Thin film deposition using the sputtering method is a widely used technique in materials science and engineering. It involves the ejection of atoms from a solid target material due to bombardment by high-energy ions, typically from a noble gas plasma. These ejected atoms then deposit onto a substrate, forming a thin film. Sputtering offers numerous advantages, including the ability to deposit a wide range of materials, precise control over film properties, better adhesion, and compatibility with high-melting-point materials. The process is highly reproducible, can be automated, and is suitable for creating complex films, including oxides and nitrides, through reactive sputtering. It is also maintenance-free and works well in ultrahigh vacuum conditions, making it ideal for advanced applications like epitaxial growth.
Key Points Explained:
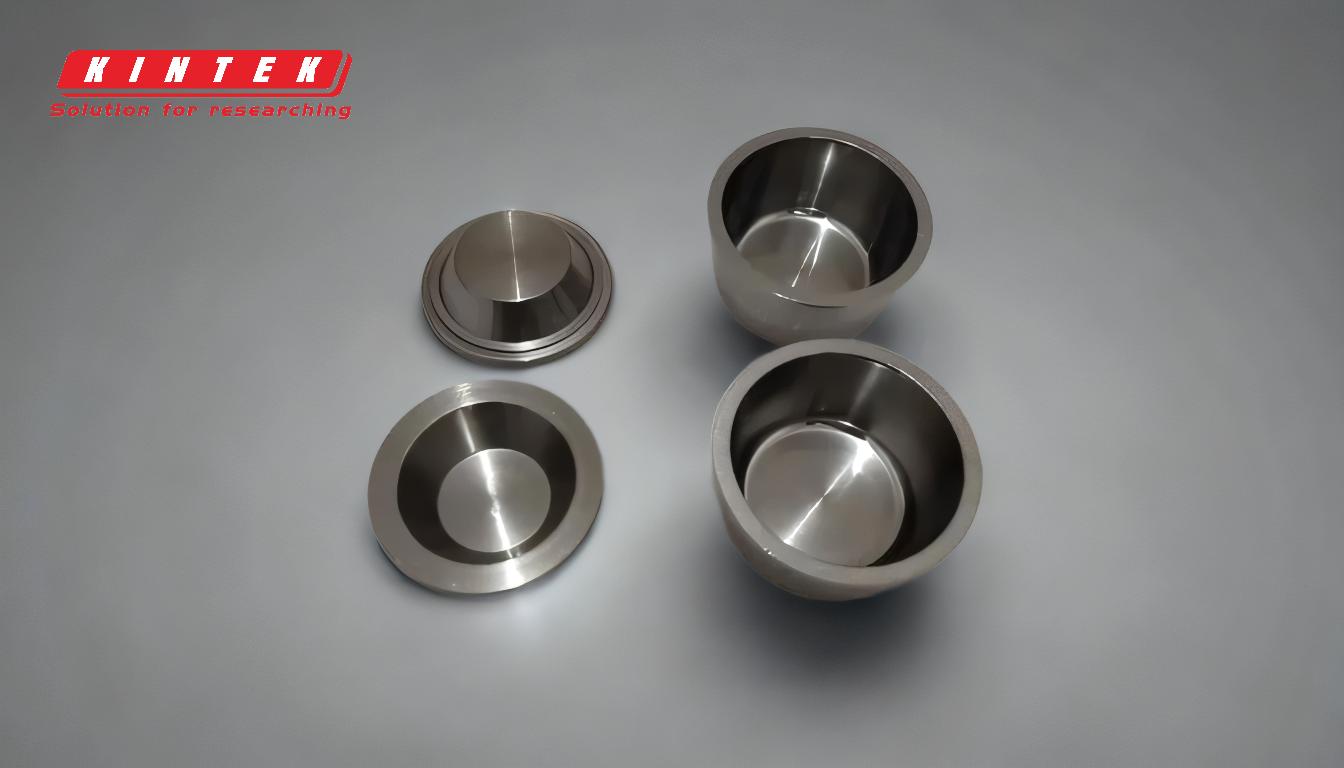
-
Mechanism of Sputtering:
- Sputtering involves bombarding a target material with high-energy ions (usually from a noble gas like argon) in a vacuum chamber.
