Chemical vapor deposition (CVD) is a versatile and widely used process in various industries for creating thin films and coatings on substrates such as glass, metals, and ceramics. This method involves chemical reactions between gaseous reagents to deposit a solid film onto a heated substrate. CVD is particularly significant in the production of advanced materials like graphene, carbon nanotubes, and semiconductor films. It is valued for its ability to produce high-quality, large-area coatings at relatively low costs compared to other deposition techniques. The process requires a high level of skill and precision, as it involves controlling temperature, pressure, and gas flow to achieve the desired film properties.
Key Points Explained:
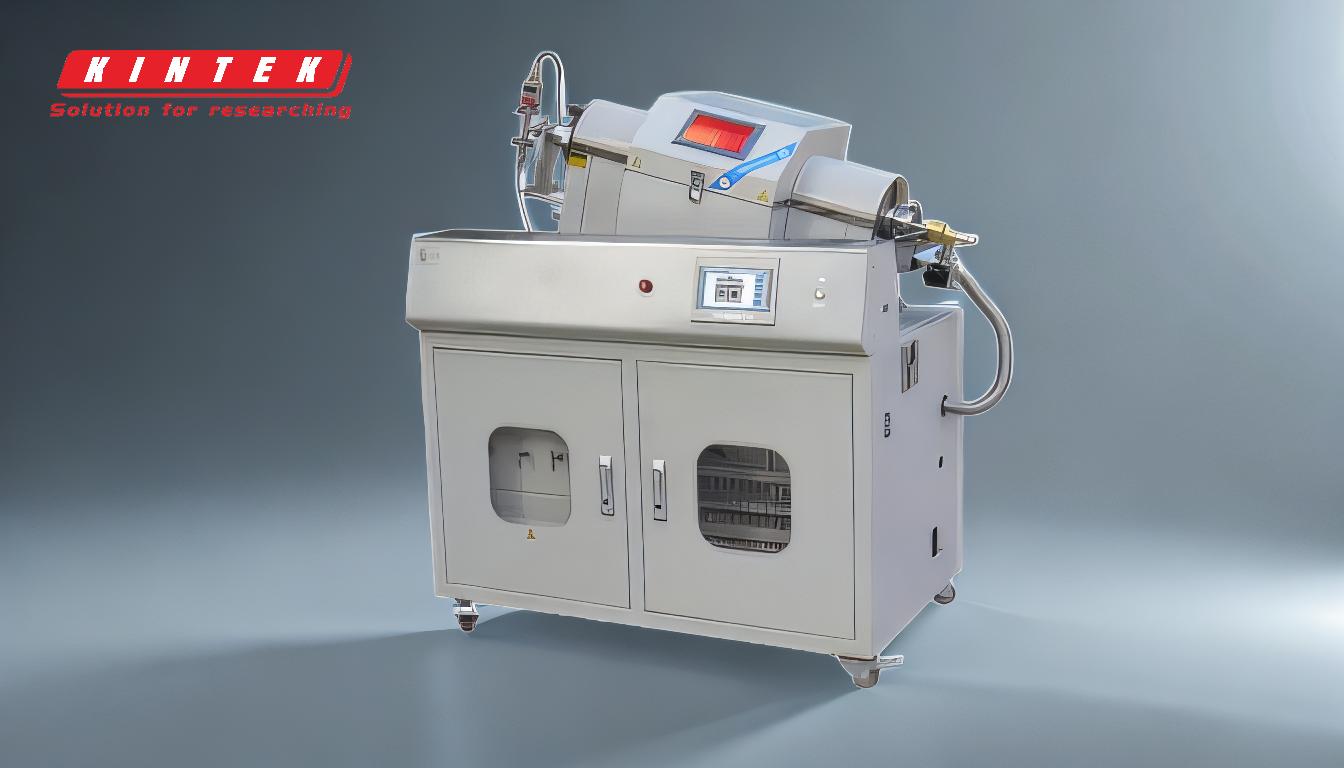
-
Definition of Chemical Vapor Deposition (CVD):
- CVD is a thin-film deposition process where a solid film is formed on a heated substrate through chemical reactions in the vapor phase. The process typically involves gaseous precursors that react or decompose on the substrate surface, resulting in the deposition of a thin, uniform layer. This method is used to create coatings with precise thickness and composition.
-
Applications of CVD:
- CVD is used across various industries, including electronics, optics, and materials science. It is particularly important in the production of graphene, carbon nanotubes, and semiconductor materials like GaN nanowires. The ability to deposit metallic, ceramic, and semiconducting thin films makes CVD a critical process in the fabrication of electronic devices, protective coatings, and advanced materials.
-
Advantages of CVD:
- CVD offers several advantages, such as the ability to produce large-area coatings with high uniformity and purity. It is also cost-effective compared to other deposition methods like sputtering or thermal vapor deposition. Additionally, CVD can be used to deposit a wide range of materials, including metals, ceramics, and semiconductors, making it highly versatile.
-
Process Requirements:
- The CVD process requires precise control of several parameters, including temperature, pressure, and gas flow rates. The substrate must be heated to a specific temperature to facilitate the chemical reactions, and the gaseous precursors must be introduced in a controlled manner to ensure uniform deposition. This level of control demands a high degree of skill and expertise.
-
Comparison with Other Deposition Methods:
- Unlike sputtering, which involves the physical ejection of atoms from a target material, CVD relies on chemical reactions to deposit a film. This makes CVD more suitable for creating complex and high-quality coatings. Similarly, compared to the aerosol deposition method, CVD does not require high-speed particle collisions or additional heat treatment, simplifying the process in some cases.
-
Role in Graphene Production:
- CVD has emerged as a leading method for producing graphene, a material with exceptional electrical, thermal, and mechanical properties. The process is inexpensive and can produce large-area graphene films, making it the most promising approach for commercial graphene production. Since its first successful demonstration in 2008 and 2009, CVD has become the standard method for graphene synthesis.
-
Future Prospects:
- The continued development of CVD technology is expected to expand its applications in emerging fields such as flexible electronics, energy storage, and nanotechnology. Advances in precursor materials, reactor design, and process control are likely to further enhance the capabilities of CVD, making it an even more essential tool in materials science and engineering.
In summary, chemical vapor deposition is a critical process for creating high-quality thin films and coatings across a wide range of industries. Its versatility, cost-effectiveness, and ability to produce advanced materials like graphene and carbon nanotubes make it an indispensable technique in modern manufacturing and research.
Summary Table:
Aspect | Details |
---|---|
Definition | Thin-film deposition via chemical reactions in the vapor phase. |
Applications | Electronics, optics, graphene, carbon nanotubes, semiconductor films. |
Advantages | High-quality, large-area coatings; cost-effective; versatile material use. |
Process Requirements | Precise control of temperature, pressure, and gas flow. |
Future Prospects | Flexible electronics, energy storage, nanotechnology. |
Discover how CVD can revolutionize your material production—contact our experts today!