Plastic pyrolysis is a thermochemical process that breaks down plastic waste into three main products: pyrolysis oil, pyrolysis gas, and pyrolysis residue. The composition of these products varies depending on the type of plastic and the pyrolysis conditions. Pyrolysis oil is a complex mixture of organic compounds, including oxygenated chemicals, polymers, and water. Pyrolysis gas consists of non-condensable gases like methane and hydrogen, while the residue primarily contains carbon black and ash. Wastewater may also be generated if the plastic waste contains moisture. The yields typically range from 30-80% oil, 20-30% carbon black, and 10-20% gas.
Key Points Explained:
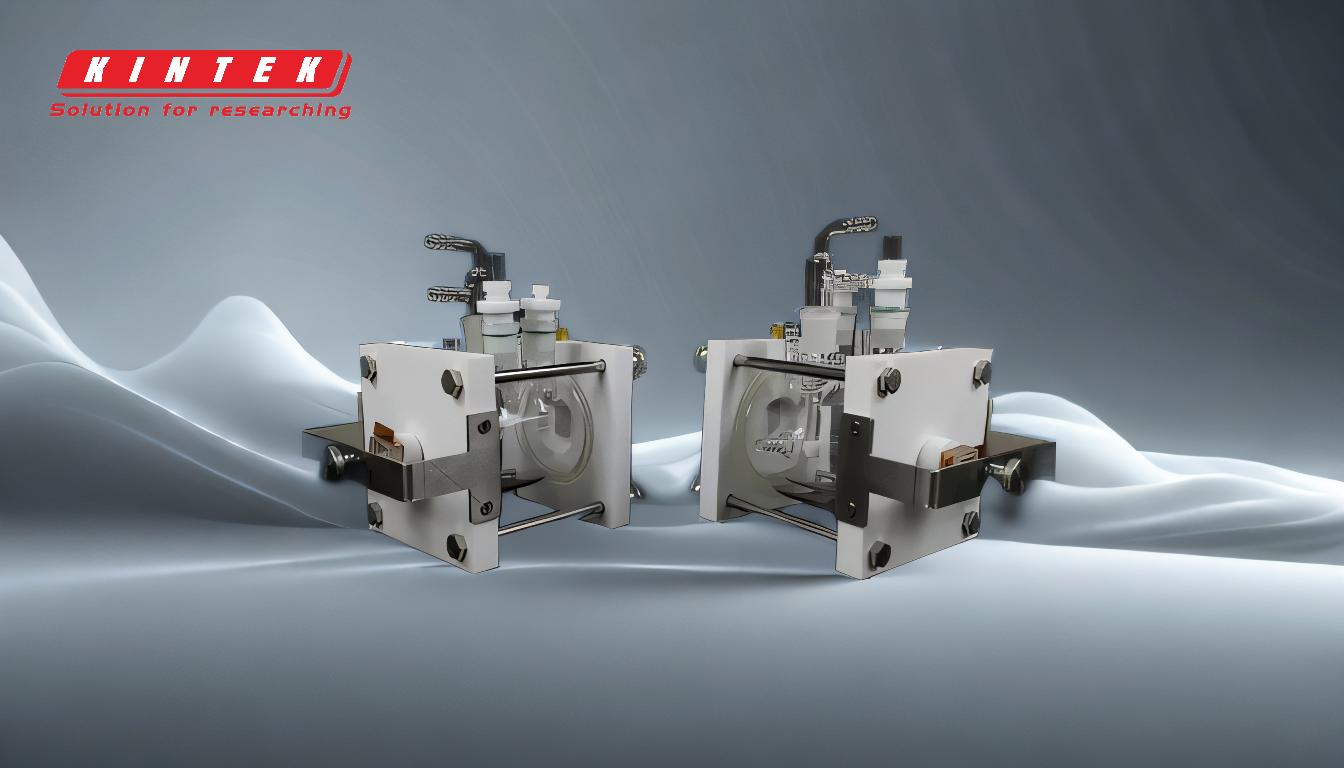
-
Pyrolysis Oil Composition
- Pyrolysis oil is the primary liquid product of plastic pyrolysis, making up 30-80% of the output.
- It is a complex mixture of oxygenated organic compounds, polymers, and water.
- The oil contains up to 40% oxygen by weight and includes a wide range of chemicals:
- Low molecular weight compounds like formaldehyde and acetic acid.
- High molecular weight compounds such as phenols, anhydrosugars, and oligosaccharides.
- The composition of the oil depends on the type of plastic feedstock and the pyrolysis temperature.
-
Pyrolysis Gas Composition
- Pyrolysis gas accounts for 10-20% of the product yield.
- It consists of non-condensable gases, including:
- Light hydrocarbons like methane (CH₄) and ethylene (C₂H₄).
- Hydrogen (H₂) and carbon monoxide (CO).
- These gases can be used as a fuel source for the pyrolysis process or for external energy generation.
-
Pyrolysis Residue Composition
- The solid residue, or char, makes up 20-30% of the pyrolysis output.
- It primarily consists of carbon black, a valuable material used in industries like rubber manufacturing and ink production.
- The residue may also contain ash, which is the inorganic component of the plastic waste.
-
Wastewater Generation
- If the plastic waste contains moisture, wastewater may be generated during pyrolysis.
- This wastewater typically contains dissolved organic compounds and requires proper treatment before disposal or reuse.
-
Factors Influencing Product Composition
- The composition of pyrolysis products is influenced by several factors:
- Type of Plastic: Different plastics (e.g., polyethylene, polypropylene, polystyrene) yield different proportions of oil, gas, and residue.
- Pyrolysis Temperature: Higher temperatures tend to produce more gas and less oil, while lower temperatures favor oil production.
- Reactor Design: The design of the pyrolysis reactor and condenser affects the separation and quality of the products.
- The composition of pyrolysis products is influenced by several factors:
-
Applications of Pyrolysis Products
- Pyrolysis Oil: Can be refined into fuel oil or used as a feedstock for chemical production.
- Pyrolysis Gas: Used as a fuel for heating or electricity generation.
- Carbon Black: Used in rubber products, inks, and coatings.
- Wastewater: Requires treatment to remove contaminants before disposal or reuse.
-
Pyrolysis Plant Components
- A typical pyrolysis plant includes:
- A reactor (or retort for batch processes) where the plastic is thermally decomposed.
- A condenser to separate the liquid and gas products.
- An energy module (furnace) to provide heat for the process.
- Some designs may exclude the condenser if the goal is to produce only solid residue, burning the vapor-gas mixture in the furnace instead.
- A typical pyrolysis plant includes:
By understanding the composition of plastic pyrolysis products, purchasers and operators can optimize the process for specific applications, such as fuel production, chemical feedstock, or material recovery. The variability in product composition highlights the importance of tailoring the pyrolysis process to the type of plastic waste and desired end products.
Summary Table:
Product | Composition | Yield (%) | Applications |
---|---|---|---|
Pyrolysis Oil | Oxygenated organic compounds, polymers, water | 30-80 | Fuel oil, chemical feedstock |
Pyrolysis Gas | Methane, ethylene, hydrogen, carbon monoxide | 10-20 | Fuel for heating, electricity generation |
Pyrolysis Residue | Carbon black, ash | 20-30 | Rubber manufacturing, inks, coatings |
Wastewater | Dissolved organic compounds (if plastic contains moisture) | - | Requires treatment for disposal/reuse |
Ready to optimize your plastic pyrolysis process? Contact us today for expert guidance!