- The impact of these ions causes atoms from the target to be ejected in a process known as a "collision cascade."
- These ejected atoms travel through the vacuum and deposit onto a substrate, forming a thin film.
-
Advantages of Sputtering:
- Material Versatility: Sputtering can deposit a wide range of materials, including metals, alloys, oxides, nitrides, and even organic compounds. This makes it suitable for diverse applications, from semiconductors to optical coatings.
- High Melting Point Materials: Unlike thermal evaporation, sputtering can deposit materials with very high melting points, such as tungsten or ceramics, which are difficult to evaporate.
- Film Quality: Sputtered films typically have better adhesion to the substrate, higher packing densities, and more uniform thickness compared to films produced by other methods like evaporation.
- Precision and Control: The process allows for atomic-level precision, enabling the creation of pristine interfaces and the ability to tune film properties by adjusting process parameters like pressure, power, and gas composition.
- Low-Temperature Deposition: Sputtering can deposit films at reduced temperatures, making it suitable for temperature-sensitive substrates like plastics or organic materials.
-
Reproducibility and Automation:
- Sputtering is highly reproducible, making it ideal for industrial applications where consistency is critical.
- The process can be easily automated, reducing human error and increasing throughput.
-
Reactive Sputtering:
- Reactive sputtering involves introducing reactive gases (e.g., oxygen or nitrogen) into the sputtering chamber. These gases react with the sputtered atoms to form compound films, such as oxides or nitrides.
- This technique is widely used for depositing optical coatings, dielectric layers, and other functional films.
-
Adhesion and Kinetic Energy:
- Sputtered atoms have higher kinetic energy compared to evaporated atoms, which results in better adhesion to the substrate.
- This high energy also contributes to the formation of dense, high-quality films with minimal defects.
-
Maintenance-Free and Vacuum Compatibility:
- Sputtering systems are relatively maintenance-free and can operate in ultrahigh vacuum conditions, making them suitable for advanced applications like epitaxial growth and semiconductor fabrication.
-
Flexibility in Source and Substrate Configuration:
- The sputtering target can be shaped into various forms (e.g., rods, cylinders, or lines), allowing for flexibility in deposition geometry.
- The source and substrate can be positioned close together, reducing the chamber volume and improving efficiency.
-
Applications of Sputtering:
- Optical Coatings: Sputtering is used to deposit anti-reflective, reflective, and protective coatings for lenses, mirrors, and displays.
- Semiconductors: It is essential for depositing thin films in integrated circuits, solar cells, and sensors.
- Magnetic Storage: Sputtering is used to create thin films for hard drives and other magnetic storage devices.
- Decorative and Functional Coatings: It is employed in industries like automotive and jewelry for depositing durable, decorative, and functional coatings.
In summary, sputtering is a versatile and precise method for thin film deposition, offering numerous advantages over other techniques. Its ability to handle a wide range of materials, produce high-quality films, and operate under various conditions makes it a cornerstone of modern materials science and manufacturing.
Summary Table:
Key Aspect | Details |
---|---|
Mechanism | Bombardment of target material by high-energy ions in a vacuum chamber. |
Advantages | Material versatility, high melting point compatibility, precise control. |
Applications | Optical coatings, semiconductors, magnetic storage, decorative coatings. |
Reproducibility | Highly reproducible and automatable for industrial use. |
Reactive Sputtering | Forms compound films like oxides and nitrides using reactive gases. |
Maintenance | Maintenance-free and compatible with ultrahigh vacuum conditions. |
Discover how sputtering can enhance your thin film processes—contact our experts today!