The Cold Isostatic Pressing (CIP) process is a material processing technique that uses hydraulic pressure to consolidate metal powders into a near-net shape. It leverages Pascal's principle, where pressure applied to an enclosed incompressible fluid is uniformly distributed throughout the fluid and its container. The process involves designing an elastomeric tool, filling it with metal powder, sealing and vibrating it, and then subjecting it to high pressure in a hydraulic fluid-filled vessel. This results in a consolidated part with a density of 75–85%, which is then ready for further post-processing.
Key Points Explained:
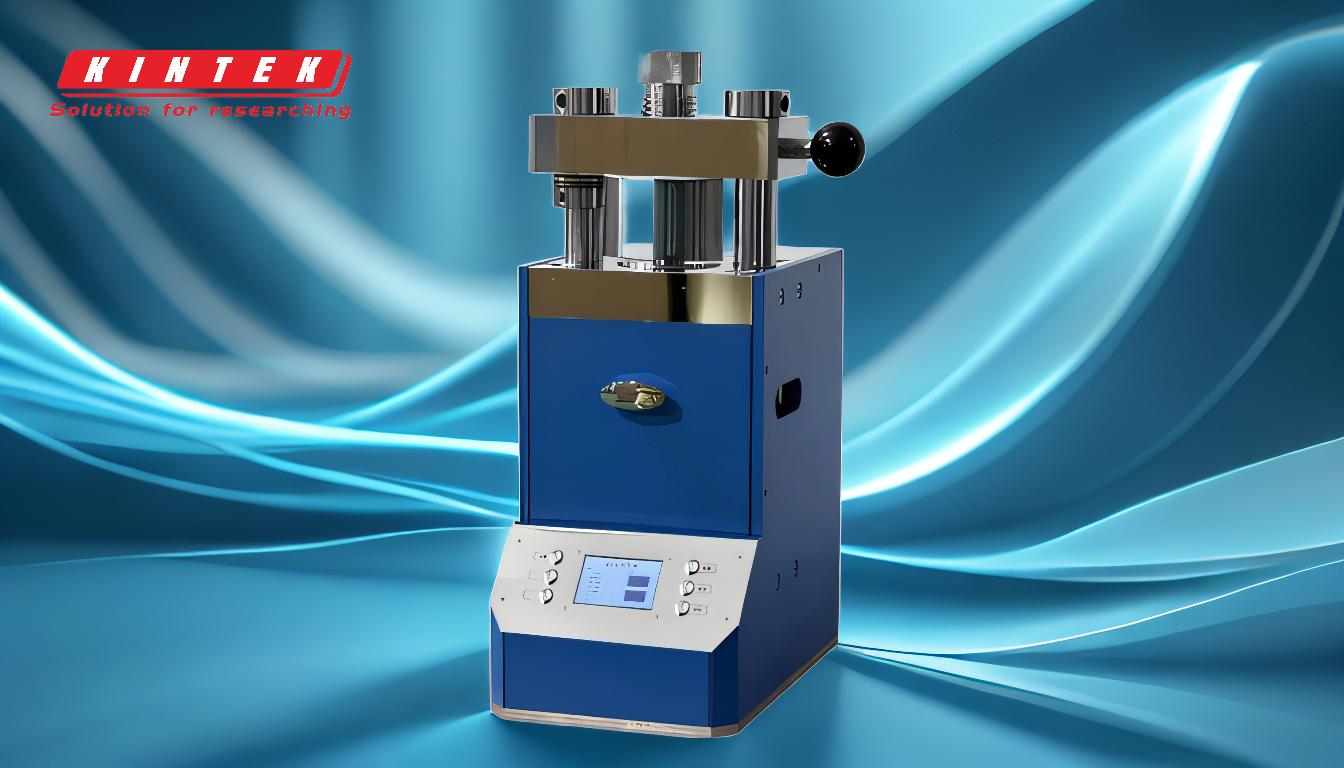
-
Principle of CIP:
- CIP relies on Pascal's principle, which states that pressure applied to an enclosed fluid is transmitted uniformly in all directions.
- This principle ensures that the metal powder is compressed evenly from all sides, leading to uniform density and minimal distortion in the final part.
-
Stages of the CIP Process:
-
Tool Design:
- An elastomeric tool is designed to match the shape of the final part. This tool acts as a mold for the metal powder.
-
Powder Filling:
- A specific amount of metal powder is placed into the elastomeric tool. The type and amount of powder depend on the desired properties of the final part.
-
Sealing and Vibration:
- The tool is closed with a bung and vibrated to reconfigure the powder, ensuring even distribution and reducing voids.
-
Isostatic Compression:
- The encapsulated powder is placed in a pressure vessel filled with hydraulic fluid. High pressure is applied uniformly, compressing the powder isostatically.
-
Pressure Release:
- The pressure is released gradually to allow the tool to retract while the powder consolidates into a solid form.
-
Part Extraction:
- The consolidated part, typically with a density of 75–85%, is extracted from the tool and prepared for further post-processing.
-
Tool Design:
-
Advantages of CIP:
- Uniform Density: The isostatic pressure ensures that the powder is compressed uniformly, leading to parts with consistent density and mechanical properties.
- Complex Shapes: CIP can produce parts with complex geometries that are difficult to achieve with other methods.
- Material Versatility: The process is suitable for a wide range of materials, including metals, ceramics, and composites.
-
Applications of CIP:
- Aerospace: Used to manufacture components like turbine blades and structural parts that require high strength and precision.
- Medical: Produces implants and prosthetics with complex shapes and high biocompatibility.
- Automotive: Used for creating lightweight and high-strength components for engines and transmissions.
-
Post-Processing:
- After CIP, the parts often undergo additional processes such as sintering, machining, or heat treatment to achieve the final desired properties and dimensions.
-
Limitations of CIP:
- Density: The parts produced by CIP typically have a lower density compared to those made by hot isostatic pressing (HIP), requiring further densification steps.
- Tooling Costs: Designing and manufacturing elastomeric tools can be expensive, especially for complex shapes.
- Production Speed: The process can be slower compared to other powder metallurgy methods, making it less suitable for high-volume production.
By understanding these key points, a purchaser or engineer can better evaluate whether the CIP process is suitable for their specific application, considering factors like material properties, part complexity, and production requirements.
Summary Table:
Aspect | Details |
---|---|
Principle | Uses Pascal's principle for uniform pressure distribution. |
Process Stages | Tool design, powder filling, sealing, vibration, compression, extraction. |
Advantages | Uniform density, complex shapes, material versatility. |
Applications | Aerospace, medical, automotive industries. |
Post-Processing | Sintering, machining, heat treatment. |
Limitations | Lower density, high tooling costs, slower production speed. |
Discover how Cold Isostatic Pressing can transform your manufacturing process—contact our experts today!