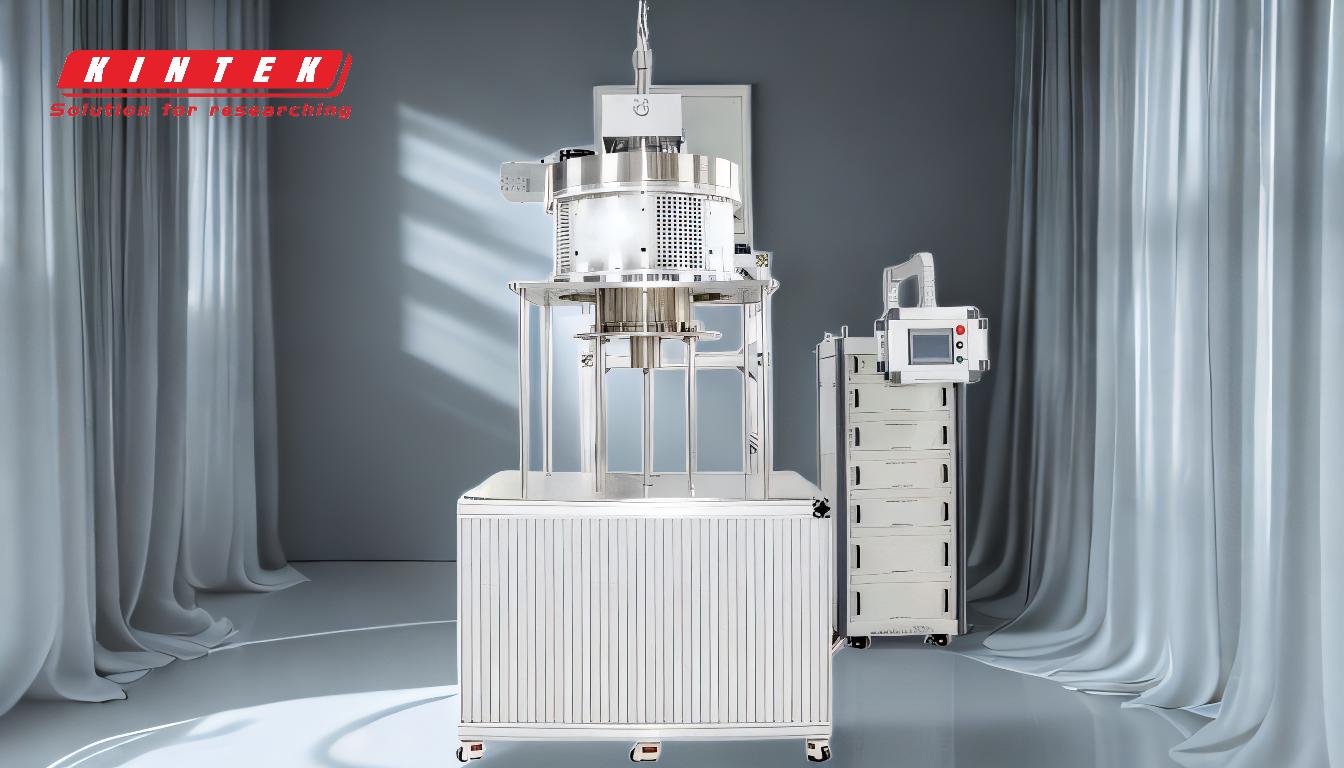
-
What is Chemical Vapor Deposition (CVD)?
- CVD is a chemical method for thin film deposition where gaseous reactants are introduced into a reaction chamber. These reactants undergo chemical reactions on or near the substrate surface, forming a solid film. The by-products of the reaction are then removed from the chamber.
- This method is ideal for depositing materials with low melting points and can produce films with high purity and uniformity.
-
How CVD Works
- Reactant Introduction: Gaseous precursors are introduced into a reaction chamber.
- Chemical Reaction: The precursors react on the substrate surface, forming a solid film.
- By-product Removal: Gaseous by-products are evacuated from the chamber.
- Film Formation: The deposited material forms a thin, uniform layer on the substrate.
-
Advantages of CVD
- High Precision: CVD allows for precise control over film thickness and composition.
- Uniformity: It produces highly uniform films, even on complex geometries.
- Material Versatility: CVD can deposit a wide range of materials, including metals, semiconductors, and insulators.
- High Purity: The process results in films with minimal impurities, making it suitable for high-performance applications.
-
Applications of CVD
- Semiconductor Manufacturing: CVD is extensively used to deposit thin films in the production of integrated circuits, transistors, and other semiconductor devices.
- Optical Coatings: CVD is employed to create anti-reflective, reflective, and protective coatings for optical components.
- Tribological Coatings: It is used to deposit wear-resistant coatings on tools and machinery components.
- Energy Applications: CVD is utilized in the production of solar cells, fuel cells, and batteries.
-
Comparison with Physical Vapor Deposition (PVD)
- While CVD relies on chemical reactions, PVD involves the physical transformation of a target material into a vapor, which is then deposited onto a substrate. PVD is better suited for materials with high melting points, such as metals and ceramics.
- CVD generally offers better conformality and step coverage, making it more suitable for complex geometries.
-
Common CVD Techniques
- Low-Pressure CVD (LPCVD): Conducted at reduced pressures, offering high uniformity and purity.
- Plasma-Enhanced CVD (PECVD): Uses plasma to enhance the chemical reaction, allowing for lower deposition temperatures.
- Atomic Layer Deposition (ALD): A variant of CVD that deposits films one atomic layer at a time, providing exceptional control over film thickness and composition.
-
Challenges in CVD
- High Temperatures: Some CVD processes require elevated temperatures, which can limit the choice of substrates.
- Toxic Precursors: Many CVD precursors are hazardous, requiring careful handling and disposal.
- Cost: The equipment and precursors for CVD can be expensive, making it less suitable for some applications.
-
Future Trends in CVD
- Low-Temperature CVD: Development of techniques that allow deposition at lower temperatures to expand the range of compatible substrates.
- Green CVD: Use of environmentally friendly precursors and processes to reduce the environmental impact.
- Nanostructured Films: Advances in CVD to create films with nanoscale features for applications in nanotechnology and advanced electronics.
In summary, Chemical Vapor Deposition (CVD) is a versatile and precise chemical method for thin film deposition, widely used in industries requiring high-performance coatings. Its ability to produce uniform, high-purity films makes it indispensable in semiconductor manufacturing, optics, and tribology. However, challenges such as high temperatures and toxic precursors must be addressed to further expand its applications.
Summary Table:
Aspect | Details |
---|---|
Definition | CVD is a chemical process where gaseous reactants form a solid film on a substrate. |
Key Advantages | High precision, uniformity, material versatility, and high-purity films. |
Applications | Semiconductor manufacturing, optical coatings, tribology, and energy. |
Common Techniques | LPCVD, PECVD, and ALD. |
Challenges | High temperatures, toxic precursors, and cost. |
Future Trends | Low-temperature CVD, green CVD, and nanostructured films. |
Ready to enhance your thin film deposition process? Contact us today to learn more about CVD solutions!