Chemical vapor deposition (CVD) is a sophisticated process used to deposit high-purity, high-performance solid materials onto a substrate. This technique involves the reaction or decomposition of volatile precursor gases in a controlled environment, typically under vacuum and at elevated temperatures. The gaseous species interact with a heated substrate, leading to the formation of a thin, uniform film on the substrate's surface. CVD is widely used in industries such as semiconductors, optics, and coatings due to its ability to produce materials with exceptional purity and performance characteristics.
Key Points Explained:
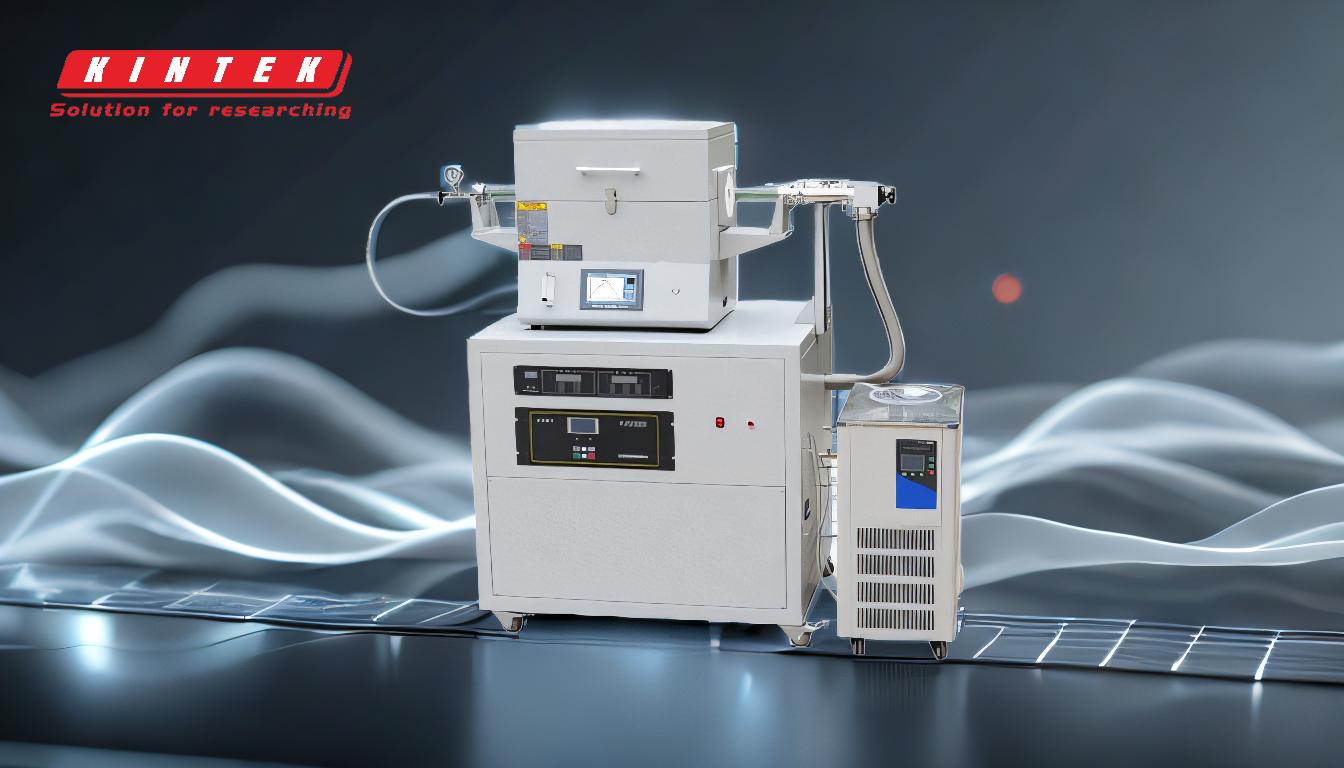
-
Definition and Purpose of CVD:
- Chemical vapor deposition (CVD) is a chemical process designed to create highly pure and durable solid materials. It is commonly used to deposit thin films or coatings onto substrates, which are essential in applications like semiconductor manufacturing, optical coatings, and protective layers.
-
Process Overview:
- The CVD process involves introducing a volatile precursor gas into a reaction chamber under vacuum conditions. The chamber contains a heated substrate, which is the surface where the coating will be deposited.
- The precursor gas reacts or decomposes when exposed to the high temperature of the substrate, forming the desired material. This material then bonds to the substrate's surface, creating a uniform coating.
-
Role of Temperature and Environment:
- The reaction chamber is typically maintained at high temperatures, often exceeding 500°C, to facilitate the decomposition of the precursor gas.
- A controlled atmosphere, often reducing, is used to ensure the proper breakdown of the gas molecules and the deposition of the coating material.
-
Mechanism of Deposition:
- The gaseous species containing the coating element interact with the heated substrate. Thermal energy causes the molecules to decompose, releasing the coating material.
- The released material then deposits onto the substrate's surface, forming a thin, even layer over time.
-
Applications of CVD:
- Semiconductors: CVD is widely used in the production of semiconductor devices, where it deposits high-purity materials like silicon, silicon dioxide, and silicon nitride.
- Optics: It is employed to create anti-reflective coatings, mirrors, and other optical components.
- Protective Coatings: CVD is used to apply wear-resistant and corrosion-resistant coatings on tools and industrial components.
-
Advantages of CVD:
- High Purity: The process produces materials with exceptional purity, which is critical for applications in electronics and optics.
- Uniformity: CVD ensures even deposition of the coating material across the entire surface of the substrate.
- Versatility: It can deposit a wide range of materials, including metals, ceramics, and composites.
-
Challenges and Considerations:
- High Temperatures: The need for elevated temperatures can limit the types of substrates that can be used, as some materials may degrade under such conditions.
- Complexity: The process requires precise control of temperature, pressure, and gas flow rates, making it more complex compared to other deposition methods.
- Cost: CVD equipment and precursor gases can be expensive, which may affect the overall cost-effectiveness of the process.
In summary, chemical vapor deposition is a versatile and highly effective method for depositing thin films and coatings with exceptional purity and performance. Its applications span multiple industries, making it a critical technology in modern manufacturing and materials science.
Summary Table:
Aspect | Description |
---|---|
Definition | A process depositing high-purity solid materials onto substrates via gas reactions. |
Process Overview | Precursor gases decompose on a heated substrate under vacuum, forming thin films. |
Key Applications | Semiconductors, optics, protective coatings. |
Advantages | High purity, uniformity, versatility. |
Challenges | High temperatures, complexity, cost. |
Discover how CVD can enhance your material applications—contact us today for expert guidance!